Furniture making is a craft, and professionals take pride in their designs, skills and custom products. But like other manufacturers, furniture makers must deal with supply-chain issues, from inventory to demanding customers, all of which can be challenging, even problematic, at times. As business picks up and orders increase, so does the need to better manage processes and operations to succeed in a competitive market.
That’s the position that American Woodmark, a Virginia-based manufacturer and distributor of kitchen cabinets and vanities, was in when it began exploring RFID in 2009, to better compete in the remodeling and new-home construction markets. Today, American Woodmark has deployed the technology at seven facilities, as well as at two U.S. and two international suppliers. The company RFID-tags cabinet doors and drawer fronts and tracks them at key points in the manufacturing process, including door build, finishing, quality control, stocking and shipping. The RFID solution has enabled American Woodmark to manage inventory in real time, reduce errors, improve customer service—and achieve a return on investment (see Manufacturer Uses RFID to Put a New Face on Cabinet-Making).
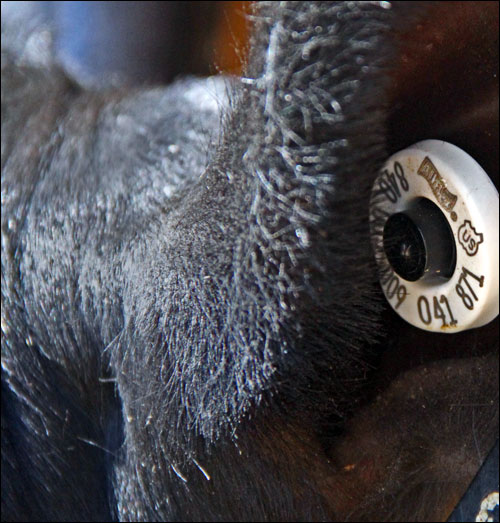
Now that American Woodmark has an RFID “backbone,” David Johnson, the company’s materials technology and projects manager, is thinking about how to employ the technology to further streamline processes. Like other manufacturers, American Woodmark uses programmable logic controllers (PLCs) and computer numerical control (CNC) servers to manage networked machines on factory assembly lines and determine their positioning and motion. Integrating RFID with these systems, Johnson says, would enable fixed readers on the production line to identify the RFID-tagged doors and communicate information such as which edge details they are slated to get, to ensure the appropriate tool heads are automatically loaded for each custom job. “No one has to touch anything to put the right tool head that does the edge detailing on the machine,” he says. “And when the next stack is read, the system will go and load itself with the right tool head for those doors, too.”
Similarly, a production line could be set up to automatically accommodate different door sizes. “The system could just read the tag and know what size door it is working with and what to do with it,” Johnson says. He also foresees the day when RFID will help American Woodmark better manage machinery maintenance. If machine parts were identified with RFID temperature tags, for example, they could be read regularly to see if they comply with the specifications in a database.
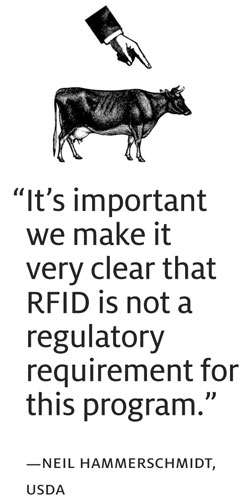
Johnson says American Woodmark’s major competitors have explored the use of RFID for specific applications. They and other custom and office furniture manufacturers “are coming around to RFID,” he says, because they understand how the technology can address manufacturing problems by providing visibility into the production process.
Other furniture makers worldwide are RFID-tagging parts and finished products to track work-in-process and shipments (see Poltrona Frau Uses RFID to Track Leather Materials, Custom Door Maker Turns to RFID to Better Manage Business, RFID Helps IKEA Furniture Maker Eliminate Shipping Errors and Walter Knoll Boosts Accuracy for Product Shipment, Returns). And there was “huge interest” among attendees at last spring’s LIGNA trade show for the woodworking industry in Germany, says Andrej Ermlich, project management head for Abaco Informationssysteme, an RFID systems integrator and software supplier for the furniture manufacturing sector (see RFID Carves Out a Place in Woodworking Industry).
Still, getting RFID to work well in the furniture-manufacturing sector can be tricky business.
Building a Business Case
“We can automate a lot of processes using RFID,” says Kevin Knuth, business development manager for Northern Apex, the systems integrator that worked on the American Woodmark deployment. “If you can find a way to tag a product at the beginning of a process [as American Woodmark does], you can track it as it goes through sanding and finishing lines, or see if it’s been taken off to be reworked automatically.” When the product is complete, RFID tags can be read to verify that trucks headed to retailers or distributors have been loaded with the right product. “That opens up a new world to things like advanced shipping notices,” he says. “Furniture manufacturers can verify what they loaded on a truck and tell the retailer, ‘Here’s what you will be receiving,’ and it all happens automatically.”
