After four years of selling its radio frequency identification technology for tracking tools, assets and regulated products at nuclear facilities, as well as in the oil and gas and aerospace companies, French industrial safety management technology firm Nexess is developing a single solution that incorporates three separate RFID modules that it has previously offered. The new system, known as the NexCap Tool Tracking Solution, will incorporate a smart counter that reads tags and weighs tools as they are retrieved and returned, a smart cabinet that provides tools to users without requiring human intervention, and a PDA-based RFID solution to search for items in use or missing within a facility. The new solution will feature a single software platform to manage data culled from all three modules, says Olivier Rouault, Nexess’ product manager. In addition, the company plans to begin offering a retrofitting service for customers who wish to embed or attach RFID tags to their existing tools.
This year, Nexess began partnering with Desoutter Industrial Tools, which is now embedding tags in all new tools that it manufactures, and will aid Nexess in the retrofitting of existing tools with RFID tags for Nexess’ customers. Tag manufacturer Xerafy is providing its EPC Gen 2 on-metal passive ultrahigh-frequency (UHF) tags for use in the tools, while Nexess is working with several reader providers for its solution. German company Feig Electronic provides approximately 80 percent of the readers built into the NexCap smart cabinet and smart counter systems, while most of the RFID-enabled PDAs are supplied by Psion. What’s more, Nexess has begun offering Embisphère Bluetooth-enabled EmbiVentory readers to enable users to track goods and receive data on a tablet or laptop via the Bluetooth connection.
In 2008, Nexess was spun off from French power company Électricité de France (EDF). Initially, EDF was the firm’s primary customer, using Nexess’ RFID-based solutions at all 19 of its French nuclear power plants, for a total of 58 reactors. Each plant is employing at least one of Nexess’ NexCap modules, and some of the facilities are also utilizing Nexess’ RFID systems to track personnel as they enter or leave a reactor area during maintenance, via readers installed at entrances and exits to interrogate RFID tags built into the users’ ID badges.
Nexess also provides its tool-tracking technology to other operators of nuclear power plants, as well as to the oil and gas industry (for tracking the use and maintenance of equipment employed for drilling or other operations) and aerospace (primarily to track the distribution of tools loaned to personnel).
The NexCap smart cabinet, measuring about 3.5 feet in height, is intended for installation at sites where tools need to be accessed without requiring a staff member to provide them. The metal cabinet can store up to 150 tools, and contains a built-in UHF RFID reader, as well as antennas that capture the ID of any tagged tool placed inside the cabinet. When a user requires a tool, he places his RFID-enabled badge near the reader in the front of the cabinet. The cabinet has either an Ethernet or Wi-Fi connection to the back-end system, where NexCap software identifies the user via that badge ID, and prompts the door to unlock, as long as that access is authorized. Once the user takes the tools he needs and then closes the cabinet door, the system identifies and records which items have been removed. The NexCap software can also be integrated with the user’s enterprise resource planning (ERP) system, to provide other functions, such as storing a history of which tools are used, and by whom.
In some cases, when a large quantity of tools must be managed, a company may opt for a counter managed by a staff member. For such applications, Nexess offers a touchscreen, an RFID reader and a weight scale that can be installed on or built into a countertop. A worker seeking to borrow tools first presents his RFID badge to the reader. The person manning the counter then places each requested tool on the scale, where the reader captures that item’s ID number. If the weight matches the expected weight for that tool, the process is approved and the individual may take it. If the weight does not match the figure stored in the software, however, users are alerted that there is a problem. The same process occurs as the tools are later returned. The scale helps to ensure not only that the correct item is being identified, but also that it is being returned or checked out in its complete form (for example, if a battery were missing, the weight would be less).
Nexess’ smart counter system can also be used without a staff member overseeing the loaning of tools. In this case, weight sensors are built into existing shelves within the tool-storage area, which a worker can access by providing his ID badge to a reader at the door. Once inside, the employee removes items from the shelves, and, thanks to weight sensors, the system detects that items were taken and can thereby ensure that nothing is removed from the storage area without being properly checked out. The worker then uses the smart counter’s built-in RFID reader to check out each tool, by placing the item on the scale and indicating, via the touchscreen, when he plans to return it.
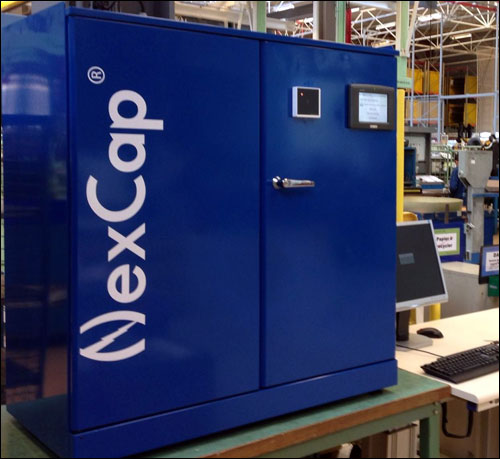
For the mobile solution, a worker uses a PDA with a built-in RFID reader to track down missing items, such as tools or spare parts. This is especially important in sensitive areas, such as near a nuclear reactor as it is being serviced, or inside an aircraft.
When adopting multiple NexCap modules, Rouault explains, users only require a single software platform, and can link data from each module—for example, those using the mobile solution can view when a tool was removed from a cabinet, as well as by whom. The system can also store maintenance data, such as when a tool was last calibrated. Use of the system can increase productivity, he says, by reducing the need to manually fill out paperwork or spend time searching for missing tools.
The NexCap Tool Tracking Solution is slated to be made available at the end of this year. The service for retrofitting tools, meanwhile, will be available in September, initially to customers in the aerospace industry.