- Identifying Robot Parts via RFID
- Automatically Linking Panels to Molds and Inserts
- Eliminating Manual Counting
PolySto Group, a technology company for the Belgian food industry, has adopted an RFID system in the past year that is enabling a robotic assembly process for its specialized hygienic wall protection solution. By tracking each new panel and the related molds and parts fitted to that product, the company has transitioned from a fully manual assembly process to a robotic one. That has resulted in faster production, with fewer potentials for errors, the company reports. The solution, provided by Aucxis RFID Solutions, employs UHF RFID readers from Impinj, as well as Aucxis’s own Hertz middleware and Polaris software.
Due to the nature of its operations, and the highly regulated requirements of health and government bodies, the food industry needs specialized wall coverings wherever food is managed, PolySto explains. The company, based in Lokeren, Belgium, manufactures polymer composite wall panels, known as kerbs, that are composed of a mixture of polyester resins and quartz granules, as well as various additives. The composition helps to prevent contaminations, such as Salmonella, E. coli and Listeria. These protective panels are designed to be easy to clean and decontaminate.
PolySto can customize the products according to the needs of its customers. Each panel includes specific molds and inserts, based on the panel’s height or width, which provide its seal when installed. Traditionally, PolySto managed the work-in-progress of each new product by manually tracking every panel, along with its inserts and molds, to ensure the proper matching of parts. This, however, proved to be a time-consuming process that could reduce efficiency.
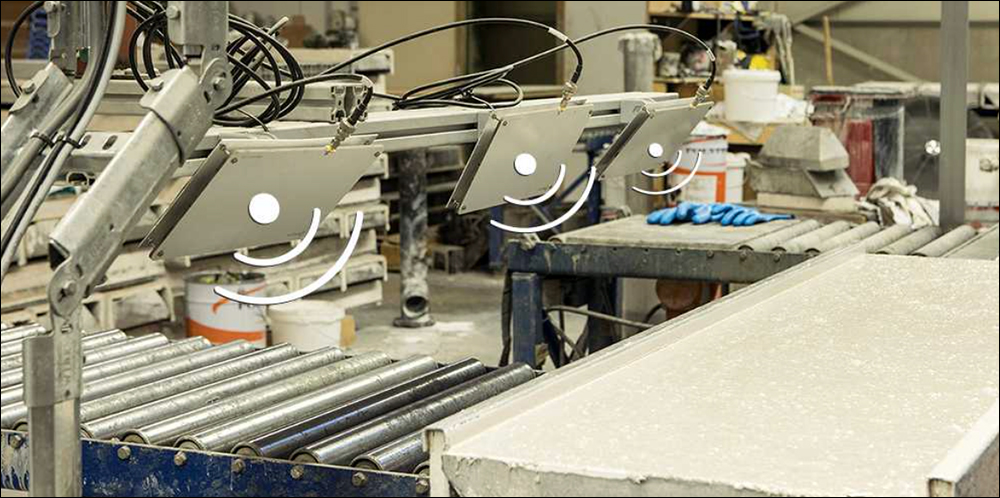
Each panel includes specific molds and inserts, based on the panel’s height or width, which provide its seal when installed.
Identifying Robot Parts via RFID
In 2020, says Jan Weymans, PolySto’s product manager, the company was preparing to replace some of its manual processes with a robotic system, but it needed a way for robots to identify each product and provide the necessary operations based on that identity. The company’s management began working with Aucxis to develop a solution that could capture the unique ID number of every panel and its related parts, both during and after production. “In this way,” he says, “the robot knows which program to select to finish the kerb.”
PolySto and Aucxis first conducted a proof-of-concept in late 2020. Then, after proving the system operated as needed, they deployed the Nova RFID Asset Management solution platform the following year, according to Lauran D’hanis, Aucxis’s account manager and business consultant. There were challenges related to RFID deployment in this environment, he recalls. For one thing, Weymans notes, the automation of production required the greatest accuracy and reliability possible.
The partners worked with Aucxis to ensure proper installation and power levels of RFID readers so that every tag would be read as each product arrived at the robotic station. The solution consists of passive UHF RFID tags mounted within the panels during the production process. Each tag ID is then linked to details about its corresponding panel. The inserts and molds are also tagged, and the unique ID number encoded on each tag is linked to the panel that is being assembled.
