Evans Distribution Systems, which distributes products that include cookies, has deployed machine-vision technology that makes its picking and packing processes more accurate. The system is being piloted at a single packing line now, with expectations to roll out further in 2020. According to the company, the result has been that customers are receiving the cookie flavors they requested, while the rate of claims related to shipping errors has been nearly eliminated.
The solution, provided by global technology company ADLINK, uses machine vision and artificial intelligence (AI) to identify the products being packed, as well as whether they match a customer’s order. In that way, says Steve Ruch, Evans Distribution Systems’ VP of warehousing, any mispacked boxes can be flagged and repacked in order to prevent any errors from occurring.
The firm has deployed the technology on one of three production lines at which the cookies are being picked and packed for orders. The pilot, launched in January 2020, will be expanded to some other product lines, Ruch says. In fact, the company manages logistics for a variety of consumer brands out of its 409,000-square-foot Detroit facility. The solution, known as Smart Pallet, employs two Gigabit Ethernet cameras, ADLINK’s Edge AI GigE Vision System gateway computer and ADLINK’s Edge software, according to Daniel Collins, the firm’s director for IoT. Packaged cookies are marked and classified as they move along the packing line, orders are pulled from the warehouse order system, and rule-based analytics identify any incorrect contents as they are placed in boxes to fulfill customer orders.
ADLINK has been in operation for more than 25 years to help businesses transfer analog data into digital data for analytics purposes. Even something like a cardboard box, Collins says, can be digitized to gain intelligence. In recent years, the firm has offered machine vision using a camera as a sensor, as well as ADLINK’s AI functionality and software. Traditionally, its customers have been in the transportation, military and factory sectors. ADLINK released Smart Pallet using this technology about three years ago. The solution is intended to help ensure that the right products are in a box, Collins says, and that boxes are loaded onto the correct pallet properly, based on a customer’s order.
Typically, most companies that manually pick products for orders use handheld barcode scanners to confirm what has been packed and palletized. That process can be slow, however, and packers might forgo it entirely if they are in a hurry and are confident that they have packed the product correctly. “It’s not ergonomically friendly [to use a barcode scanner],” Collins notes, “and can cause inaccuracies related to human error.” Scanners can be slow, they can miss a label, and in some cases, if a box or some other item is missed, it will simply remain missing until the pallet or package is received and unloaded.
Ruch has considerable experience managing picking lines and says he understands the labor-intensive process of counting products that were picked in order to ensure claims have not come in from customers due to erroneous shipments. The packing of cookies is fast-paced and high-volume, he reports, and it comes with the potential for errors. In fact, Ruch says, a box of the brand’s cookies is generated every three seconds, and the cookies are shipped at a rate of 20,000 items daily. In this fast-paced environment, several workers are employed at each picking line, dedicated to ensuring the proper packing of each box and pallet.
Last year, Ruch wondered if an automated system was available for detecting packing errors. “I ran into ADLINK at a trade show,” he recalls, “and was telling them what I was trying to do” related to counting the different types of cookie boxes. The two companies then deployed the Smart Pallet system on a single packing line to detect each kind of cookie flavor based on each box’s color and shape. ADLINK also mounted a large screen above the picking line so workers could view details from the Smart Pallet system.
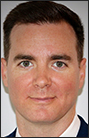
ADLINK’s Daniel Collins
Evans Distribution Systems has eliminated most of its manual processes related to checking packed boxes and pallets on that packing line. The ADLINK system pulls each package’s order by reading data from the shipping label on the side of each box. The system detects what cookies have been placed in the box by identifying each package. “Now,” Ruch states, “someone can just look at a screen, and if there is an error they can see which box is the problem.” Employees can use that information to remove and repack any erroneously packed boxes. By next year, Ruch says he hopes a pneumatic arm could automatically remove any boxes found to have been mis-packed.
Some of ADLINK’s customers are using the system to track when pallets are moved, where they are stored and how forklifts are being operated. For example, the solution could work with cameras mounted on forklifts, as well as above the floor at a staging area where pallets are being filled. By affixing barcodes on the floor, for instance, one of ADLINK’s customers utilizes the system to identify when a barcode is visible, indicating that a particular pallet has been removed from a given location and is thus being loaded onto a truck. That information enables automated processes such as advance shipping notifications.
Other customers are using the technology simply to count boxes that are being shipped, as well as to identify which boxes they are. When cameras are installed on forklifts or other moving objects, the device uses Bluetooth Low Energy (BLE) beacon technology to send data back to the server and thereby identify where the forklift is located.
ADLINK provides its customers with its own smart cameras employing third-party sensors, containerized in an industrial IP 67-rated cover. The technology company provides the machine-learning functionality and enables data to be stored and analyzed. ADLINK has tested a variety of technologies for the Smart Pallet solution and has found machine vision to be the best choice. RFID, for instance, required the tagging of each item, and warehouse workers reading the tags would often capture stray reads from products on other pallets. “We landed on the idea for machine vision,” Collins says, and with machine learning the company could identify what product is being packed based on its size, shape and/or color, and also use AI to identify new products introduced into the system.
ADLINK is currently working on a solution for worker safety that would enable the monitoring of safety features, such as whether workers are in hazardous locations, if they are wearing helmets and if they are distracted by a cell phone. In the meantime, Ruch says, because the cookie production line has gained positive results, he expects that the company eventually won’t need to employ two workers to visually audit each shipment packing job at each line, thereby saving it money in labor costs. He hopes to use the technology next with other products on additional packing lines, such as detecting the proper placement of bottles of liquor and glasses into clear packaging.
One challenge the technology has experienced, Ruch reports, relates to the changing of light levels depending on the time of day. Cookie box colors are more difficult for the system to detect once the sun goes down, he notes. In the future, Evans Distribution Systems may opt to enclose the camera vision space so that only artificial lighting is used, so as to ensure the accuracy of color detection.