- Omnidirectional Reading with a Single Tag Chip
- Tag Production Capacity Aimed at 12 Billion
- Custom Tags that Defy the Metal Detector Challenge
With the goal of serving the rising demand for radio frequency identification technology, Polish company Talkin’ Things is acquiring more production space and assets, including new antenna milling equipment, and it plans to produce as many as 1.3 billion RFID tags annually, beginning in 2023. At the same time, the company has released a new omnidirectional tag that it says can accomplish 10 meters (33 feet) of transmission range at any orientation or angle.
With its recent capacity increases and existing development efforts, Talkin’ Things predicts it will have a growing presence in the RFID tag industry, but that it will also provide more sustainable versions of its products, without requiring chemical-based etching of aluminum antennas. The company intends for its new Rezszów plant to be a zero-emissions site, and it recently received $20 million in investor funding that will be employed on production facility expansion, according to Jakub Zaluska, Talkin’ Things’ marketing director.
Since launching in 2014, Talkin’ Things has offered a customizable solution approach, providing large numbers of RFID tags and developing them for customers’ specific needs. One example of such efforts involves an airbag manufacturer that required RFID tags that could pass through a metal detector without being detected. This is the kind of challenge in which the company specializes, Talkin’ Things claims, as it can build a new tag prototype using its own machines to approximate the bonding and materials necessary for tags for a specific application.
Talkin’ Things has traditionally taken an innovative approach to RFID tag production, by providing low-cost products that are high in quality (see RFID Tag Costs Drop to About 3 Cents with Talkin’ Things Products). That quality is crucial, Zaluska says, for “without quality and performance, the low price would be of no use.” The company is selling the tags to both brands and packaging businesses, and it partners with packaging companies as well.
Talkin’ Things works with MCC Label and other businesses to ensure that tag application can be incorporated into existing production processes. In addition, it can provide entire RFID systems, including readers and software to run industrial hardware, which would be integrated with a user’s existing management software. Year by year, the company has been growing its capacity. It now produces half a billion tags annually, with plans to double that capacity by the end of 2022.
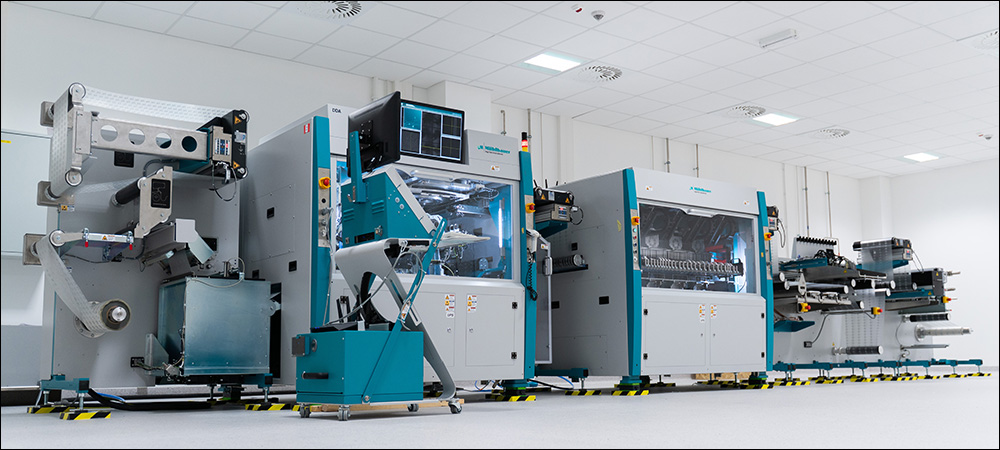
Talkin’ Things builds tag prototype using its own machines to approximate the bonding and materials necessary for tags for a specific application.
Omnidirectional Reading with a Single Tag Chip
One way in which Talkin’ Things is growing is with the development of new products. In May, the company released a new line of omnidirectional RAIN RFID tags known as Storks, which feature omnidirectional functionality without requiring specialized chips that typically cost more than standard chips and tags. This, Zaluska says, allows users to gain the kind of read reliability from any angle that might have required complex multi-antenna configurations in the past, or tags based on dual-differential antenna ports.
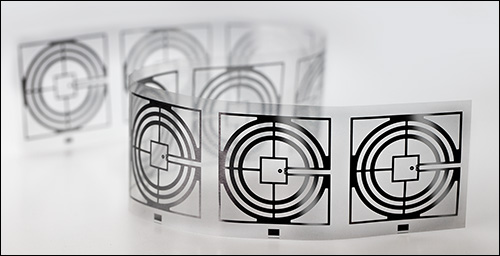
Stork tags
The three new Stork products each include an NXP Semiconductors UCODE 9 chip and are built to provide reliable read performance from any angle. The 50-millimeter (2-inch) TT-501D Stork provides a reading distance of up to 15 meters (49 feet) when directly oriented in front or back, and up to 10 meters (33 feet) if oriented sideways—that is, at 90-degree and 270-degree orientations. The smallest tag, the TT-301D, measures 30 millimeters (1.2 inches) and offers a read distance of 10 meters (33 feet) in front and back, and 8 meters (26 feet) at any other angle. The third product is sized at 40 millimeters (1.6 inches), with performance between those of the other two tag models.
