KH Lloreda, Spain’s largest household cleaning products company, has developed its own automated shipping system—transporting product from its manufacturing site, through its distribution warehouse and on to customers. This, the company reports, has virtually eliminated the need for manual labor.
The system has been in operation since December 2010. According to the company, the RFID technology tracks cartons of products as they are automatically assembled onto pallets, placed onto trucks, unloaded and stored at a distribution center, reassembled onto pallets in response to a retailer’s order, and again loaded onto trucks for delivery to that retailer. With RFID, says Daniel Lancho Navarro, KH Lloreda’s operations director, the firm knows at which stage its products are in the shipping process, as well as when their status changes, and can also prevent errors in the system, with human hands rarely ever touching the cartons. If, for example, the robotically picked cartons are incorrectly loaded (if they don’t match an order), the RFID technology detects that error, issues an alert to management, and stops the automated task in question (such as loading a truck, or stretch-wrapping a pallet) so the discrepancy can be addressed.
The installation of the RFID hardware and software, as well as the integration of that software into KH Lloreda’s enterprise resource planning (ERP) system, was provided by Spanish RFID systems integrator Saident RFID Soluciones. The software interprets data from the RFID reads and determines where the cartons are in the shipping process, then forwards that information to the company’s back-end system, where other software programs on HK Lloreda’s server select cartons to match customer orders and instruct the robotic stacking of those cartons onto pallets. The loading system was provided by Moveco, and Italian provider of dock-automation systems.
The family-owned KH Lloreda, based in Barcelona, sells 25 million bottles of its kitchen and bathroom cleaners and stain-removers in Spain, France, and Portugal annually, representing 60 percent of the market share in those three countries. It also sells a smaller quantity to consumers in Greece, Croatia and Poland. Most of the products that the company ships to retailers come in the form of 750-milliliter (25.4-ounce) plastic bottles, with 12 bottles packed in a box.
The company began looking into an RFID-based system approximately two years ago, Lancho says. With the construction of such an automated system, KH Lloreda envisioned being able to ship those boxes of product from its manufacturing site to its distribution center, and then loading the orders onto trucks bound for retailers. The work would be accomplished with almost no human intervention, he explains. Instead, the company designed robots to stack boxes onto pallets at the manufacturing site, bring those pallets to a staging area and then load them onto trucks, for delivery to its DC. There, the system would automatically remove the pallets from the vehicles and store them. Later, when product was needed to fulfill a retailer’s order, a robot would remove the necessary cartons from the pallets and stack them on separate pallets, which would then be stretch-wrapped and loaded onto trucks destined for stores.
To track the loading of those goods and ensure that mistakes do not occur, the company chose an RFID system that can capture the ID number of a UPM Raflatac DogBone EPC Gen 2 passive RFID tag attached to each box loaded with cleaning products. Its factory has several carton-filling lines, one of which is automated—the other three are partially manual. On the automated line, a Germark RFID printer-encoder encodes each tag, which is automatically applied to the carton’s exterior. In the semi-automated lines, factory workers place the encoded tags onto the cartons themselves.
A robot stacks the boxes onto a pallet, which then moves along an automated track to a fixed Impinj reader, where the pallet is rotated four times to ensure that the interrogator captures each RFID tag’s unique ID number, thereby verifying which cartons are loaded onto the pallet. The reader then forwards that information to KH Lloreda’s back-end system. If a box’s tag can not be read, the system issues an alert to the staff so that the unreadable tag can be replaced by one that functions properly.
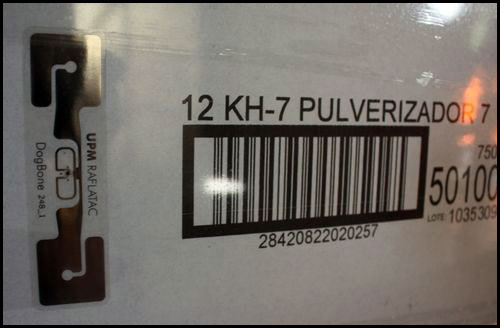
Once the reader data is received in KH Lloreda’s software, the system changes the status of the cartons on that pallet to indicate each carton is being loaded for transport to the distribution center. Trucks then back into the four loading docks, each of which is equipped with a fixed Impinj RFID reader portal. The pallets are automatically loaded onto the vehicles. In some cases, this is achieved via a combination of moving tracks on the loading dock and directly inside the truck. In other cases, a telescoping robotic arm fitted with a double-width forklift loads pallets, two at a time, into the vehicle. As each pallet passes through the portal, the reader captures the tag IDs of the cartons on that pallet.
Once the system determines that all pallets are loaded onto the truck, KH Lloreda software signals an alert to the distribution center, indicating that a loaded truck will be arriving. In this way, the software can also begin preparing picking plans for customer orders, which are sent to the picking robot at the DC.
When the truck arrives at the distribution center—located less than a kilometer from the manufacturing facility—another RFID portal at the incoming loading dock awaits. The portal’s Impinj reader captures each carton’s ID number as the pallets are automatically unloaded via moving tracks and pass through the portal. Those IDs are again forwarded to the back-end system, in order to confirm that the items have been received at the distribution center.
The picking robot, manufactured by industrial robotics company Fanuc, moves along a track, using 3-D artificial vision with an infrared camera and laser to analyze every carton’s position and location on each pallet. The robot receives instructions from the software as to the cartons required for a particular customer order, and begins removing cartons from the pallets in storage and loading them onto new pallets destined for that customer. The robot is also instructed to pick the heaviest and biggest cartons first, in order to ensure that they are stacked in the lowest part of the pallet, with the lighter and smaller ones stacked on top. To help it perform these tasks, the robot utilizes its 3-D artificial vision, as well as instructions from the database that contains a record of the storage location of every pallet loaded with cartons.
The pallets travel down automated tracks to a stretch-wrapping station, where an Impinj interrogator at the machine reads each carton’s ID number, and the software then compares the IDs with the order. If the IDs do not match specific orders, a screen illuminates an alert, and the stretch-wrapping process stops until it can be corrected via a supervisor’s manual intervention.
As a truck arrives to take orders to customers, the software determines which pallets to load first, to ensure the optimal unloading sequence, based on the order in which the pallets are to be delivered to customers on the driver’s route. The software then instructs the robotic system accordingly.
At the loading dock, an RFID portal reads the carton tags once more as a robot places the pallet onto a truck, and a screen at that location also displays an alert if the pallets are being loaded in the incorrect order, or if the wrong cartons are being loaded onto the vehicle.
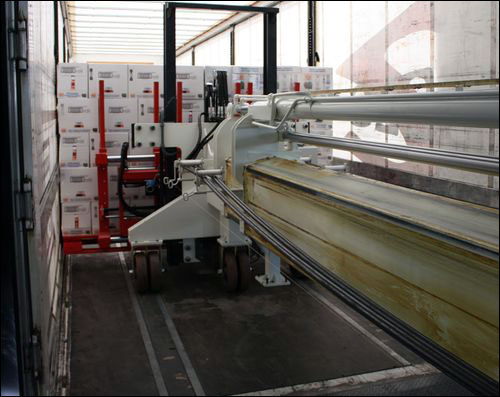
According to Lancho, the system went live following two years of development. The company spent €9 million ($12.3 million) on the automated system, but it expects to gain sufficient benefit from the automation (reduced labor costs, for instance) to achieve a return on its investment.
“We are driving our investment not just for the pleasure of innovation,” Lancho states. KH Lloreda has patented the loading system, he says, and offers workshops to share the results of its automation and RFID project with other companies, and also plans to provide the solution to technology resellers, earning royalties in the process.