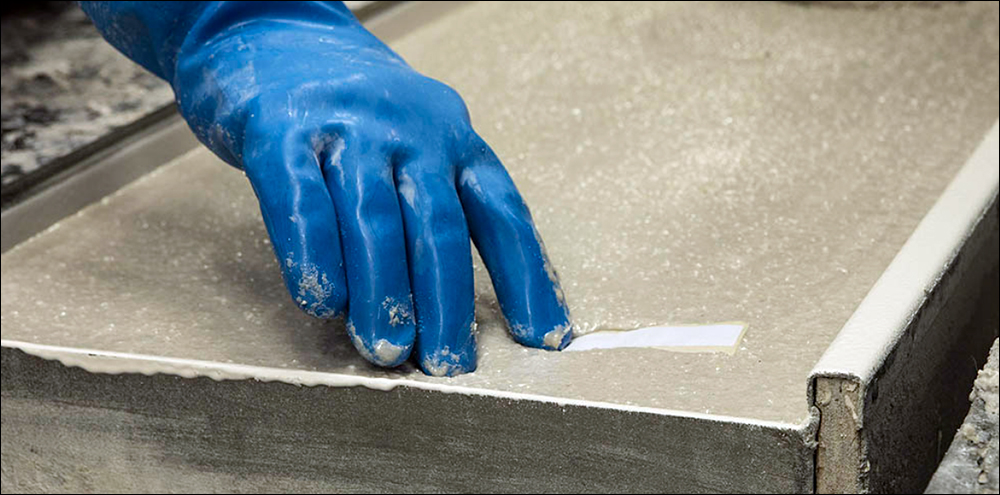
The NOVA system registers and identifies polymer composite kerbs during manufacturing process.
Automatically Linking Panels to Molds and Inserts
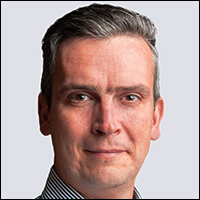
Jan Weymans
As a new panel under production proceeds through the manufacturing process, it passes a fixed RFID reader installed at the roller conveyor, which carries the panel to the assembly robot. At this point, the RFID tags are read, thereby creating a connection between the panel and the molds and inserts. Aucxis’s Hertz middleware connects the RFID read data with PolySto’s business application to instruct the robot regarding the proper procedure.
When the robot receives the panel, it can employ the RFID data to adjust its settings according to the product’s needs. Hertz also provides filtering, processing and the sending of data to the Polaris software. Management can use the Polaris Web-based portal to view details of each manufactured panel type, as well as its status in production. Workers sometimes employ the handheld RFID reader after the completed panel is being inspected and tested for tolerance. The quality-assurance approval can then be stored in the software, along with other product information.
During the RFID system’s deployment, Weymans reports, the greatest challenge has been to adjust the antenna power to ensure the most effective read. “Because the RFID tags are in our product,” he says, and thus cannot be mounted differently, any change to the system depends on the RFID antennas. That, he adds, makes it difficult to adjust quickly.
Eliminating Manual Counting
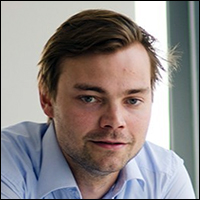
Lauran D’hanis
Since the RFID and robotic solution was deployed, PolySto has automated the registration and identification of panels, accessories and molds required for each new product. The use of robotics has reduced labor costs and improved productivity, Weymans reports, while the robotic system was made possible, in part, by the automated identification of each product as it arrives in that system. “The combination of the RFID technology and the robot,” he states, “will increase production capacity, but also increase efficiency.”
The company can use the Polaris cloud-based software to gain a real-time and historic overview of the production process. Because the RFID tag stays with the panel after it goes to the customer, it provides identification throughout the product’s lifespan. “By applying an RFID tag [to the wall protection product], you open up many future possibilities,” Weymans says. A few examples he cites are production registration by the buyer, as well as logistical management such as tracking and locating goods in a warehouse, inventory management, and managing the end-of-life for each panel.
“In the future,” Weymans predicts, “we will certainly look at how we can use [the technology] for automated stock management, but also for recycling. The latter is becoming increasingly important today,” to ensure the products’ sustainability and proper disposal. The deployment has proven the successful use of RFID technology in this environment, D’hanis notes, adding, “RFID tagging on poly-concrete is very feasible and often more easy than barcode scanning. It can also benefit a lot of process flows.”
Key Takeaways:
- By deploying RFID, PolySto Group has enabled the transition to robotic assembly by capturing the details of each panel (kerb) and its related molds and inserts, which enables robots to provide the necessary production processes.
- Since the system was deployed, the company has reduced labor time for its manual production process, as well as for counting parts and ensuring they were properly installed with each panel.