Lithuanian furniture manufacturer Klaipedos Baldai is employing radio frequency identification to track pallets of products shipped from its facility. With fixed RFID readers installed near dock doors, as well as onboard forklift truck computers that display reader data, the company utilizes the technology to prevent mistakes and improve efficiency for its high-volume shipping of goods to IKEA stores. The solution was provided and installed by Lithuanian automation and telecommunication systems integrator Autepra UAB.
Klaipėdos Baldai is an IKEA supplier of home furniture, including chests of drawers and CD racks. The company sells US$7.5 million worth of goods monthly out of its 20,000-square-meter (215,300-square-foot) warehouse, with all of its products being exported to IKEA’s stores outside of Lithuania. The firm focuses on high-volume output, and thus has an interest in technology that can boost the efficiency of its order-fulfillment and shipping processes. Goods are typically packaged in units composed of unassembled components, and different products can, therefore, often look alike. In addition, shipments typically include mixed pallets, with an assortment of products packed together, making it difficult to ensure that no loading mistakes are made that could result in shipments either missing items or containing incorrect products.
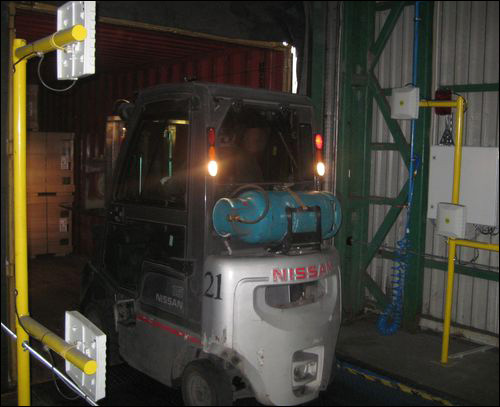
“The main challenge was shipping mistakes,” says Laertas Janušauskas, Klaipėdos Baldai’s production planning manager. The company employed a loading manager whose responsibilities included inspecting each order delivered to the dock doors by forklift drivers, prior to those items being loaded into delivery trucks, in order to ensure that errors were not made. Despite this process being in place, the firm received two to three claims from stores monthly indicating a shipping error had occurred. Such claims cost the company revenue in additional shipments required to correct those mistakes, and also affected customer satisfaction.
To eliminate these errors and improve shipping efficiency with less manual labor, Klaipėdos Baldai sought to use its own SAP system to manage data that would include such details as when a product was loaded, for which customer it was intended, and as part of which order. To test the use of RFID, Autepra UAB first installed a single CAEN RFID R4300P-ION reader, wired to a mobile computer at one the warehouse’s four dock doors, and then tested the read rate for a period of two to three weeks. After determining that the technology performed satisfactorily, says Tomas Girdzevicius, Autepra’s director, the company proceeded with a full deployment, consisting of an R4300P-ION interrogator installed at the loading ramp for each of the four dock doors.
When an IKEA store places an order for products, the company’s SAP software lists the details of the specific order to be filled. Workers gather the components necessary for each ordered item, and pack that item’s components in a box on a conveyor. At the end of the conveyor, the box is placed onto a pallet, along with boxed components of other ordered goods. Once workers finish stacking the pallet, they cover it in stretch-wrap and attach a Smartrac ShortDipole EPC Gen 2 passive ultrahigh-frequency (UHF) RFID tag to the outer stretch-wrap layer. A staff member then utilizes a Nordic ID Morphic UHF RFID handheld reader to link the tag ID to the packed product’s bar-code number, thereby creating a unique ID linked to the product in the SAP software. The software also records other data, such as which personnel accomplished the production work.
The goods may then be stored at the warehouse for a number of days while the remainder of the order is loaded onto pallets, after which the shipment is ready to be placed onto a delivery truck destined for that store. When the pallets are ready for shipment, the forklifts’ computer screens indicate which pallets must be picked, as well as to which dock they should be delivered. The drivers then proceed to retrieve those pallets and bring them to the designated dock door, where an RFID reader captures each pallet’s ID number. The reader forwards that information to the SAP system, which compares each pallet’s ID with the appropriate order for that dock door, ensuring that all of the pallets are correct.
In the event that an incorrect pallet is being loaded, or if a pallet is missing, the SAP software displays an alert on the forklift operator’s mobile computer screen, indicating the problem. The operator can then correct the issue by removing the incorrect pallet, or by adding the missing one. In this way, the company reports, the software prevents shipments errors.
In addition, the system provides Klaipėdos Baldai with an automatic record of which goods were shipped to a specific store, and when this occurred. That data can then be provided to stores if they are concerned about a pending shipment, or if historic information is required to prove what was shipped and when.
The complete deployment was taken live in September 2012, and the company uses approximately 17,000 tags per month. To date, Janušauskas says, the system has eliminated the incidence of shipping-error claims. For management, he adds, “We can see, in real time, which trucks are being loaded, and what products were already loaded.”
According to Janušauskas, the system has also provided data regarding production. Since the tag is encoded and read when an item’s components are boxed, he says, “this works as a flag for end of production and automatic acceptance to stock, so we can see, in real time, exact quantities of products in stock.”
“We’ve gotten no claims from our customers about mixed pallets or other loading mistakes,” Janušauskas reports. This, he says, “grows our customer satisfaction and confidence about our service, and saves our customers’ resources. In the future, we will consider wider usage of RFID technology.” One example he cites involves the use of RFID to track spare parts for machinery utilized onsite.