Air Canada Cargo is in the process of deploying an ultrahigh-frequency (UHF) RFID solution to manage shipments as they move through its five hubs, or when they enter or leave one of the larger cargo-transfer stations it operates around the world.
Air Canada is Canada’s biggest air cargo services provider, and most of its customers are large freight-forwarding companies and businesses that transport their products via expedited air service rather than aboard land vehicles. Approximately 10 years ago, Franwell approached Air Canada Cargo, looking to use the firm as a live laboratory for the testing of a radio frequency identification system to track the movements of cargo automatically. The cargo service provider has since spent several years testing and developing the technology, and is now deploying it across many of its stations.
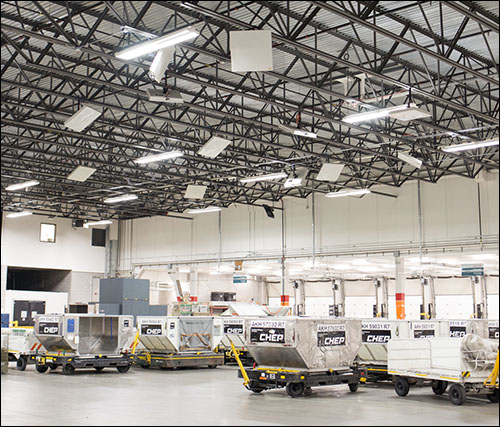
With the CargoAware system Franwell has developed, Air Canada Cargo expects to increase its shipment visibility, reduce the incidence of human errors, improve its use of resources and better support e-commerce initiatives related to tracking the receiving, packing and shipping of packages at its many stations around the world, says Barb Johnston, Air Canada Cargo’s manager of operational technology.
About a decade ago, Franwell, together with researchers from the University of Florida, approached Air Canada Cargo. “They were starting to dabble with the technology and approached us about it,” Johnston recalls. “We said, ‘Sure, you can play in our backyard,’ but it has evolved dramatically from there, and quite quickly.'”
The project started with a proof-of-concept, says Michael Morey, who was Air Canada Cargo’s director of cargo operations prior to retiring last year. Morey now serves as the advanced cargo solutions director at Franwell, where he works to supply solutions for the cargo industry, including Air Canada Cargo, with the CargoAware RFID technology. Fixed overhead and doorway portal RFID readers were installed at Air Canada Cargo’s facilities in Montreal, London-Heathrow and Frankfurt, and tagged parcels were then tracked as they flowed through those stations. Readers forwarded data to a central server running the CargoAware software, via a Wi-Fi connection.
The companies worked with the university to resolve such challenges as reading tags in the presence of liquid-filled packages (placing tags on the corners of parcels made them the most reliably readable), and what to do in the event that an Internet connection were not available for the readers to forward their data (if the Wi-Fi system being used for the RFID deployment was not working at any given time, the readers would store their data until Internet access returned).
After completing the proof-of-concept, Johnston says, Air Canada Cargo decided to “go forward with the technology.” The results proved that the system could provide automatic visibility into the packages’ status, she notes—including, in the case of the hubs, the specific container in which they were being loaded and transported.
Traditionally, when Air Canada Cargo receives a package from a freight forwarder, it attaches a label with information printed on it in text and bar-code form. That data includes an eight-digit air waybill number and the package’s destination. Workers can visually check the label at other stations, where packages are sorted for loading in vehicles and aircraft. At the hubs, the packages are placed in large containers known as universal loading devices (ULDs) or on pallets, and employees must input data about which packages are placed in which container, or on which pallet, so that they can be tracked.
With RFID, that process becomes automated. First, workers at the stations print a label with an embedded Smartrac Frog EPC UHF RFID tag. “If a shipper tenders shipments already wrapped together on a wooden pallet—many pieces wrapped together but identified to us as one piece—we tag it as one,” Johnston explains. “If the shipment is tendered as many loose pieces, we tag every single piece, then prepare it for transport.” The unique ID number encoded to the tag is linked to the air waybill number printed on the label, and to the shipment information in Franwell’s CargoAware software, which forwards that data to the Unisys management software that Air Canada Cargo uses to plan and track package movements.
