Luxottica Group, a global luxury sunglass and eyeglass company, reports that it has improved quality, as well as the efficiency of its receiving, quality-inspection and subsequent re-stocking of returned products, by between 30 and 50 percent, by deploying a Near Field Communication (NFC) RFID system. The solution employs an NFC dangle tag attached to each frame, and software that enables workers to view data about the item, and to update its status via NFC-enabled tablets.
Luxottica is a market leader in the design, manufacture and distribution of fashion, luxury, sport and performance eyewear. Proprietary brands include Ray-Ban, Oakley, Vogue Eyewear, Persol, Oliver Peoples, Alain Mikli and Arnette. Founded in 1961 by Leonardo Del Vecchio, the group is a vertically integrated organization that employs 77,000 individuals, backed by a global wholesale and retail network. In 2014, the firm produced approximately 80 million units worldwide, with total reported net sales of €7.6 billion($8.3 billion).
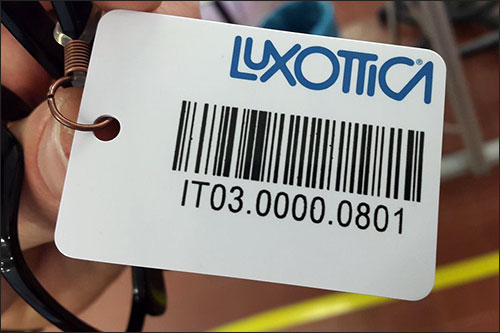
At its distribution and after-sales center in Italy, the company not only ships new products to retailers, but also receives and inspects frames returned by those customers as part of in-store collections-renewal programs, and then refurbishes them, if necessary. Only perfect-quality frames are restocked to be sold to other markets, the company reports. In this operation, Luxottica was targeting efficiency improvements via NFC technology use.
The eyeglass and sunglass market is partially driven by fashion, says Gian Stefano Fantini, Luxottica’s after-sales director, and some collection frames thus have a short lifetime in some markets, before they are returned and replaced by the next collection. Luxottica Group has an agreement with its more than 30 European Luxottica subsidiaries and commercial organizations to process returns from their customers. The crediting criteria for each organization depends on the type of frame being returned, as well as its quality.
Luxottica’s after-sales department receives hundreds of frames daily from stores across Europe. Prior to the NFC system’s installation, employees had a basically paper-based method of tracking each frame’s return and refurbishing process. They manually updated the SAP system with data, maintaining the link between the frame and the local subsidiary’s retailer in order to execute the specific crediting process.
Quality inspectors had to visually inspect the frames, and if any damage was found, that information needed to be input into the system as well. The frames were then routed to a location where refurbishment took place, such as tightening screws or polishing. Once the frames were refurbished, they were delivered to operators who used a catalog to identify the kind of packaging that each frame required, put that frame in that packaging and then shipped the product to the central warehouse.
The after-sales department operates as a multi-country service center; each day, on average, more than 200 batches of frames for customer return authorization are managed in parallel. The manual management of data related to these tasks within its processing facility is time-consuming, Fantini says, and the need to search through catalogs and manually input data limited how fast the frames moved from receiving to outbound. In addition, he reports, retailers had to wait until the manual process was completed before receiving their credit.
The company analyzed its needs and identified a technological solution that captures NFC read data, interprets and stores that information and enables Luxottica to perform analytics based on the stored data. The project, known as REvolution, was managed by Luxottica’s IT department.
When frames are received, workers now attach a reusable NFC RFID tag to each item and create a record in the REvolution software, which is integrated with the company’s SAP system. The frames are then moved to a quality inspector, who—with the support of a Microsoft Windows 8 NFC-enabled tablet—enters his or her own ID number and reads each frame’s tag, thereby linking the inspection to that individual. The worker then inputs data indicating that the frame passed inspection, or describes what specific refurbishing operations need to be carried out before it can pass. If the frame must be scrapped, a specific damage code has to be inserted.
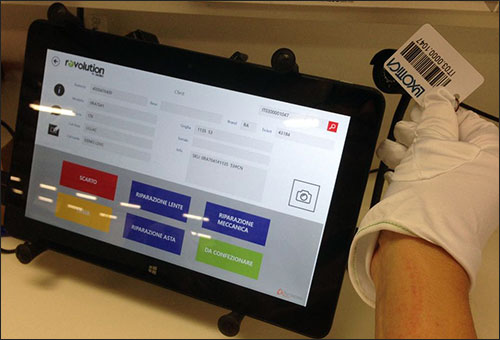
The software next transmits that data to the SAP system, which can manage the crediting process to the subsidiary or retailer, based on the returned frame’s condition and value.
When packaging the frames, workers use an NFC-enabled tablet to read each frame’s NFC tag, and the REvolution software indicates the packaging to be used for that particular product. They then follow those packaging instructions, while the software is updated to indicate that the frames are ready to be moved to the warehouse.
“Quality excellence standards have stepped up,” Fantini says, “as each frame or operation is tracked individually.” The manual paper-based process was eliminated, thereby boosting efficiency by up to 50 percent, with a positive impact on crediting and restocking lead times. “The process now is radically changed also from a visual point of view: Standard, fully loaded containers are now used to store all frames together as they come from different countries and customers, while individual information is maintained by the NFC tag tracking.” People are now focused on quality-control value-added activities, he notes, and not more on “flows” control. As a consequence, assessment errors were reduced by up to 30 percent. The next step will be the extension of NFC processing to Luxottica’s North America after-sales center, based in Atlanta, Ga.
Fantini will describe the details of his company’s NFC deployment and plans at this year’s RFID Journal LIVE! conference and exhibition, taking place on Apr. 15-17 in San Diego, Calif.