Even if the name doesn’t sound familiar, there’s a good chance you’ve visited, traveled on or otherwise benefited from at least one of Bechtel‘s many global megaprojects. Headquartered in San Francisco, the engineering, construction and project management firm has built, or played a major part in building, such modern marvels as the Bay Area Rapid Transit (BART) system, the Channel Tunnel, Hoover Dam, Las Vegas’ McCarran International Airport and the Trans-Alaska Pipeline.
Bechtel is now involved in the construction of three liquefied natural gas processing and export facilities on Curtis Island, an ecologically fragile mile-long speck of land off the coast of Gladstone, Australia. The facilities are being constructed to process coal seam gas (CSG) produced by collection facilities on the Australian mainland. The plants will purify the gas into a liquid state for export to customers worldwide.
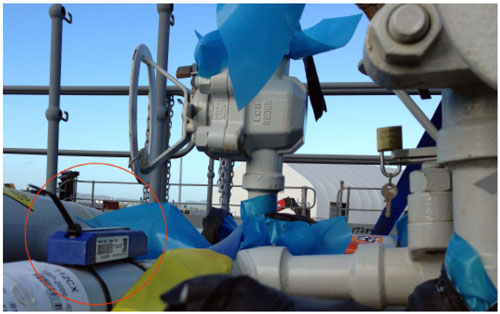
Even by megaproject standards, it’s an epic undertaking. Each of the three sites will employ several thousand workers during construction. Yet there are no roads connecting the facilities to the mainland or each other, which makes moving people, vehicles and construction materials a formidable challenge. “It’s basically an uninhabited island in the area we’re working,” says Ed Koch, the company’s construction automation specialist.
With limited room on the island, the majority of the project’s materials receiving and laydown (storage) sites are on the Australian mainland. The construction materials must be loaded onto ferries and transported across a harbor before reaching their installation location. “All the materials have to be handled multiple times before arriving at their final destination,” Koch says.
The materials that sail across the harbor must arrive at the correct island project destination on time and in the correct quantity. Mistakes are likely to generate a ripple effect, delaying construction in multiple areas simultaneously. “When you have materials mixed for three different sites, all in multiple storage areas, you really have to make sure the right thing gets selected and transported to the right place by the right time,” Koch notes.
Bechtel needed an efficient, cost-effective way to track and organize the materials involved in the construction of the three facilities. The company selected RFID to serve as the nucleus of a new cutting-edge localized materials-management system. “For Bechtel, RFID provides a world of opportunity,” Koch says.
First Steps
Since Bechtel couldn’t do much to improve the projects’ transportation situation, due to the island’s remote location and protected wildlife habitats, managers knew they needed to take steps to ensure the efficient coordination and management of construction materials.
The search for a solution began in fall 2011, when they formed an evaluation committee in the United States to study how other major construction projects dealt with similar logistics challenges. Managers also closely scrutinized a pilot study Bechtel conducted in 2008 with the Construction Industry Institute that quantified the benefits of RFID tracking and management. “We knew we could find things approximately eight times faster, and we had seen, during the study, productivity improvements in excess of 4 percent,” Koch says.
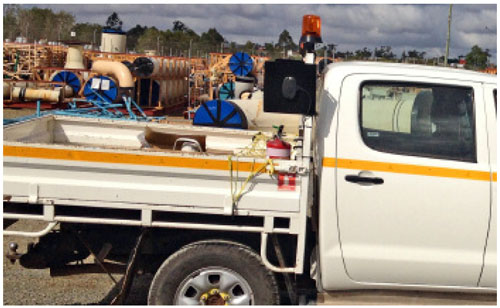
A crossfunctional team was formed in November 2011 to develop a formal design and deployment strategy. The team included representatives from Bechtel’s business corporate divisions, and project technical experts from procurement and construction. “Involving all key stakeholders was vital to success,” Koch says. The team identified three key goals:
• Integrate RFID into existing company-developed supply-chain software to achieve transactional benefits during materials handling.
• Track the location of materials as they move through a complex localized supply chain from mainland distribution centers to Curtis Island job sites.
• Shorten cycle time and reduce costs for collection of materials and transfer of those materials to the individual project sites by using fewer personnel and equipment resources.
To develop a system that would meet all these goals within the limited time available, Bechtel turned to Atlas RFID Solutions, based in Birmingham, Ala. The company, Koch says, was selected for its focus on construction-industry solutions and its successful work with Bechtel on a previous project. Atlas was awarded the RFID project contract in late 2011.
Designing the System
Atlas completed the system’s basic design in early 2012. A limited trial—Koch calls it “proof of reality”—was launched in the second quarter. But the deployment failed to meet Bechtel’s expectations. “With that first deployment, we very quickly realized that everything that had been cobbled together stateside was not 100 percent reality when it actually went to the field,” Koch says. “You’ve got to plan how you’re going to deploy and then, once you get to where you’re really going, you have to adapt.”
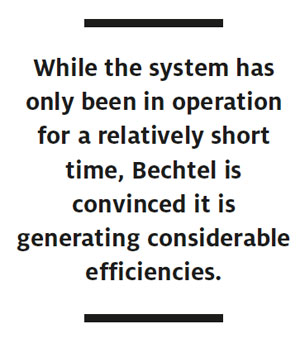
Bechtel and Atlas needed to move fast to keep pace with an unyielding construction timeline. It took roughly six months to “recalibrate,” Koch says, which included redesigning processes and conducting further tests.