An Abaco customer began using RFID three years ago to reduce costs and provide a higher quality of service, Ermlich says. RFID readers are installed on most of the machines to manage CNC programs. “The RFID transponder identifies the part, and the database provides the name or number of the CNC program stored in the machine for drilling, cutting or coating processes,” he says. The project also includes using RFID to manage inventory, monitor work-in-process, automate assembly and optimize logistics, from the loading dock to customer sites.
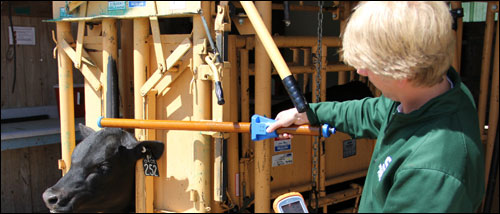
But many furniture makers today are employing RFID to solve specific problems. Pandoor Doors, Israel’s largest manufacturer of custom interior doors, adopted RFID to automate manual production processes, so it could fulfill more orders without introducing potential human errors. Pandoor uses RFID to set up the computer-controlled cutting machines, which are changed for each order. “What if you typed the wrong code or if you pressed the wrong keypad? The last thing you need is a complaint from an angry customer who ordered a left-handle door and got a righty,” says Michal Yanuv Max, sales and marketing director at Tadbik‘s RFID division, which provides Pandoor with RFID labels. Pandoor also uses RFID to automate its painting process, she says.
Another European furniture maker is RFID-tagging pallets of finished furniture from warehouse pickup to truck, to prevent delivery errors—and the unsatisfied customers and additional costs that go along with them, says Erno Berger, account manager at RFID systems integrator Vilant, which worked on the project. “Each outbound gate is equipped with ultrahigh-frequency RFID readers and each pallet is checked as to whether it was loaded to the correct truck, and that no pallets have been left behind from the truck,” he says. This is becoming an important use case, he adds, referring to similar projects and inquiries from potential customers.
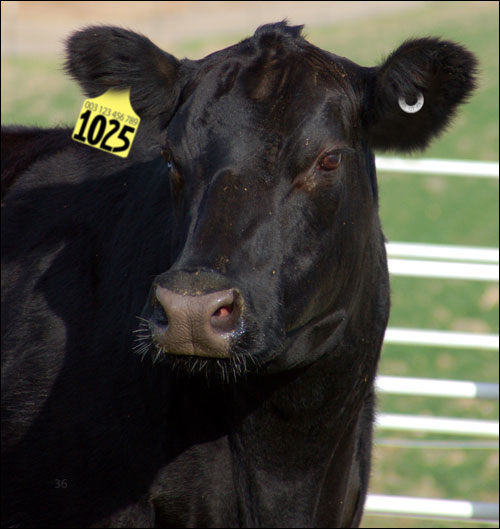
Two Israeli bed manufacturers, Aminach and Hollandia, replaced their bar-code system with an RFID solution, to ensure a complete set of the correct components is added to a delivery order. That way, an installer doesn’t find that a box of screws is missing, and the assembly of a bed or sleep sofa must be delayed.
With the bar-code method, fulfillment employees had to scan each component for a kit and then produce a new bar-code label for the kit, says Uzi Parizat, executive VP at Bos Dimex, an Israeli provider of RFID and supply-chain solutions to the bed manufacturers. “Sometimes, the employees forget or skip one of the kits,” he says. Moreover, bar-coded components have to be set in the product carton with the bar codes facing front so they can be easily scanned, and that’s challenging when multiple components must be included.
For its customers, Bos Dimex provides Tadbik UHF RFID tags for labeling components that are then picked by fulfillment employees using a handheld reader, according to ordering information entered into an enterprise resource planning system and connected to Bos’ proprietary middleware. The tagged items are then placed in a cart for transfer to a station where they are packed in cartons. “All the items and the components are scanned,” Parizat says, “and the ERP checks that there is no missing part or wrong part” before the cartons are loaded onto trucks.
Smoothing Out Rough Edges
Furniture makers that want to use RFID to automate processes first need to reach a certain level of organizational maturity, especially regarding matters related to the in-house flow of materials, Ermlich says. “If the processes you want to optimize by using RFID are not defined enough for at least basic assumptions in that direction, an RFID project would not be advisable,” he says. “You would, on the contrary, increase the amount of chaos, so to speak.”
For some products, specialty tags may be needed, depending on the materials involved, Knuth says. A tag that can be easily read when affixed to a piece of maple may not read at all when used on an item made of medium-density fiberboard laminate, he explains. It’s also important to choose the right type of antennas—and know their appropriate placement and power levels—to get installations in furniture manufacturing facilities functioning correctly, he adds.
