Container Technology is testing passive RFID tags on its reusable liquid containers and drums so that its customers can better track the whereabouts of those containers within their supply chains.
The container manufacturer, headquartered in Santa Monica, Calif., has been looking into RFID for the past four years, and has just started testing its technology, SmartTrak, with two of its customers, which are chemical manufacturers based in the western United States, according to Gary Clancy, managing director with Container Technology. At the customers’ request, Clancy declined to identify their names.
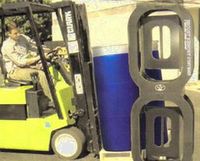
SmartTrak uses the KU-Tag passive UHF RFID technology licensed from University of Kansas’ Information and Telecommunication Technology Center (ITTC), which develops technologies in RFID, telecommunications, information systems, bioinformatics and radar. SmartTrak also includes an RFID portal that uses RFID interrogators chosen to meet each individual customer’s needs, software that aggregates the RFID read data, and design and implementation services.
Complying with the EPC Class 1 Gen 2 air-interface standard, the KU-Tag was developed for use with metals and liquids and has been tested to provide read ranges of up to 20 feet—important features for Container Technology. The company’s liquid containers—which include 55-gallon drums that can cost between $50 and $80, and 330-gallon totes that can cost between $500 and $800—are large and require wide portals or gateways, so the interrogator antennas may not be close to the tags. “We’ve looked at a lot of tags,” Clancy says. “The thing with the KU-Tag is the read distance. For passive tags, the read distance this tag offers is really state of the art.”
Container Technology inserts the tags in clear, plastic covers to protect them from sunlight’s damaging ultra-violet rays and then uses adhesives to affix the RFID tags to the sides of the drums and totes.
Many of Container Technology’s customers, including the two that are testing RFID, currently track their drums and totes using bar codes. But bar codes require line of sight in order to scan the number from the bar code. “As many of our customer’s containers are drums and larger, bar coding becomes an issue due to read distance,” Clancy says. “To be efficient, [our customers] need to read a container while it is on a forklift truck entering or leaving a loading dock.”
Also important was the ability to provide consistent read ranges in either empty or filled containers. Liquid can interfere with RF waves and disrupt an interrogator’s ability to read a tag. The KU-Tag includes a rectangular microstrip (“patch”) antenna and a foil ground plate, with a plastic substrate that separates the foil from the antenna in the middle. The foil ground plate is a thin metal sheet that serves to isolate the antenna from any other metal or fluid that can lower the read range of RFID tags (see University of Kansas’ Tag for Metal, Liquids).
At dock doors at the two customers’ sites, Container Technology has installed interrogators so containers can be scanned to document when they enter and exit the facilities. During testing, expected to last about 90 days, Container Technology is working with the customers to measure read rates and other data to see how well the installations work. If all goes well, Clancy says, the companies plan to extend the tests to full implementations.
Ultimately, Clancy believes, Container Technology’s customers may want to incorporate interrogators throughout their plants so they can track where containers are during the packaging processes. “To incorporate this technology into the packaging/filling connection systems within a manufacturing plant could prevent the wrong product from being packaged,” Clancy says. In addition, he says the chemical makers may also work with their customers so that those companies can track the containers when they arrive and are then shipped backed for refilling.