Editor’s note: As we get toward the end of 2023, RFIDJournal.com is looking back at some of the top stories that we published in the last year.
Star Cement has deployed a technology-based solution that tracks logistics at its three facilities in northeast India. The system automates the company’s management of vehicles as they deliver raw materials and pick up bagged cement products, thereby improving efficiency and on-time deliveries, while also reducing theft. The solution, known as Urgetruck, was taken live in February of this year, and it was provided by Kemar Automation as an ultrahigh-frequency (UHF) radio frequency identification (RFID)- and Internet of Things (IoT)-based plant logistics process automation system.
Star Cement, the largest cement brand in northeast India, provides products to building companies. At each plant, it receives raw materials such as limestone, ash and clinker. The cement is produced and bagged onsite, then is picked up by customers for delivery to construction purposes. Traditionally, the company managed operations at its busy facilities manually, with employees dedicated to recording the movements and weights of vehicles as they went about their delivery and pick-up tasks. Data was recorded on paper and was entered into Microsoft Excel spreadsheets.
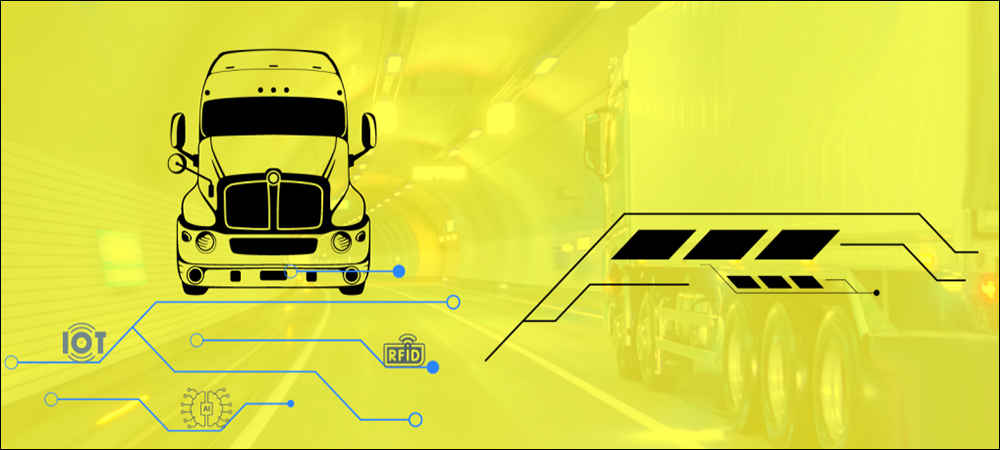
The Urgetruck solution has automated operations related to the receiving of materials and the loading of finished product.
The firm faced several challenges related to this process. For one thing, truck turnaround times needed to be faster, queues occurred, and some product was lost due to theft or errors, since the removal of product relied on individuals recording what was taking place. To address such challenges, the company sought a suitable identification technology that would identify trucks approaching each plant and moving within the loading area and scales. It found that UHF RFID, with tags applied to each truck entering the site, could provide the most reliable data in that environment.
Though license plate recognition and optical character recognition were also discussed, the company ultimately ruled them out. Rajeshwar Bhatt, Kemar Automation’s CEO, says most trucks in India already have UHF RFID tags on their windshields for toll payments. “This was one of the advantages for [Star Cement] to go for RFID technologies,” he states. The IT technology company focuses on improving and automating processes and logistics, Bhatt says, and Star Cement chose its Urgetruck solution.
Managing Truck Flow In and Out
To deploy the system, Kemar and Star Cement took a multi-pronged approach. The key challenge, Bhatt says, was to manage the flow of trucks entering and exiting the facility. The companies needed a system that would reduce congestion and delays, but that would also enable a more efficient flow of vehicles through the site. They also wanted to improve turnaround times as trucks were loaded and unloaded, increase dispatching efficiency and ensure incoming raw materials would be handled efficiently as soon as they arrived onsite.