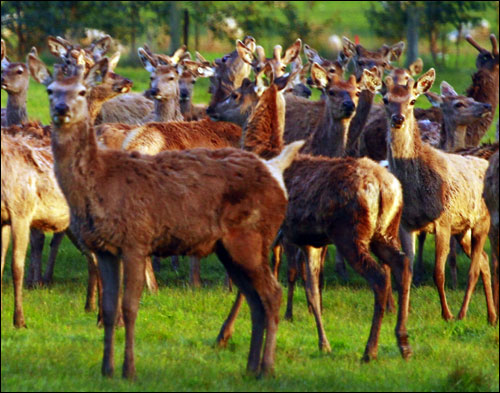
Johnson says one of American Woodmark’s biggest challenges was avoiding extraneous reads in the tag-rich factory floor environment. The company addressed this issue by establishing “keep out” areas to prevent tagged materials outside of the desired flow from passing nearby readers. In places where isolation wasn’t possible, the firm installed shielding and enclosures to block extraneous reads.
Solid Comfort, which makes hotel furniture, faced these issues after it implemented an RFID system in 2010 to track items from final assembly to shipment. Things went well during the pilot, says owner Ryan Larkin, but struggles began during the live implementation, with a full warehouse and readers that would constantly read close-by tags. “We couldn’t really narrow down the antenna scanning to a specific spot,” he says.
Another problem was that completed items—”big bulky furniture made of ¾-inch melamine particleboard,” as Larkin describes them—often had to be wheeled through the RFID portal leading from the production area to the shipping area multiple times, because the labels weren’t in plain sight. Employees wouldn’t realize the tag hadn’t been recognized until they were halfway to the truck and heard the system emit the sound that let them know the read wasn’t successful.
“We tried to make it work for a few years, but it got to the point where it was counterproductive for the business,” Larkin says. Partner AbeTech came in numerous times to help and each time thought the problem was solved, he notes, but issues continued to crop up. “It could have been the software, equipment or users,” he says, “but we just had so many daily obstacles we decided to go back to the bar codes.”
Still, Larkin considers himself a big believer in RFID, noting that the problem of random tag reads might not occur today because his plant has been reconfigured to create more separation between the assembly-line offload and warehouse facilities. He’s open to trying RFID again, but would test it in a real-world setting first. “I do think we learned a lot,” he says. “We learned what doesn’t work, so that is a big win.”
Creating Customer Service
A few years ago, Finnish furniture maker Martela, which manufactures products for offices and public interiors, began attaching passive UHF tags to items after they were delivered to customer sites. As a service to its customers, Martela offers to conduct inventory counts to help organizations comply with government auditing requirements or track assets for internal purposes, and RFID makes the process more efficient. Martela also uses the tags to quickly identify items that need to be replaced and fulfill those orders, as well as track the used pieces as they are either resold or sent out for dismantling and recycling.
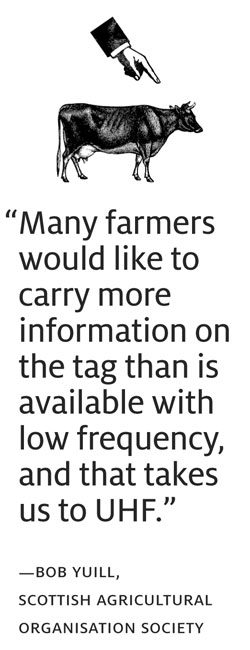
Since then, Martela has updated operations and now can RFID-tag items at production sites, according to Berger at Vilant, which developed the solution. “The process is much easier,” he says. “There is a lot of model variance—for instance, the same chair might come in several different colors—and now all that information can be integrated and linked to the tag from [Martela’s] back-end factory systems right there.” There also have been updates to the reporting service, so inventory reports can be automatically generated as PDF files for customers to review online on demand.
American Woodmark’s Johnson sees an opportunity to improve customer service using RFID. The company would like to equip field-service personnel with USB RFID readers for their smartphones. The RFID tags would remain embedded inside cabinet doors, invisible to customers. If something went wrong— say, a solid wood center panel split—the customer rep could go to the site, read the tag, record the information in a smartphone application and immediately order a new door. This way, the rep wouldn’t have to take measurements onsite and manually input data that could result in potentially ordering the wrong replacement door. “There’s nothing more frustrating to customers than getting that door and not having it fit,” Johnson says. He’s waiting for more RFID chipset builders to accommodate USB RFID readers in a cost-efficient way and is hopeful that will happen this year.
Johnson also envisions harnessing RFID’s power in other ways. If, for instance, American Woodmark were to get multiple reorders from customer service reps for doors to replace those with split panels, the company would have an RFID-enabled e-pedigree to know when and where those doors were built. “For example,” he says, “we measure and record moisture content in our plants. Without RFID, we don’t know when or where these doors were built. But now, with RFID, we can see the entire ePedigree for each door, which could supply a born-on date along with dates for each subsequent process step, and correlate data on environmental and equipment status.”
Today, RFID provides real-time visibility into the manufacturing floor, Johnson says. But, he adds, “we haven’t even scratched the surface of the benefits RFID will provide. It’s exciting to think about five years from now, and how we will still be developing applications off the backbone we built over the last several years.”
Abaco’s Ermlich says his customers have suggested ways to leverage the technology to improve processes. As furniture makers gain more experience working with the technology, he says, they have new insights into how to extend RFID’s benefits.