The U.S. Social Security Administration (SSA) has moved from its antiquated, slow and error-prone manual shipping and receiving process to a system based on bar-code technology. The change has led to major improvements for the agency, which provides 240,000 line items—primarily forms, booklets and other documents used by the Social Security program—to its offices across the country.
The agency was able to cut labor and operational expenses by nearly $1 million. Now, it has deployed an RFID tagging system it believes will further streamline its shipping and receiving processes, improving outbound shipment accuracy by up to 5 percent. The SSA says its receiving accuracy may improve by 25 to 30 percent once all its suppliers begin tagging shipments.
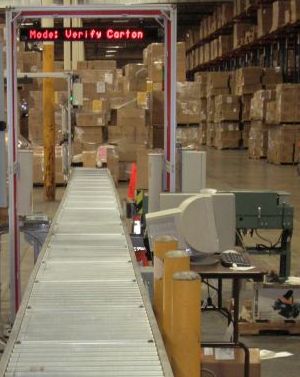
The SSA isn’t new to RFID. The agency has been working with the technology since a 2002 pilot test was held in an SSA supply room, in which it tested the use of RFID for an asset-tracking application (see Asset Tracking in Big Organizations). “The pilot showed management the feasibility of using RFID,” says Gary Orem, former SSA project manager and information technology specialist (now retired).
With management’s buy-in, Orem initiated a 2004 test using RFID for verifying cases and pallets of documents being shipped to SSA offices from its main warehouse and distribution centers in Woodlawn, Md. The SSA also purchased an RFID portal reader and tags, extending the relationship it had already established with Everett, Wash., RFID hardware manufacturer Intermec during the supply room pilot.
Intermec contracted systems integrator System Concepts, based in High Point, N.C., to design and deploy a means of tagging and verifying shipments. System Concepts worked with Canadian supply chain software provider Radio Beacon to develop integration points between System Concepts’ MasterTrax RFID middleware, which controls the RFID hardware and collects and filters RFID tag data collected by the readers, and the Radio Beacon warehouse-management system the SSA uses to process orders.
Presently, four additional SSA warehouses and distribution centers in the Baltimore area are RFID-enabled, and the agency is placing tags on roughly 30 percent of the goods it ships—most bound for SSA offices, with a small percentage sent between the warehouses. The tags are used as an automated means of verifying that orders are picked accurately and leave the facility complete. As it receives an order from the SSA’s order management system, the Radio Beacon warehouse management system uses a set of business rules (based largely on the size of the order) to determine whether the cases and pallets require RFID tags.
For orders requiring RFID, print commands for shipping label are sent to a bank of Intermec PM4i smart label printer-encoders. Encoded to the EPC Gen 2 UHF RFID inlay inside the label is the serial shipping container code (SSCC), a serialized number the SSA uses to identify each case it ships, whether labeled with just a printed a bar code label or an RFID inlay.
Warehouse personnel pick and label the cases, placing them on a conveyor system used to move cases to an area of the warehouse where all orders are palletized. If the order is RFID-enabled, the workers power up an Intermec IF4 portal reader installed alongside the conveyor. The reader collects the SSCC from each case’s label and sends it to the WMS, which pulls it into a list of SSCCs for that order. A motion sensor determines each time a case enters the reader’s interrogation field. If the reader does not successfully read a tag, the system alerts personnel to handle that case as an exception. Once all cases have been read, the WMS generates an SSCC to identify the pallet. That SSCC is associated with the SSCC of every case on the pallet. Personnel can then ensure that the pallet tag has been accurately encoded before the pallet is placed on a truck.
In March of 2005, one of the SSA’s major document suppliers began placing pallet tags on its goods. It has continued to so since that time, and Orem says this supplier’s shipments have become 100 percent accurate, consistently, since it began using RFID to verify its outbound shipments. For the SSA, the ability to use RFID labels to receive the pallets into its warehouse (rather than reading the bar-code label applied to the pallet) has cut labor. Now that this supplier is consistently sending complete and accurate orders, the SSA has cut its administrative costs, as it no longer needs to reconcile incomplete or inaccurate orders with this supplier.
Orem says the SSA is currently working with a handful of other suppliers that also tag their shipments. As the suppliers’ government contracts come up for renewal, the SSA plans to add RFID-tagging requirements to them, just as the Department of Defense (DOD) is doing. “We’ll be making case and pallet tagging mandatory,” says Orem. Eventually, the SSA headquarters in Woodlawn, as well as four additional SSA warehouses, will be using RFID both to receive and ship all products.
Orem says he hopes to grow the SSA’s use of RFID technology by working with all of the vendors from whom the agency purchases such valuable assets as desktop and laptop computers, to place tags on these goods before shipping them to the SSA. Orem envisions that the SSA would read the tags to receive the goods into its asset inventory, then also use the RFID tags to identify the items as they are put through their regular maintenance schedules. For example, IT personnel would use a handheld interrogator to identify a desktop computer requiring service rather than trying to crawl around under a desk to locate the computer’s bar code or serial number plate. If the SSA expanded its use of RFID in this way, Orem says, it could save up to 70 percent of the labor costs associated with managing valuable assets.