There has been a clear trend of industrial organizations ramping up efforts to capture data—usually designed to enable an extended view of equipment health, asset status and other system components. A while back, I talked about how there’s no point in compiling and analyzing data without having a plan for using it (see Operationalizing IoT Data to Drive Revenue in the Enterprise).
So has anything changed? Have organizations moved the needle when it comes to integrating the Internet of Things (IoT) with enterprise resource planning (ERP), enterprise asset management (EAM) or field service management (FSM) systems as part of their digital transformation journey?
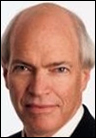
From my firsthand experience and research, I would say the answer is a tentative “yes.” There have been incremental steps toward embracing the full potential of the IoT, along with some isolated bright spots of rapid advancement. But there are also two areas of complexity that we need to address.
Issue 1: Lack of a Compelling Business Case
For some industries, rudimentary IoT is nothing new, and it has even reached a point of diminishing returns. For instance, manufacturing has long been involved in the IoT. Networked programmable logic controllers (PLCs) have been used to automate industrial processes, and data from supervisory control and data acquisition (SCADA) systems has enabled plant floor management visibility. All of this is based on data from connected devices, resulting in an increasingly autonomous manufacturing environment.
But even within manufacturing, we see very few companies realizing the IoT’s immediate revenue potential. This could be achieved by pushing the IoT further into the structure of the business. Data from connected devices could be used to transform and lean out the business, simply by triggering events and transactions ranging from inventory reorders to maintenance work orders to customer orders. This could give manufacturers the ability to leapfrog competitors by dramatically compressing timelines, improving the customer experience or creating new service and product lines that generate new revenue.
But here’s the rub: many companies still regard the IoT as just a mechanism to drive cost reduction. According to new research that IFS conducted in late 2018, most industrial companies planning to increase IoT investments are still looking primarily in areas associated with cost containment, instead of revenue generation. Sixty percent of respondents planned to increase spending on process automation, while 50 percent planned to spend more on condition-based maintenance. Yet less than 30 percent planned to increase IoT spending for field service and aftermarket service, which drives net revenue at margins higher than realized on the initial product sale.
What it comes down to is this: each market sector and each company will need to identify the best business case for its own needs and its own opportunities—the place where an enterprise IoT approach can and will drive measurable return. It is here that we see the most rapid adoption. For example, in the construction industry, organizations are seeing the greatest, most immediate ROI potential in terms of increased safety. While this is a specific and viable business case for construction, it could also be characterized as a cost-avoidance mechanism. But, small steps.
Issue 2: Gaps in Commercially Available Technology
Large enterprises are able to fund massive systems-integration projects across IoT, SCADA and enterprise software in an attempt to derive enterprise-wide benefits from the Internet of Things. But commercial off-the-shelf solutions that can easily be configured to connect data from connected devices to the enterprise have been, in many cases, slow to come to market.
A 2018 study from the management consulting firm Bain & Co. reveals that would-be IoT adopters believe that vendors have made little progress on lowering the most significant barriers to IoT adoption. The study cites security, ease of integration with existing technology systems, and uncertain ROI as areas of concern. The consultants indicate that, on average, businesses are planning less extensive IoT implementations through 2020 than they were just a couple of years ago.
This is particularly an issue in industrial sectors. With such a wide range of PLC and SCADA systems, it’s challenging to combine and consolidate them in a logical way with ERP systems. Because of this, I’ve seen IoT initiatives quickly turn into a tangled mess, with system integrators attempting to map multiple systems together. Enterprise software will increasingly need to offer streamlined approaches to this arduous task to ease adoption.
For now, a substantial gap remains between connected devices and the transactional software used to run a business, like ERP. In our research, the percentage of respondents who have integrated IoT data streams with ERP software stayed about flat between 2017 and 2018. And to a certain extent, ERP software as a system of record may continue to be a constraint for companies intent on adopting transformational business models built around IoT data. The IFS findings echo Bain & Co.’s findings that vendors have been slow to offer manageable routes to adoption, specifically when it comes to integration with operational technology like ERP software.
Increasing Sophistication in IoT Data Collection
Even with what appears to be incremental growth, the sophistication level of IoT application has been jumping by double digits year-over-year. Data from our study reveals several interesting upward trendlines during a 12-month period between 2017 and 2018. It shows:
• Companies collecting IoT data on entire work cells or production lines rather than individual machine components or individual machines increased by 17 percent.
• This, in turn, enables more advanced use cases, which helps explain a 30 percent increase in the use of IoT technology to support asset performance management.
• Respondents using the IoT to monitor their customers’ equipment saw a 10 percent increase, potentially signaling transformational approaches to field service management.
I predict we may see two waves of IoT investment, the first focused on enabling more thorough and strategic data collection, with a second wave (or series of subsequent waves) focused on making more complete use of the data collected. For example, in the early stages, data collected about customer equipment may help manufacturers troubleshoot, but at later stages, it could drive an automated field service value chain in which the equipment sends its own work orders.
In time, I also believe these sensors will support servitized business models, as manufacturers may charge a customer for productivity and outcomes—duty cycles, products manufactured, hours of operation—rather than for a discrete product. There’s no stopping the move toward greater interplay of the IoT and business systems. There are some obstacles in the road, however, including a hazy vision of how to build a viable use case based on different company needs.
There is a role for software and technology vendors to play along this journey as well. Enterprise software vendors must deliver simple and predictable pathways for IoT data to travel through the core transactional systems that underpin companies and automate processes or provide actionable analysis. Once these two barriers are overcome, we’ll see a much greater surge in IoT adoption as part of a revenue-generating business strategy.
As CTO of IFS in North America, Rick Veague has responsibility for the company’s product and industry solutions offered to customers and partners throughout the United States and Canada. Rick joined IFS in 1999, and has held positions developing, marketing and delivering high-value business applications, including ERP, FSM, EAM and MRO solutions.