For the past three years, Italian women’s fashion brand and retailer Sandro Ferrone has been tracking goods tagged from the point of manufacture through to its primary distribution center. During the coming months, that deployment will be expanded to a second DC, as well as to some of its more than 200 store locations, most of which are in Italy. Since the system was taken live at its DC in Rome, the retailer reports that it was able to reduce the amount of labor required to pick products for store orders from 18 full-time employees down to six, while achieving 99 percent inventory accuracy.
Sandro Ferrone specializes in women’s “fast fashion”—a trend that keeps newly designed apparel coming to consumers at a pace more rapid than that of the traditional retail model. The clothing brand and retailer releases five collections each year, as compared with the traditional model of two annual collections. Each year, Sandro Ferrone offers 800 unique garments or accessories and sells a total of two million items. To accomplish the fast-fashion supply needed in stores, the company must be able to move a limited volume of specific products very quickly, in order to ensure that the latest garments are available at the shops while there is low risk of merchandise remaining unsold.
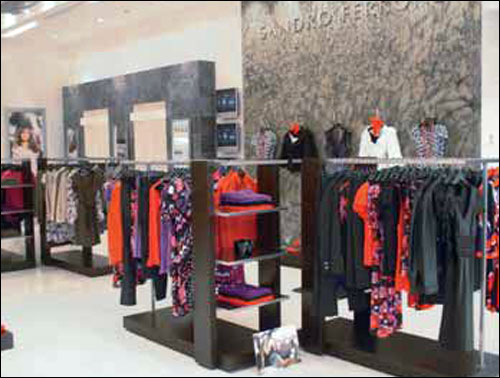
In 2011, the company piloted an item-level RFID system to track each garment from its factories to its distribution center in Rome, and on to shipment to stores. Following that trial, Italian systems integrator Maestrale Information Technology, with support from RFID Global by Softwork, permanently installed the technology at the Rome DC (the company’s main warehouse). Sandro Ferrone now plans to expand the deployment to a second DC, as well as to stores, throughout the next few months.
The solution employs EPC Gen 2 ultrahigh-frequency (UHF) RFID labels provided by Tageos. According to Nicolas Jacquemin, Tageos’ VP of sales and marketing, Sandro Ferrone’s suppliers use an RFID-enabled version of Toshiba‘s BSX4T printer to generate an RFID label for every garment. The unique ID number encoded to each label’s RFID chip is linked to the specific garment’s stock-keeping unit (SKU) and other information, such as the date and location of manufacture, in software provided to Sandro Ferrone by Italian software firm Zucchetti.
The label itself—the EOS-300, made with a paper-only substrate with a printed antenna—is inexpensive, Jacquemin says. Sandro Ferrone selected that label not only for its low cost and ability to be easily printed with product information, he notes, but also for its dimensions—54 millimeters by 34 millimeters (2.1 inches by 1.3 inches)—which matched those of the price tags already being attached to the products.
The clothing factories then pack and ship the tagged merchandise to the Rome distribution center, where a fixed Feig Electronic LRU3500 reader with four antennas, mounted at the dock doors, captures each tagged item’s unique ID number and forwards that information to the Zucchetti software, thereby updating the product’s status as received in the warehouse. The goods are then stored on shelves until retrieved to fulfill a specific store’s order. Until that time, the DC staff uses Nordic ID Merlin RFID handheld readers to collect inventory data regarding which products are located on which shelf within the warehouse.
Once a store places an order, employees again use a handheld to locate specific items and pick them for shipping. The use of RFID ensures that workers have collected the correct product, while the software stores that data to create a record of each order’s picking process. Packed boxes are then loaded onto trucks, at which time they pass through the fixed reader portal, which collects the tagged items’ ID numbers, thus indicating that they have now been shipped.
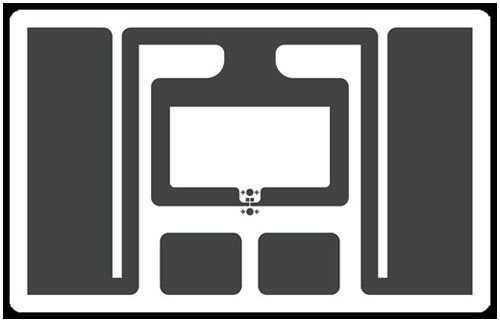
In the future, the company indicates, the stores will also be equipped with RFID readers at exits. This will help the retailer to prevent shrinkage by identifying when an item still tagged—signaling that it was not purchased—passes through the door.
Since the RFID system was taken live, Sandro Ferrone has seen an increase in its DC’s receiving and picking efficiency. A worker previously required approximately 10 minutes to identify 100 items arriving from the manufacturing point, the company reports, whereas that same task can now be accomplished in about six to seven seconds.
Sandro Ferrone reported to Tageos that order preparation also became faster and more efficient, since personnel could easily identify the items they picked using the handheld reader, rather than having to scan a bar code or visually inspect every item.