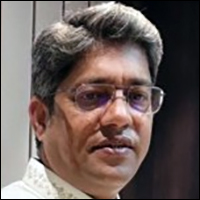
Rajeshwar Bhatt
Star Cement and Kemar Automation worked together to assign the key points at which data needed to be captured automatically regarding a truck’s presence and identity. Kemar then provided the company with a network of RFID readers from Zebra Technologies, along with motion sensors for identifying trucks at specific milestones during the process of delivering raw materials or picking up products. In total, approximately 70 to 80 readers were installed at each of the three sites.
As a truck enters the premises, it first approaches the gate, where an RFID reader is deployed. Many vehicles that use the facility already have an RFID tag attached to their windshield, and those that do not are assigned one. The unique ID number encoded on each tag is linked to details about a particular truck, as well as the company that operates it, in Kemar’s Konnect software, in order to identify vehicles approaching the gate. “Once the antenna reads the tag,” Bhatt states, “the reader passes them to our Konnect application, and we do the filtering and validation at Konnect.”
The collected data is forwarded to the Urgetruck software, which processes that information using an MTTQ messaging protocol. As each truck moves into the facility, it undergoes several processes, such as passing through a weighbridge, loading and unloading, and then exiting the gate. At each of these locations, the vehicle’s tag is again read to update the status of that delivery or pickup. Numerous gates around the facility also capture vehicle tag IDs as they enter specific areas.
Automating Manual Processes
With the solution in place, the manual process of weighing each vehicle at the weigh station and recording that value has now been replaced with an automated and unmanned system. The weighbridge captures each truck’s gross or tare weight, then links that data with the vehicle ID in the software. In that way, the cement company has immediate access to weight information, and can thereby reduce the incidence of errors.
The weighbridge system no longer requires personnel to record such details. The technology informs drivers of their next task on an LED display, accompanied by an announcement on a public address system, while the Urgetruck software provides a dashboard for centralized monitoring and action from supervisors. Bhatt says supervisors can communicate with drivers remotely if they find a problem or exception.
When it comes to loading and unloading, the RFID system can automate the allocation of a specific dock for every vehicle. The Urgetruck software automatically determines the appropriate space for a truck when it arrives, while large LED displays and voice announcements instruct drivers as to which gate they must report to, as well as where to park their vehicles. Arriving trucks receive permission based on the total capacity inside the area, and the software keeps track of every movement.
As trucks back into the loading area, RFID readers stationed there identify each vehicle based on its tag ID, and the software locates the appropriate batch of bagged product according to that data. The solution includes motion sensors installed to ensure the vehicle is present at the proper loading points, Bhatt says, as well as a fixed RFID reader to confirm the correct truck is being loaded with the right cement. Once the specific number of bags intended for a given order has been detected as having been loaded onto the truck, the process is automatically closed in the software.
Reducing Shrinkage, Increasing Availability
To prevent theft or shrinkage, the solution includes Zebra mobile handheld RFID readers with which security guards can read each tag as vehicles leave the site, thus automating data capture so product cannot be surreptitiously removed. The company reports that shrinkage has been reduced due to this security measure.
The system also comes with boom barriers at all gates to ensure that the right truck and the correct cargo are being handled at the proper time. Since the technology was taken live, Star Cement reports that it has achieved an improvement in truck turnaround times. This, Bhatt says, means vehicles can now enter and leave the site faster and more efficiently, and that more deliveries are possible.
According to Star Cement, the automation and real-time tracking of raw material handling ensures that products are available in a timely fashion, and that bottlenecks are prevented during delivery. Real-time tracking and milestone updates since the technology’s February deployment have ensured that the company gets its products delivered on time more often. That, Bhatt says, has led to improved customer satisfaction, while strengthening Star Cement’s reputation for punctual delivery.
Going forward, the cement company expects to add more features to the solution. In fact, Kemar Automation notes, it was deployed with a modular design intended for easy integration and scalability. Therefore, Star Cement could employ the technology for other functions as facilities’ operations require. Moreover, the firm can use the data resulting from the RFID tag reads to gain analytics that could help with scheduling, dispatching and other tasks.
Key Takeaways:
- Kemar Automation’s Urgetruck solution has automated operations related to the receiving of materials and the loading of finished product at Star Cement’s three facilities in Northeast India.
- Since the system was taken live, the company says its on-time delivery rate has improved, shrinkage has been reduced and trucks now move through sites more efficiently.