Aerospace company Boeing has deployed a real-time location system (RTLS) from Zebra Technologies to ensure that workers operating moveable platforms are wearing proper safety equipment when painting new aircraft.
Before installing the system, Boeing had already been well acquainted with Zebra’s RTLS technology. “Zebra has been offering their ultra-wideband (UWB) real-time location system hardware and software for asset-tracking applications at Boeing commercial and military sites,” says Daryl Stephenson, a Boeing spokesman.
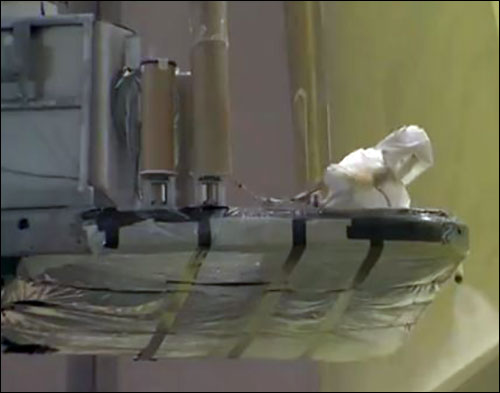
The idea for a painter fall protection system was devised when Boeing associates learned that Zebra’s MotionWorks UWB RTLS solution was being used by the National Football League (NFL) to track football players, says Jill Stelfox, the VP of Zebra Location Solutions. The system provides statistics regarding athletes and their performance, by using UWB tags and receivers to automatically capture game data, such as the amount of time that players spend in a huddle, as well as how fast an individual runs and how far he moves during a play (see RFID Drafted to Track NFL Players’ Every Move During Games). Boeing saw the potential to utilize the same kind of solution to track painters as they moved about an aircraft, working on platforms positioned dozens of feet above the ground, as opposed to players moving around a field.
“They told us they wanted to be sure their folks were safe when painting planes,” Stelfox recalls. The company challenged Zebra with designing a system that would disable the platforms’ motion if workers were not in a safe condition.
Airplanes are painted by a handful of painters at a time, each standing on a stacker—a large, moveable work platform that can rise, drop, or move left or right, thereby providing the painter with access to all parts of a plane’s fuselage. Staff members are mandated to wear safety harnesses while conducting the work, which sometimes requires that they reach over the fuselage and interchange safety lines while up in the air on stackers. However, Stelfox notes, even with safety harnesses in place, there are risks. Although spotters are responsible for monitoring the painters, there was no foolproof way for the company to be sure that all personnel were complying with Boeing’s safety policy 100 percent of the time. In addition, with multiple stackers moving around a plane at once, and with painters focused on their work and on managing heavy paint sprayers, it was possible for the painters to be unsafe.
The MotionWorks Painter Fall Protection System solution that Zebra developed for Boeing is intended to solve both problems: By continuously tracking the locations of staff members on stackers, the system can ensure that they are harnessed, hooked up and complying with Boeing’s safety policy. What’s more, the solution enables stackers to automatically shut off in the event that a non-compliant condition exists.
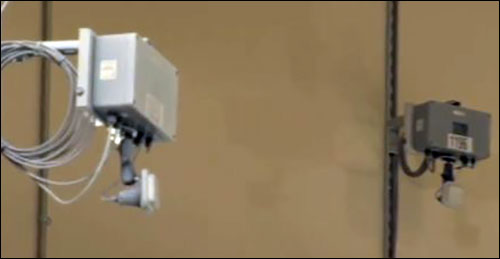
“It took both engineering teams—Zebra’s and Boeing’s—to put their heads together to keep these guys safe,” Stelfox says, including finding a way to ensure that the RFID technology operated in the heavy metallic environment. Zebra also had to spend considerable time learning about the painters’ work processes, in order to make the system easy to use for Boeing’s employees. The companies started the development work in early 2014 and required about six months to come up with a workable solution. Boeing began using the system in late July 2014 within six of its hangars, located in the Washington cities of Seattle and Renton. To deploy the solution, the company installed Zebra’s UWB receivers in the hangars and issued UWB tags to personnel. The location of each tagged worker is represented by an icon on a map of the hangar area, depicted in the MotionWorks software.
“This was outside of the box for us and something we’re really proud of,” Stelfox states. “They put their belief in us to engineer a solution, and I think they chose us because of our tenacity to get it done.”