- RFID Deployments Travel Up the Supply Chain
- Leveraging Clustag Hardware and Middleware
- Testing New Solutions at the Innovation Center
In November 2022, technology company SML opened a new Supply Chain Innovation Center (SCIC) in Corby, England, where the company is demonstrating and testing radio frequency identification (RFID) solutions for reading passive UHF RFID tags on apparel and footwear as well as home goods and cosmetics in a variety of supply chain use cases. The system allows users to see how tagged items move through a typical distribution center environment, and to see how it would apply to their environment. The goal, according to SML, is to provide customers with greater visibility into their products throughout the supply chain, enabled by RFID tags applied to items at the point of manufacture.
SML recently partnered with logistics automation company Rielec, and the combination of SML’s Clarity Supply Chain solutions and Rielec’s Clustag solutions are on display at SML’s first SCIC facility. (Clustag is Rielec’s brand for RFID readers, including tunnels and cabinets.) By bringing products from the two technology firms together, SML and Rielec have worked to create a comprehensive enterprise solution offering, according to Dean Frew, SML’s CTO and senior VP of RFID solutions.
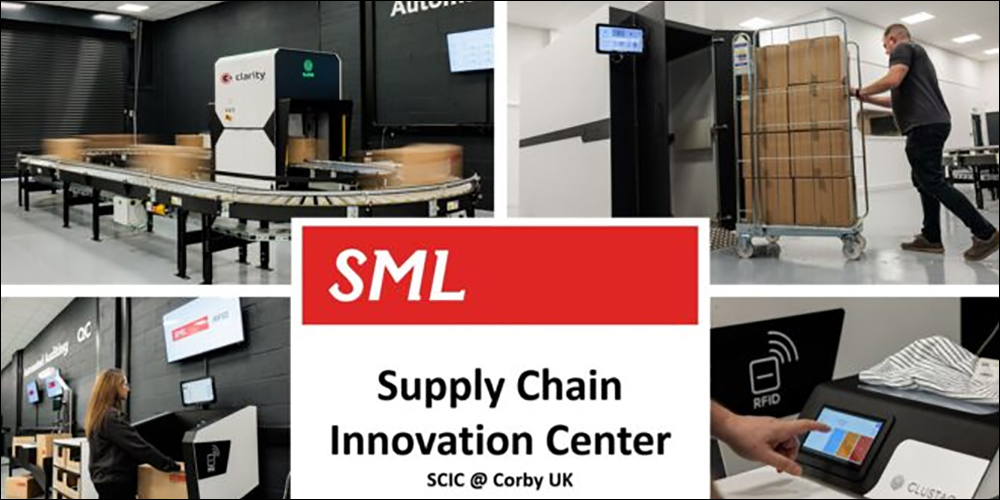
SML’s Supply Chain Innovation Center (SCIC) in Corby, England
The SCIC site includes SML’s Clarity software and custom-made Clustag equipment for the mass reading and encoding of labels, and the facility specializes in solutions integrated into material-handling systems for packing distribution, as well as garment-on-hanger systems and manually operated warehouse workstations. The Corby facility adds to the SML Retail Ideation Space (RIS) that was opened there in 2019, along with similar sites in Plano, Texas, and in Hong Kong and Shanghai. The company opened a smaller SCIC at the Plano facility this month.
RFID Deployments Travel Up the Supply Chain
SML reports that its customers have indicated a need to expand how their RFID solutions are being used for retail apparel and footwear management. While RFID tags applied at manufacturing sites were initially being read predominantly in stores for inventory-management purposes, businesses are now looking to expand up the supply chain to read tags long before they reach stores.
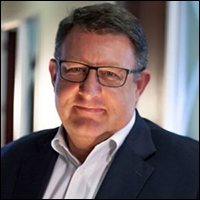
Dean Frew
“The retailers that we’re working with [want] to be able to do inbound box-level auditing” at the point at which goods are received at the distribution center, Frew says. “And many of the brands we work with are wanting to do outbound auditing” to track the picking and packing of goods shipped out to stores or directly to customers.” By reading the tags on goods packed in boxes, he explains, these customers are better able to prevent errors and provide proof of correct shipping to recipients.
Companies that had tried to set up DC-based RFID systems in the past often ran into hurtles, Frew notes. “They were running into some challenges around the read rates,” he states. “You turn up the power, you read stuff… and all of a sudden, you’re reading boxes that are in front and behind the box.”
Requests for supply chain data at distribution centers was the genesis of the SCIC, Frew recalls, and are also the reason that SML is now partnering with Rielec to use its highly accurate tag readers. Together with Rielec, he says, SML is building a series of supply chain products to provide inbound and outbound management, as well as carton-level packing and order auditing.
SML and Rielec began partnering on solutions aimed at distribution centers in April 2022, to offer UHF RFID material-handling systems that could include RFID reader tunnels, reader stations and handheld readers, combined with SML’s Clarity software for high-volume, reliable and accurate reading at warehouses. Read accuracy is imperative for customers in this environment, Frew says. “You can’t have these things be breaking down,” he adds, “and they have to work accurately, every time.”
