For the past two years, Coriel Electronics, a U.K.-based provider of embedded electronics, has been developing a solution that employs passive ultrahigh-frequency (UHF) RFID tags and sensors to capture and transmit data regarding railcars, such as their location, and to indicate their identity in a system used for condition monitoring. Throughout that time, the company’s products have been used by its customers to identify railcars and components on those cars requiring maintenance. Once such customer is Alstom Transport, a France-based manufacturer (with global operations) that produces railroad infrastructure and rolling stock, and also provides maintenance services to the rail sector. Beginning this spring, several rail-infrastructure owners will begin undertaking pilots intended to determine if RFID technology can help manage the conditions of cars using their tracks, as well as monitor the speed of a train as it passes readers installed on those tracks.
Coriel’s rail automatic vehicle identification (AVI) solution consists of the firm’s DcTrak software, which manages read data, as well as its TrakStar RFID readers, installed at key locations within rail yards or adjacent to rail tracks, and linked to system sensors, such as axle counters and speed-detection systems. The technology is being used, in some cases, to capture the history of conditions related to a specific railcar, or a particular axle on that car, as it passes the reader and sensors.
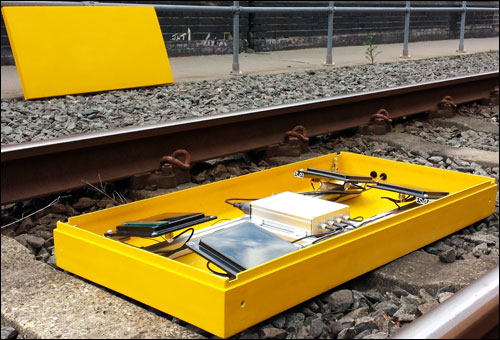
Coriel, located at the University of Nottingham Innovation Park (but not affiliated with the school), was founded in 2008 to provide electronic design for microcontrollers and processors, high-speed serial interfaces, sensors, and Bluetooth and RFID solutions, as well as software to manage those systems. The founders have a background in telecommunications, electronics and software, while their customers are typically manufacturers of telecom electronics products and other devices (such as MP3 players) that employ embedded electronics.
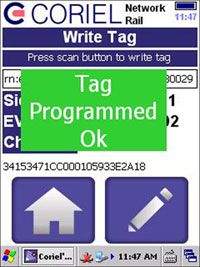
“We made a strategic decision two years ago to make RFID part of our growth strategy,” says Philip Leslie, Coriel’s business-development manager. Around that time, the company began working with Alstom, which had sought an AVI system for managing the maintenance, repair and operations (MRO) activities of its customers’ railcars at its maintenance yards. Alstom receives, maintains and stores railcars that its customers use on the U.K. rail network. Coriel determined that passive UHF RFID tags would be the best technology to automatically identify those railcars, Leslie says, and to pair each car’s tag ID number with data captured in the field from sensors monitoring that car’s condition.
These systems measure a range of conditions, from component temperatures to vibrations. Coriel provided Omni-ID Grip passive UHF EPC Gen 2 RFID tags, which were mounted to the undersides of railcars, as well as its own TrakStar 400 readers. Each interrogator is mounted in a protective case, along with four reader antennas, installed between the rails on the tracks used to transport cars to and from maintenance areas. The Grip, a rugged tag encased in polycarbonate and rubber, is made with an Alien Technology Higgs3 chip containing 96 bits of Electronic Product Code (EPC) memory and 512 bits of user memory. A condition-monitoring system, mounted at the same location where the reader is installed, transmits measurements in conjunction with the RFID data to Alstom’s own software system, for analysis and operations.
The TrakStar 400 system includes onboard activation sensors and a heating system (for use during harsh winters) that is installed between the rails on a track on which the cars are received, moved and serviced. As a train approaches the reader, its onboard sensors awaken that device, which then captures the car’s RFID tag ID number and alerts the condition-monitoring system to commence operation.
In addition to capturing the RFID information and alerting the condition-monitoring system, the DcTrak software also provides the operator with system diagnostics and alerts related to the health of the sensors and readers. Alstom installed the system in 2013, and Coriel expects further installations by Alstom to take place throughout the United Kingdom and the rest of Europe.
Multiple companies in the railway industry have also launched pilots of Coriel’s AVI systems, and are using RFID for multiple use cases. For example, several rail infrastructure owners will soon launch tests of the AVI technology, to determine passive RFID’s suitability to identify train cars moving at various speeds. Eventually, Leslie says, the data collected may be utilized to identify cars in need of servicing or replacement, with the objective of causing less damage to tracks and consequential interruptions of service.
As with the Alstom deployment, passive UHF RFID tags will be used—though in this case, they will be placed on the sides of each railcar. Tags will then be interrogated at various distances and speeds. The unique ID number encoded to each tag will be linked to the railcar owner, and details about that specific car will be combined with sensor data in Coriel’s DcTrak software. Coriel will install RFID readers at trackside, Leslie explains, and sensors will capture the speeds at which each railcar passes. This information can help the rail owner prevent unnecessary track damage, he says, by identifying when a car would cause excessive strain on the tracks, as well as helping to determine when a car might fail entirely while in transit on those tracks.
Last year, Leslie reports, the company received certification from GS1 UK for its UHF technology. “The certification means that buyers who want to deploy a GS1 standards-based system will have the comfort that this technology is compliant with GS1 global standards,” he states.
Additionally, Coriel is launching a tag-encoding application known as Tag-Star, designed to help ensure that no critical mistakes are made, such as encoding a tag with the wrong ID number or using the same number twice. What’s more, the company offers RFID technology for use in other sectors, such as logistics and manufacturing. One example is a cable and drum (spool) management system known as SmartDrum, with which drums and spooled cable can be tracked and managed at worksites by personnel equipped with handheld readers, or by fixed reader portals.