Summa Akron City Hospital increased the capacity of its emergency department (ED) in 2012 to meet the demands of a growing number of patients arriving for care. To learn how much that expansion has improved the rate at which it transfers patients from ambulance stretcher to hospital bed, the ED has been using radio frequency identification technology to identify when a stretcher arrives with a patient, and when it leaves without one. The technology, provided to the hospital by Barcoding Inc., most recently has been used to identify the response time at the hospital for patients during the 2015 winter flu epidemic.
Akron City Hospital’s ED treats individuals from approximately 30 municipalities for trauma, strokes or heart attacks. It serves an average of 270 emergency patients daily, for an annual total of 80,000 visits, with about 19,000 patients arriving in an emergency vehicle. That number has been growing (from 2013 to 2014, it grew 3.5 percent), in part because patients are more frequently going to the emergency room for treatment rather than for scheduled doctor visits. About 30 different agencies—such as municipal emergency medical services (EMS) and fire companies, as well as one private ambulance company—bring patients to the hospital’s ED, wheeling them in on stretchers, also referred to as cots.
Patients (and the ambulance company or EMS staff) then await the availability of a hospital bed, at which time the patient is transferred to that bed and the EMS or ambulance crew can then take the stretcher back to their vehicle and leave. Akron City Hospital considers both its patients and the EMS agencies as its customers, says Jon Zalewski, the hospital’s EMS coordinator. For the sake of the EMS units, as well as the patients, the facility tries to keep the waiting time for beds down to a maximum of 15 minutes. However, throughout the past decade, agencies were complaining that the transfer times were becoming longer as the department became more crowded.
In 2009, the hospital began seeking ways in which to track that length of time, and to compare any improvements as it expanded the emergency department. The hospital tried to monitor wait times for beds, with employees posted to record that time, but found that it was difficult to collect data this way since staff members tended not to stay on that task.
“We had unacceptable wait times to transfer ambulance patients from their emergency medical services cots to the ED beds,” Zalewski states.
The hospital needed a way to measure the actual amount of time that patients spent waiting for a bed. By using an RFID system, the facility would be able to determine whether long waits were actual or only perceived.
A trial RFID deployment took place in early 2010, consisting of Confidex passive Survivor ultrahigh-frequency (UHF) RFID tags zip-tied to stretchers, as well as a Barcoding Inc. Weatherproof RFID Interpreter RFID reader mounted near the entrance that had a USB port for downloading the collected read data to a computer, to then be viewed on a Microsoft Excel spreadsheet. The reader used for the trial was designed for trade shows, Zalewski says.
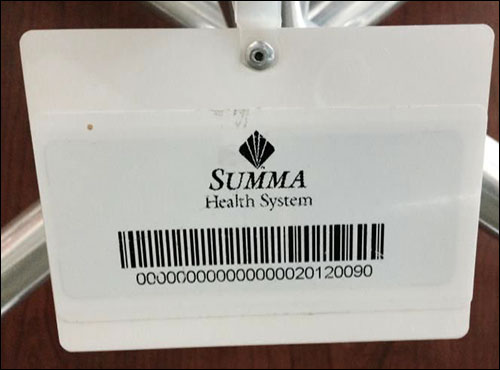
The hospital tested the technology for about six months. During that span of time, approximately 65 stretchers from 19 municipal agencies were tagged. The read rate, for ingoing as well as outgoing stretchers, was about 76 percent, which was a lower percentage than the facility would have liked. Another problem that arose was the loss of tags—they were often knocked loose as the stretchers were moved into and out of vehicles and into the field to transport patients.
Following the trial’s completion, the hospital continued collecting data from the RFID reader, and it has since increased coverage to about 100 stretchers from 30 municipalities or companies. A hospital worker attached a tag to each stretcher, and that tag’s unique ID number was linked, on an Excel spreadsheet, to data regarding that stretcher’s owner.
When its bed capacity increased in 2012 from 45 beds to 75, the hospital was able to use the RFID data to confirm that wait times were on the decline. The medical center’s goal is to transfer 90 percent of emergency patients from stretchers to beds in 15 minutes or less, and 100 percent in 30 minutes or less.
The RFID solution tracks those transfers in this way: An EMS or ambulance crew brings a patient into the ED on a stretcher with an RFID tag attached to it. The reader captures the ID number of the stretcher as it passes by, linking that ID with a timestamp to indicate when the stretcher arrived. Once the patient is transferred to a bed, the empty stretcher is wheeled back out through the same doorway, past the reader once more. Hospital management can later view the two timestamps for the single ID number on the Excel spreadsheet, and determine the wait time based on that information.
The hospital recently changed its hardware to an Impinj reader and standard UHF RFID tags. The tags, encased in a plastic covering to protect them from any hard knocks, are attached to a recessed location on the stretcher so that they are less likely to become torn off.
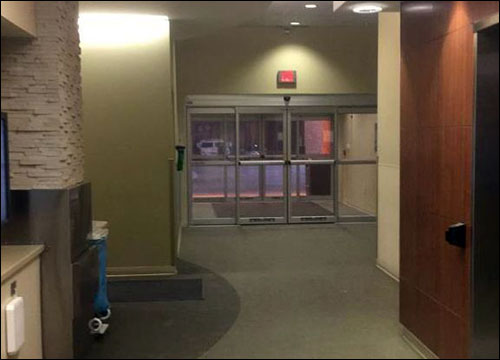
With the new reader and tags, and the new tag locations, the system is now capturing most tags as they pass through the hospital doorway in both directions. This year, the system was used to determine how much wait times were increased with the rising volume of patients around flu season, as well as at what times of day and on which days the longest waits occurred.
The greatest benefit of the system is gaining knowledge of actual transfer times, Zalewski says. The hospital can report these times to the EMS companies, he explains, which can then confirm that the hospital is “actively taking steps to address wait times.”
Although the hospital’s staff is only viewing the spreadsheet data after each day is over, Zalewski says his goal is to see the information displayed on a dashboard so that the rates of stretcher movements through the department could be viewed in real time. However, he says, that expansion to the RFID system awaits funding.
Thus far the deployment has been comparatively inexpensive: $7.50 per tag, totaling $750 for 100 tags. The reader cost less than $3,000.
Jon Zalewski described the deployment on Apr. 17 at this year’s RFID Journal LIVE! conference and exhibition, held last week in San Diego, Calif.