Leveraging Clustag Hardware and Middleware
The solution consists of RFID tags of the user’s choice, in addition to Clustag hardware and middleware, Clarity software and a business-intelligence layer provided by SML. The RFID systems are built for warehouse environments. “Clustag’s MOT RFID Station is what we consider the outright solution for high-flow RFID conveyor tunnels,” says Luis Rius, Rielec’s CEO and founder.
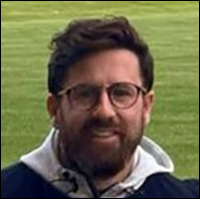
Luis Rius
The readers come with fully enclosed areas inside the tunnel, on conveyors, which act as an electromagnetic shield or cage. That shielded cage helps to ensure more accurate reads, Rius says. Because the read area is enclosed, he explains, “We can raise RFID power-emitting levels with no risk of outer readings, achieving a 100 percent reading performance,” with no separation between cartons required.
Traditionally, Rius says, tunnel reading has required some balancing between reader strength and the potential for stray reads from cartons in the area. The result is often what he calls poor performance levels. Clustag MOT, he adds, stems from years of research pursuing 100 percent reading performance in RFID tunnels. The Clustag MOT RFID Station is provided with PLC and an AS-Interface modules so that the reader can be operated with peripherals when required to do so, such as material-handling equipment, sensors, barcodes and other devices.
Clustag MOT RFID Stations scan RFID-tagged cartons and validates items against shipment orders, while also reporting variations. If an exception is identified, the carton is rerouted for reconciliation. Bulk validation with the tunnel can be installed at various points along the distribution process, Rius says, after orders are picked, when items are packed or wherever shipment audits are to be performed. “At Corby,” he states, “we are providing our state-of-the-art solutions both for manually operated RFID-enabled workstations and a Clustag MOT RFID Station integrated into a conveyed racetrack.”
This, according to Rius, allows customers to check their products being tested. As a result, the Clustag and Rielec system is intended to provide 100 percent read accuracy so that companies can address tagging errors before products leave the DC. Such RFID tag errors, Frew says, cannot be detected via simple tag reads at stores. Companies have indicated they experience errors such as mispacked cartons that were supposed to have a specific number of products of a certain stock-keeping unit, with the number not matching. In other cases, tagged items are received, but the tags are inoperable.
By the time a problem like this “works its way into the river of tags going to stores,” Frew says, “nobody can stop and actually identify them.” Another challenge for retailers is that many are starting to put in place compliance programs by which vendors that fail to tag certain products must pay a penalty. Detecting such errors without accurate reading at the DC makes compliance programs difficult to enforce.
Testing New Solutions at the Innovation Center
For both brands and retailers, the benefit to having data from a DC is the ability to monitor what factories are sending. One example is a deployment for New York-based Herman Kay in 2015 (see Herman Kay Gains Packing Accuracy Via RFID). The outwear brand was receiving chargebacks from retailers related to claimed shipping errors, so the RFID system was used to ensure that every order would be packed accurately. “They got to a place where they eliminated most of their chargebacks,” Frew states, “because their shipments were perfect.”
The Corby SCIC, a 303-square-meter (3,260-square-foot) facility, is being converted as a simulated warehouse with supply chain management equipment for testing. The site includes what the company calls a “DC and store receiving station,” that reads hundreds of tags simultaneously when a cart loaded with packed cartons is rolled into a shielded cabinet. It also has an inbound and outbound case-auditing conveyor, known as a “racetrack,” with an enclosed and shielded tunnel reader. In addition, there is an auditing and box-packing station, handheld DC stock-count and stock-finding functionality, and an RF returns surface. Users can view the read data and analytics on a Clarity dashboard.
The offerings from SML and Rielec being displayed and tested at the Supply Chain Innovation Center “take the item-level RFID business case and step it up back up the supply chain,” Frew says. Most early adopters of this technology will be those that have already deployed it at their stores, he notes. Some customers viewing the technology have indicated that they didn’t realize how much data could be collected by automating RFID reading in the supply chain, Frew says. He recalls being told, “‘We didn’t know we could do that, because we tried it and we couldn’t. We couldn’t read hundreds of items in a box in a second, and not read the things we didn’t want.'”
In the long term, Frew predicts, tracking RFID-tagged goods throughout the supply chain will drive further benefits to users, such as brand authentication and diversion detection. If a box of tagged products is detected on its way to a particular store but is received at a different location, the system can identify that misrouting, for example. SML has leveraged its innovation centers as places where customers can see technology at work. “Bottom line,” he states, “is we’ve got customers in the U.S. and customers in Europe that are already adopting the technology, and it makes this a great place to develop [our own] product but also to be able to work with clients.”
Key Takeaways:
- SML and Rielec are allowing customers to test their technologies for the DC environment at SML’s new Supply Chain Innovation Center in England.
- Rielec’s readers are designed with electromagnetic shields aimed at ensuring 100 percent read accuracy in warehouse settings.