In 2011, Shimane University Hospital, in Japan, deployed a high-frequency RFID solution to track surgical instruments used on patients through cleaning, sterilization and storage. The Rigshospitalet hospital, in Copenhagen, recently completed an 18-month trial in which it used ultrahigh-frequency RFID technology to track surgical instruments. While they took different approaches, both hospitals found that item-level monitoring improved patient safety and reduced costs and labor.
To help determine whether an RFID surgical-instrument tracking solution will deliver a return on investment for your hospital, consider the hard and soft benefits to be gained throughout the process: the preoperative stage, during the assembly of instrument trays at the central sterile department (CSD); intraoperative stage, for verifications before surgical interventions in the operating room; and postoperative stage, when hospital personnel collect all soiled instruments and send them back to the CSD for reprocessing (decontamination, assembly and sterilization).
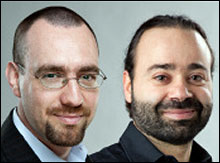
As we discussed in our recent column, Hard vs. Soft Benefits, hard benefits are those that will be converted into cash savings or additional revenues. Soft benefits will improve efficiencies, but they won’t necessarily impact your bottom line. Still, when it comes to managing surgical instruments, the soft benefits may drive your business case, because patient safety comes first.
Automatically tracking instruments can greatly reduce or eliminate infections, and it ensures no instruments are inadvertently left in the patient. Item-level tracking also facilitates traceability for compliance with sanitization and record-keeping requirements. Moreover, Shimane reports its solution reduces nurses’ mental stress and enables them to spend more time caring for patients.
But to be sure, the soft benefits are bolstered by recurrent hard benefits. Rigshospitalet, for example, which conducts approximately 75,000 surgeries annually, found automating manual processes could save the hospital 31,000 hours a year in operating-room procedures. Similarly, Shimane, which performs roughly 6,000 surgeries annually, found the entire process of managing instruments per operation was shortened from 150 minutes to 50 minutes, with expected annual savings in hundreds of thousands of dollars.
More efficient use of instruments also enabled the hospital to reduce its inventory by 20 percent, with anticipated savings related to further procurements. In addition, the RFID data can be used for quality control, maintenance and repair. The hard benefits your hospital could achieve will depend, in part, on how many surgeries are performed annually and how many tools you tag and track.
Using RFID to manage surgical instruments is a relatively new application that involves a number of challenges. When developing your business case, assess your workflow and all the areas in which you will need to establish read points. Also, consider the up-front cost of tagging tens of thousands of instruments (which requires specific competencies and equipment), as well as trays and carts.
If your business case indicates your hospital could achieve a ROI, put out a call for tenders. Then, as the Shimane and Rigshospitalet examples demonstrate, you’ll have to evaluate the HF
and UHF RFID options and decide which is best for your hospital.
Ygal Bendavid and Harold Boeck are professors in the school of management at the Université du Québec à Montréal, and members of RFID Academia‘s research board.