Cambridge Consultants, a British technology company, is looking for customers such as parcel carriers after completing development of a Bluetooth-based RFID sensor tag that could help logistics companies and their customers identify when a package has been dropped. The system is designed to allow anyone with a smartphone equipped with a Bluetooth Low Energy (BLE) chip to use an app to read the status of a parcel, thereby determining how it has been handled. In that way, customers of a carrier could view, on their own phones, the status of a package as it is being delivered to their door, prior to signing for it. Carriers could also track that data themselves, knowing in real time when a parcel suffers an impact by reading data on a mobile phone installed in the truck.
One of Cambridge Consultants’ many spin-off companies is CSR (formerly known as Cambridge Silicon Radio), founded in 1998. CSR makes the kind of BLE 4.0 wireless radio chips that are being used in phones, as well as in the DropTag that Cambridge Consultants has now developed. BLE is characterized by a protocol design that allows for periodic rather than continuous data transfer, enabling the DropTag to operate for up to a year on a small battery, since the tag is usually dormant. In comparison to standard Bluetooth products, a BLE device (also known as a Bluetooth Smart device) transmits a small amount of data—typically about 200 kilobits per second—to an interrogator.
Tom Lawrie-Fussey, Cambridge Consultants’ business development manager, helped develop a BLE solution for tracking heart rates to be used by athletes, finding that sensor data about the wearer’s pulse could be transmitted to a mobile phone using one chip to store and send data, and a cell battery to power that sensor and transmission. Based on the success of that Bluetooth solution, Lawrie-Fussey and his colleagues “had a brainstorming session,” he says, leading to the idea for DropTag. He adds that instead of incorporating a BLE chip into its DropTag, the company had considered using a Near Field Communication (NFC) passive 13.56 MHz RFID inlay joined to a battery-powered sensor, but had rejected that option because the inlay’s short read range would have require that a reader be placed within centimeters of the package.
The DropTag consists of an accelerometer, a cell battery, a BLE chip and an antenna in a plastic housing, about the size of a silver dollar. The tag could come with an adhesive back to attach to the exterior of the cardboard box used to ship an item or to an asset or product packed inside the box. When the tag is interrogated by a Bluetooth-enabled phone, the tag transmits its own ID number along with any sensor data indicating a fall incident, as well as the time in which that incident occurred.
First, a package’s intended recipient would need to download the DropTag app onto an iPhone or BLE-enabled (Bluetooth Smart Ready) Android phone. Then when the parcel arrives, that person could simply open the app in the phone to interrogate the tag. The app would display a message indicating the parcel’s shipping history, such as “during transport your parcel was dropped.” The individual could then open the box to check for damage before signing for it.
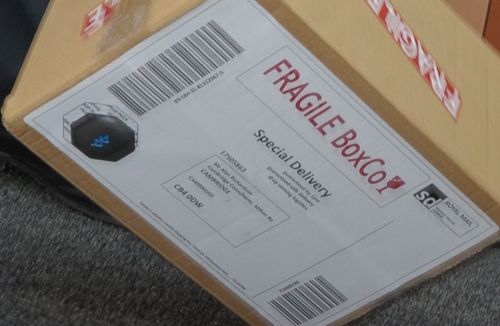
The data could also benefit the carrier, Lawrie-Fussey says, if the carrier opted to collect impact data while the parcels were being transported to delivery addresses. A smartphone could either be installed inside the truck’s cab or cargo area, periodically reading sensor data transmitted by the tags loaded inside. The read range for the DropTag is about 50 meters, and it can read through walls such as the side of a truck, Lawrie-Fussey says. If the status of a parcel changes—for example a driver turns a corner, passes over a pothole, or drops a box while unloading—the tag would send an update to the phone, which in turn would forward that data to the carrier’s back-end system to indicate that the package had fallen. The app could send GPS data to help management pinpoint where the incident occurred. Management could then alert the recipient of the package before it is even delivered, instructing that individual to check the parcel or informing him that the company has ordered a replacement.
Cambridge Consultants has built a prototype of the system including an app, and is now seeking potential customers such as a carrier, logistic company or retailer that would like to use the technology. Purchasers of the DropTag solution would be expected to brand the app themselves, which they could offer to their own customers, and to manage the data the way they chose. Cambridge Consultants is in conversation with some logistics companies around the world, Lawrie-Fussey says.
Lawrie-Fussey expects the tag to be priced between $2 and $3. In addition, he points out, there would be other costs associated with the adoption of the tag, such as the labor to apply. However, a tag could be used multiple times by simply removing it when a parcel was delivered, he adds, thereby reducing the cost per use.
The company is also considering marketing a version of the Bluetooth-based DropTag with a temperature sensor—instead of, or in addition to, an accelerometer—so that it could track refrigerated items such as fresh produce.