When the package leaves an Air Canada Cargo hub or large cargo-transfer station to be loaded onto a vehicle or airplane, it passes a floor-mounted or overhead Jamison RFID Mod3 Smart portal installed at the dock door. The portal’s RFID reader captures the tag ID number and updates the software, residing on Air Canada’s server, to indicate that the shipment has left that station. When the package enters the next cargo-transfer station, it passes another Mod3 Smart portal and its status is again updated to indicate the new station.
At its five hubs—all located at key airports—Air Canada Cargo installed overhead Echo A202, A200, A300 and A302 smart antennas provided by View Technologies, with integrated RF Controls RFID readers that can identify the packages throughout the facility, as well as determine their location according to zones set up in the software. This is necessary because, in the hubs, parcels are typically loaded into ULDs, along with other packages destined for the same station, such as the one in Frankfurt. Shipments often consist of many smaller packages. By knowing in which containers they are loaded, the company can ensure that all packages end up in the same aircraft destined for the next station, even if they are loaded into different containers or onto different pallets. This also enables compliance with customs and security mandates.
When loading a ULD or pallet, Air Canada personnel utilize a handheld computer to input the ULD number and the zone into which it is being loaded. This enables the CargoAware system to use RFID to track what is loaded onto that ULD. Once the ULD has been filled, CargoAware forwards the collected data to the Unisys Logistics Management System (LMS) software and prints an RFID label that is then attached to the ULD and used to track its movement throughout the hub.
Workers are also utilizing handheld readers at some locations to search for specific packages, according to Michael Nicometo, CargoAware’s director, by placing the readers in Geiger counter mode. In addition, Air Canada Cargo has tested the technology with readers built into wristbands worn by packers. The readers, each of which contains a motion sensor, detect when a packer is loading a ULD, and begin reading the tag IDs of those packages. This system serves as an alternative to real-time location system (RTLS) solutions with overhead Echo antennas.
Most of the technology installation is taking place this year, Johnston says, at a rate of several stations per week. “By the end of next year,” she adds, “we expect to be entirely finished.”
Johnston says Air Canada Cargo looks forward to implementing a system of nine unique alerts that would notify local managers and agents at each station in the event that an error may be imminent. For instance, if a package is loaded into a container destined for the wrong part of the world, an e-mail or text message would be sent to the local manager. In the future, she adds, video screens might be installed at some stations to display alerts for workers onsite as well. In another scenario, containers transporting animals, such as dogs or cats, could be flagged as being especially sensitive to delays, so that if the software determines that an animal has been at a specific location—a dock door, for instance—beyond a maximum acceptable period of time (such as 30 minutes), an alert could be issued.
Because workers have traditionally used pen and paper to document the loading of packages into containers or onto pallets, and have input that data manually, the RFID system is likely to save them time as well. “It’s premature to say we have seen labor efficiencies, but that’s what we expect,” Johnston says. With the manual process, workers place a box in a container, write down the air waybill number printed on the box label, and then pick up the next one. The RFID-enabled version requires that an employee simply put the box into the container. “So we know we’re going to see process improvements,” Johnston states.
“With every manual process,” Morey notes, “you’re introducing the possibility of error.” In contrast, he says, the RFID technology automatically captures every movement, links it to the tagged object and stores that data on Air Canada Cargo’s server, so that users can view the relevant details as needed. This requires that the software perform a lot of filtering, he adds, since tag reads take place at a rate of three times per second. The solution is set up to update the Unisys system only when it detects that a package has moved to a different location, such as when it is placed into a container.
Air Canada Cargo has already been providing data for shippers and freight forwarders regarding the status of shipments, Johnston says, based on manually input or bar-code-scanned data. But with the deployment of the CargoAware system, she adds, the information will become much more accurate, since as soon as a tag is interrogated at a hub or other station, that read event can be sent to the Unisys system, which will then display that data for authorized parties to view.
If freight forwarders implement RFID as well, Johnston says, Air Canada Cargo hopes to be able to access those companies’ RFID-related data, such as when a package has left a facility and is headed for an Air Canada Cargo station. In fact, Nicometo says, Franwell is currently in discussions with some freight forwarders about deploying the technology as well.