Customers had approached Talkin’ Things regarding assembly lines and other environments crowded with moving products or assets. “They were having problems getting [UHF RFID] reads because, in some cases, the tags were oriented the wrong way,” Zaluska recalls. There are countermeasures to this problem, he notes—having multiple antenna setups around a read zone, for example—but that adds complexity and cost to the solution. The Stork tags are designed to address the problem, Zaluska says. The tags leverage a circular pattern antenna as an alternative to existing omnidirectional tags that require two crossed antennas, which can be more costly than standard tags.
Tag Production Capacity Aimed at 12 Billion
Talkin’ Things is now in the process of growing its production facility. Its RFID Gigafactory is the result of expanded space in the company’s existing building, and it plans to open another facility to meet further growth. “Our goal is 12 billion,” Zaluska says. “We plan to build the factory for the target capacity.” The firm anticipates considerably more growth in the RFID industry.
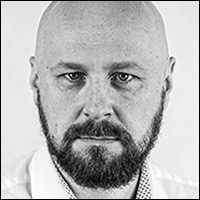
Jakub Zaluska
“The RFID market is skyrocketing,” Zaluska adds, related not only to technology advancement but also business demand as more brands follow the lead of retailers deploying RFID. “We are seeing the highest growth mostly in UHF RFID.” NFC technology use, he says, is also growing as businesses build shorter-range, smartphone-enabled technologies into packaging, as well as into payment and ticketing products.
Talkin’ Things continues to benefit from a fast design process at its production site, Zaluska reports, and the company can design and prototype tags according to a customer’s needs. “Due to a couple of clever innovations on the laboratory side,” he states, “we now are able, within a matter of just hours, to prepare the samples directly from the design phase in the computer.”
The company builds a simulated tag in its software, then produces a tag meeting those specifications and tests iterations of the design in a way that replicates the same RFID tag-bonding process used during production. “So we eliminate the variation in the process that may come from a manual process,” Zaluska says. The company then designs and builds tags with specific attributes for clients and, in some cases, builds out the portfolio of tags it offers based on these designs.
Custom Tags that Defy the Metal Detector Challenge
Custom tag design helps to address companies’ specific problems, Talkin’ Things explains. For instance, a manufacturer of airbags (which has asked to remain unnamed) has been working with the technology provider to introduce RFID tags into its automotive safety products. By building an RFID tag into each product, the company can uniquely identify every item during assembly and shipping, ensuring automatically that products are built properly and meet inspection requirements. The airbags could then be traceable even in the case of a return.
Quality control is an essential part of the company’s production process, Zaluska says, and could be time-consuming when done manually. Introducing RFID technology to the process, however, carries unique challenges. After a product is assembled, it must pass through a metal detector to ensure no pieces of metal were introduced into that product due to an error in production, such as a tiny piece of metallic equipment breaking or falling into the airbag. The detector would recognize the tag’s aluminum antennas, disrupting that process.
“We had to have a tag that is so small it goes below the threshold of the metal detector,” Zaluska says. The company was able to prototype and test such a tag within a matter of days, and it found that the tag still works at a distance of up to 2 meters (6.6 feet) in free space, but that it does not trigger the metal detector during production. “We really take advantage of our rapid prototyping,” he states, “so we gain clients that couldn’t find the solution for their problems anywhere else.” From the time of specification, the tag can be developed and produced within about 10 days. During that time, he notes, “We can go through a couple of iterations of prototype and testing.”
Talkin’ Things accomplishes this with a machine built to replicate the bonding process of a standard RFID tag, matching the tag’s exact pressure, temperature and time of curing. “We can program it,” Zaluska says, “and we get the results just for a single tag.” The company’s own engineers can place the chips manually, one at a time, on the antennas in the right spot, leveraging a microscope. For tag production, the facility currently employs two bonding lines, a pair of converting lines, testing lines and several encoders. An additional bonding line has enabled a capacity of half a billion tags. Next, the company says it plans to expand its floor space.
A new antenna production machine is expected to provide a more sustainable option for tag manufacturing, Zaluska says, by milling rather than chemically etching antennas. Milling provides a production process without chemical waste, similarly to how laser cutting operates, but at a lower cost and a higher speed than laser cutting. The excess aluminum is scratched away mechanically, without chemicals, and the waste aluminum can be recycled. “The only waste product is 100 percent pure aluminum,” he states.
The process has some limitations, however. For instance, users cannot employ the same antenna design created for an etching process; rather, the design must be modified for the machine. Thus, the company has been coming up with ways to make antennas compatible with the new machine, based on existing designs. Talkin’ Things expects the milling process to be a more popular alternative to standard tech production going forward.
“We will try to, wherever possible, switch to the green alternatives,” Zaluska says. It’s better for the environment since it eliminates the chemical process, the company explains, and it reduces extra transportation of goods when antennas are built at a third-party site. The milling process may also ensure the flexibility Talkin’ Things requires for specialized tags, enabling it to produce tags on demand.
Key Takeaways:
- Talkin’ Things is expanding to a capacity in the billions, with a focus on custom products and solutions.
- By acquiring an antenna milling machine, the company will be able to build custom tags onsite in a more environmentally sustainable way.