Covercraft, a car-cover manufacturer based in Pauls Valley, Okla., is using a Near Field Communication (NFC) RFID solution provided by Shopfloor to help track the clocking-in and movements of operators throughout its plant. The Shopfloor system enables Covercraft to know which tasks were conducted, by whom and when; monitor who was responsible in the event that an error occurs; and pay workers based on the specific quantity of tasks they complete. Several clothing or shoe manufacturers are employing a Shopfloor solution in a similar fashion, with a maker of men’s suits also planning to utilize the technology for a consumer-based application.
Shopfloor, based in Alpharetta, Ga., produces wireless shop floor control (SFC) solutions for manufacturers of apparel and other consumer products. By implementing the company’s Shopfloor Eye software, in conjunction with NFC RFID technology or QR codes, a manufacturer can automate the collection of work-in-progress (WIP) data. But Shopfloor is now considering a consumer-facing use case for some of its customers. If an NFC RFID tag is incorporated into a product, shoppers could use their Android-based devices, with a Shopfloor app, to access data regarding a particular product, such as where, when and how that item was made. They could also view photographs of the product as it was assembled.
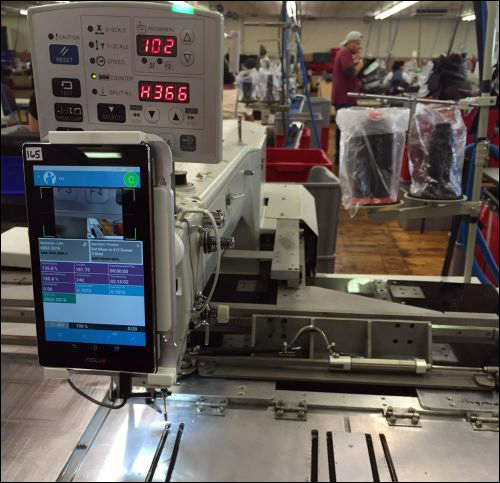
Covercraft, which also makes car-seat and dashboard covers, as well as floor mats and other products, is using the Shopfloor Eye software in conjunction with NFC RFID tags embedded in employee badges and QR codes printed on the products. As an operator begins working at the start of each day, that individual taps his or her badge against the Google Nexus 7 tablet’s built-in reader, then scans a QR code printed on each product. That data is stored so that the company can maintain a record of who provided which processes on that product. The information can be used to identify when a machine or operator is not functioning properly, or where bottlenecks occur. The firm is using QR codes rather than NFC tags since they are less expensive when purchased in large volumes.
A Puerto Rican manufacturer of military products is utilizing the Shopfloor Eye software and NFC RFID tags made with NXP Semiconductors‘ NTAG213 chips to track each pair of shoes through the assembly process, as well as matching that product to the individual workers and machines that carry out the assembly. That data, says Justin Hershoran, a Shopfloor partner, enables inspectors to easily review information, provide their own input and route an item to the repair area, if necessary, before it is sold to the customer.
The company—which has asked to remain unnamed—began using the solution approximately one year ago, and changed its payment model to compensating each employee according to the number of products he or she completed. The new system has since saved about 15 to 20 minutes of each worker’s time (which was previously spent filling out paperwork about which tasks were being performed) while employees’ productivity has increased by 10 to 15 percent, since they are automatically being paid per task completed.
With the system, every pair of shoes is assigned a traveler—a reusable plastic NFC card that remains with its corresponding product until it is fully assembled. Each machine operator and supervisor is also assigned an NFC-enabled badge that, like the traveler, contains an RFID tag with an NTAG213 chip. The unique ID number encoded to the badge tag’s memory is linked to that individual’s name and work title in the Shopfloor Eye software, which resides on the company’s server.
Once a pair of shoes is prepared for assembly, a traveler card is linked to that product, including the footwear’s description and serial number in Shopfloor Eye. The shoes then move through a series of stations to be stitched, glued or trimmed. At each location, a worker is assigned to a specific machine. When the product arrives, the worker uses a Samsung Android-based tablet to scan the NFC tag embedded in his badge, along with the NFC tag in the traveler card. The worker then completes his work on the product, and the Shopfloor Eye software stores that event.
The software can provide that data to the company’s management for historical information. This enables the firm to identify how long it takes a specific worker to complete each process.
When a pair of shoes are fully assembled, an inspector looks them over for any errors, such as a seam not having been properly glued. In the event that an error is detected, details about the flaw are input in the Shopfloor system, and pictures are taken to be stored along with the product’s tag ID, after which the shoes are forwarded to another operator, who addresses such issues. Once the repair worker receives the footwear, he can read the traveler card, access the inspector’s notes and pictures, and quickly complete the repair work. Without the technology, personnel often had to locate the appropriate inspector and ask him to point out the problem.
The shoe company can also use the data to identify any workers who may be repeatedly making mistakes, or when a specific machine might be causing problems. If a supervisor is required at any specific workstation—for example, to correct a machine error—that individual taps his or her card against the reader tablet at the workstation to create a record of that event as well.
In addition, the company utilizes the data provided by the software to pay its workers. Since each completed workstation task is stored with a worker’s ID, she can be paid according to how many products she completed during each shift. She can also view her payment history and view the number of tasks she has completed to date on any specific day, simply by scanning her badge. The system can show her not only that information, but also how much money she has earned so far.
Since the system was taken live, Hershoran says, the shoe company has found that workers are more efficient—not only because they spend less time manually recording their activities, but also because they have an incentive to work faster since they are being paid according to the number of products they complete during a given shift.
When NFC technology is being used to track WIP, Hershoran says, tags could be permanently attached to products, if a company so chooses. “Once a product’s complete, the manufacturers have a choice,” he adds. By permanently embedding the NFC tags, a firm could provide a way to continue identifying each product even after it is provided to the customer. This could prove useful, for instance, if merchandise is returned due to a defect.
In the long run, Hershoran reports, Shopfloor aims for its customers to use NFC technology not only to improve their own work processes, but also to offer extra value to their consumers. If an NFC tag were to remain with a product when it was delivered to a store, shoppers could scan that tag to learn more about it—either after bringing it home, or before making a purchase. “In that way,” Hershoran says, “even 20 years down the road, every jacket would have a story to tell.”
Shopfloor is currently in discussions with a U.S. men’s suit manufacturer to implement the technology for work-in-progress tracking, and to allow consumers to access product information while in stores. The tag would be sewn permanently into each clothing item, such as a jacket. During manufacturing, data could be collected about that item, including information regarding the fabrics, the work being performed on the product and pictures of the item as it is being assembled. Operator names or other information could be provided as well. In that way, a consumer could learn information about an item before paying for it.
Shopfloor is in discussions with potential customers about using NFC RFID tags as a consumer-based feature that could make a high-end product more desirable, and is also working to establish a standard with regard to where NFC tags should be applied to products so that shoppers could easily find and scan labels while shopping or after making purchases. “We are developing an example app to be able to show to potential manufacturers,” Hershoran states. “Once we have our first customer doing this, we would work with them to develop the standard and work with a [standards] organization to do so.”
What’s more, Hershoran says, the labels could be useful for consumers when it comes to laundry. Users could access care information about a product by tapping an Android smartphone against its label. If information (such as an item’s heat-tolerance level) needed to be updated, that could be accomplished in the software, thereby making it possible to revise information for consumers—even after they purchase a garment.