I am often asked why, if radio frequency identification technology is as wonderful as I say, everyone isn’t using it. There are a variety of factors involved, including the natural resistance to change and competition for resources. But there is also the fact that many companies just don’t know—or care—a great deal about how inefficiently they manage their physical assets.
Brian Kelly, Johnson Controls‘ director of supply chain management, said, during his keynote address at RFID Journal LIVE! 2016, that his company didn’t know how many containers it had for shipping products to suppliers. “It is somewhere between—and this is our best guess—four and five million,” he told attendees. (You can view his keynote address here: part 1 | part 2.)
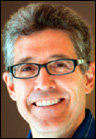
Kelly said he’s been working for Johnson Controls for 26 years, and that some containers were purchased before he joined the company. “What’s been lost, what’s been stolen, what’s been damaged, what’s been shipped and never come back is really unknown over that period of time,” he told the audience.
Many CEOs can tell you the precise profit margin for every single product their company produces, whether it went up or down in the last quarter, and what contributed to the change. But those same CEOs don’t know how many containers—and other physical assets—their companies own.
Johnson Controls is by no means unusual. When I launched RFID Journal in 2002, a senior supply chain executive at a large American consumer products company told me: “At any moment in time, we don’t know where about $1 billion worth of inventory is. It’s not lost or stolen. We just can’t locate it at the moment. If we could use RFID to eliminate that misplaced inventory, we could free up a $1 billion in cash to use for something else, such as an acquisition.”
A few years later, I was interviewing the director of materials management at a major hospital in Boston. He told me that when his hospital decided to deploy an active RFID-based real-time location system, it brought all of its gurneys into one area so they could be tagged. “I thought we had 200 gurneys,” he said. “When we got them all together, it turned out we had 300 gurneys.” That’s an inventory accuracy rate of only 66 percent.
Around the same time, I spoke to a systems integrator who worked on a project for a paper company. The project’s goal was to tag rolls of newsprint so they could be tracked, since the rolls look similar but contain different qualities. The integrator suggested tracking forklifts as well, so the company could optimize the route that each truck driver took from the time he picked up a roll until he delivered it to a shipping bay.
“The warehouse manager told me that wasn’t necessary,” the systems integrator recalled. “He indicated they had already optimized routes and trained forklift truck drivers to follow them. The guy insisted that the efficiency of the drivers could not be improved upon.” But when the integrator looked at the data from the pilot, the forklift trucks were driving around 60 percent of the time without carrying a roll of paper.
More recently, Bill Hardgrave, dean and Wells Fargo Professor at Auburn University’s Harbert College of Business, gave a presentation at RFID Journal LIVE! Europe in which he described a conversation with the VP of store operations for a retailer that wanted to allow customers to buy items online and pick them up in the store. The first question Hardgrave asked was, “What is your in-store inventory accuracy?” The VP claimed it was in the 90 percent range, so Hardgrave asked how he knew that, to which the VP replied, “Our system says we have a thousand pair of shoes in the store, and when we count we get about 900, so we’re at around 90 percent.”
Hardgrave explained that aggregate numbers are meaningless, and that a company must look at the inventory accuracy for each individual stock-keeping unit (SKU)—to know, for instance, that it has four of a particular item in-store—if it plans to expose that inventory to a customer who wants to buy a product online and go to the store to pick it up. “When they drilled down,” Hardgrave said, “their inventory accuracy wasn’t very good at all. It was around 50 percent at the size, color, style level.”
The point here is that most businesses don’t know how inefficient they are when it comes to managing physical assets—things that move around, have no internal power source and are not connected to the Internet. Some, in fact, are not jumping to employ RFID because they don’t believe they need the technology or don’t understand how much they can benefit from it. If you don’t know what you don’t know, then it’s difficult to know you have a problem that needs to be fixed.
Mark Roberti is the founder and editor of RFID Journal. If you would like to comment on this article, click on the link below. To read more of Mark’s opinions, visit the RFID Journal Blog, the Editor’s Note archive or RFID Connect.