Bechtel installed 13 gate readers from Identec Solutions at the entrances and exits of the project facilities: five at mainland-based materials storage yards, one at a pipe spool fabricator, four at mainland port sites, and one at each of the three Curtis Island port facilities.
The company distributed 37 Mobile Demand T7200 Tablets—equipped with Identec RFID readers, integrated bar-code scanners and built-in GPS technology—to materials workers at all mainland and island project sites. The tablets are used in conjunction with four vehicle-mounted readers (VMRs), with one supporting the storage yards and one at each project site. All materials are identified with Identec i-B2 active tags—roughly 60,000 so far. Some tags are recycled, so Bechtel estimates it has tracked well over 100,000 items.
Atlas’ proprietary Jovix software is used across the entire deployment to support the project’s complex multisite materials-control processes. The software is integrated with Bechtel’s procurement system to exchange information such as materials receipt, movement, requests, picking and issuing. Since it was designed from the outset to handle complex construction-site tasks, Jovix required only a few minor modifications to mesh successfully with Bechtel’s internal business software.
Supply-Chain Logistics
When the company completed final deployment in mid-2012, Bechtel found itself with a system that met or exceeded all its project goals. Although the Curtis Island facilities require a wide array of construction products, the materials logistics and management processes are virtually identical for all the materials, with only slight variations.
Materials are sent to Australia from suppliers worldwide. Upon arrival at the laydown yards, the materials are tagged. Then, Bechtel employees use their tablets to complete a formal receipt work process and upload detailed materials data from the tablets into Jovix, via Wi-Fi from the storage site or later if Wi-Fi is not available onsite. “This is our first knowledge that materials have been received,” Koch says. Once the information is received in Jovix, it becomes accessible via Bechtel’s internal procurement system as well.
As workers move materials around during laydown yard organization, the new locations are recorded with either the VMRs or the gate readers, which then feed the information into Jovix. When a materials withdrawal request (MWR) arrives from a project site, notification is transferred into Jovix via the software’s integration with the procurement system. Pick lists can be created and assigned to users, who then handle the picking using their tablets, which significantly decreases the time spent searching for materials.
Since all materials require transport to the Curtis Island project locations through a complex sequence of events involving trucks and cross-harbor ferries, documentation is required for any item loaded onto a transfer unit (trailer, flat rack, pallet or any type of ground transport platform). Field workers use their tablets to combine different materials onto an RFID-tagged transfer unit, and the software associates the items with the transfer unit. Desktop computer users can then generate packing lists for each transfer unit.
As transfer units move through the various gate readers, materials location and status information is updated automatically in Jovix to create full traceability. This process previously would have required vast amounts of manual data collection, system input and management via conventional clipboard and paper methods, Koch says.
Once the materials arrive on Curtis Island, a procurement team uses tablets to complete an issuing process similar to that used by a parcel courier. This passes the information back to the procurement system, which officially issues the materials to construction, depletes the quantity and closes the MWR, simultaneously recording what materials were issued, when and to whom.
The RFID tags remain attached to the materials until installation, ensuring locating and traceability, Koch says. All data for the movement and transactions of the materials are recorded and saved in a historical location that can be used for reporting.
For a project this size, Bechtel faced just a few small challenges. The firm needed a reliable local communications infrastructure. Existing connectivity between Australia and the United States, where the Atlas servers are located, was poor during the trial phase. To rectify the problem, Bechtel and Atlas engineers collaborated and concluded that moving the servers to an Australian data center would greatly improve data synchronization between the servers and end-user tablets. “This solution improved synchronization efficiency from approximately one hour to only minutes,” Koch says.
The only read-rate problems encountered were caused by improper tag placements on the materials transfer units, Koch says. “Atlas helped us determine proper RFID tag placement on the transfer units, and the read-rate issues dissipated and performance issues were immediately improved,” he says.
Koch also credits continuing emphasis on end-user training for the system’s successful deployment. Training, conducted with the help of an Atlas representative, initially focused on getting workers up to speed on individual work processes. “There are now also ongoing refresher courses and on-site support,” Koch says.
Quantifying Benefits
While the system has only been in operation for a relatively short time, Bechtel is convinced it is generating considerable efficiencies. Koch points to a Six Sigma process study that, for pipe spools alone, showed a time savings of one man-hour per MWR, with 300 MWRs generated weekly over multiple project years. “Total man-hour savings for the MWR work process is expected to be significant,” Koch says.
The system offers other benefits, too, such as the ability to track transfer units via gate- and vehicle-mounted readers and GPS. Previously, personnel had to manually track transfer unit locations and materials, Koch notes. “Now,” he says, “the system provides a real-time snapshot of precise transfer-unit locations and loads on project sites.”
Several other Six Sigma studies are under way, with initial estimates showing a significant positive impact on indirect labor. “We believe digitizing these processes could potentially reduce our indirect labor costs by an estimated 5 percent on multiple billions of total project costs,” Koch says. “The construction is ongoing, so final investment returns are still unknown, but we anticipate a large return on investment.”
With the last Curtis Island facility not scheduled for completion for many months, Bechtel plans to keep making refinements to its RFID installation with an eye toward equipping upcoming capital projects with similar systems.
Bechtel is working hard to increase partner involvement. Koch notes that some fabricators are now tagging items before shipping. “They’re also beginning to generate advance data that will help us improve the management of downstream work processes,” he says.
“RFID keeps revealing new and innovative uses,” Koch says, “and we’re really pleased with that.”