When MSR-FSR began offering laundry services for clean-room coveralls at its facilities in Albuquerque, N.M., and Hillsboro, Ore., it needed to maintain a precise account of each item coming through its two sites. By managing data regarding which items are washed or repaired—and how often that occurs—the MSR-FSR and its customers (nearby semiconductor companies) are afforded a record proving when and how the items were cleaned, as well as when they may need to be repaired or replaced. To manage that information, the firm is employing an RFID-enabled solution provided by InvoTech Systems a laundry, linen and uniform cleaning system company. The solution includes Impinj Speedway Revolution readers, AN720 and AN480 antennas from Motorola Solutions and passive EPC Gen 2 RFID tags provided by Fujitsu Frontech North America.
Clean rooms are enclosed environments for manufacturing or scientific research in which the level of contamination—such as dust, airborne microbes and other particles or vapors—is closely restricted and monitored. Because street clothes may contain contaminants, clean-room workers must wear special coveralls, and sometimes aprons or smocks, all of which must be laundered according to regulated standards.
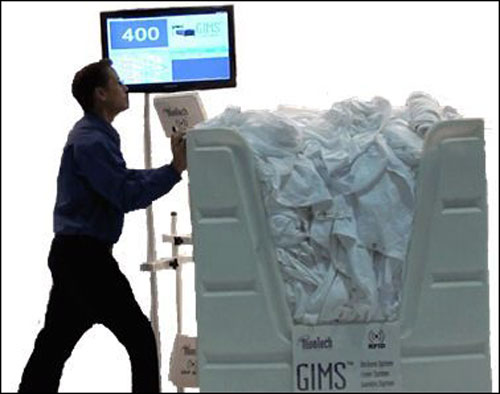
To help track these laundering process, MSR-FSR opted to deploy an RFID-enabled solution.
“We estimate the efficiencies gained exceed 23 percent in comparison to the industry-standard bar-coding solutions,” says Steve Cox, MSR-FSR’s CEO for global operations. “We are now processing several thousand individual items daily, requiring a much more efficient system to track all materials through the varying processes.”
InvoTech Systems’ technology has traditionally been used in the hospitality and health-care markets, for cleaning uniforms, tablecloths, napkins, gloves and other reusable items, according to Jeff Welles, the company’s VP. The use of such a system for clean-room garments was a new application for InvoTech, he says, since it required not only an electronic record of when an item was washed, but also how it was washed and in which machine.
MSR-FSR processes a total of 112,000 pounds per month of Class 10 (allowing a maximum of 350 particles per square foot) clean-room coveralls at its Albuquerque and Hillsboro facilities. The company wanted to implement a system that could verify which service was provided, not just for customers’ records, but also for its own billing purposes. To that end, Cox says, MSR-FSR asked InvoTech to create a solution in a short period of time, “as we had been working with another software that failed to meet our standards.” He adds, “Not only did they meet the requirements in the time periods committed, but the team that was used for installation and training was probably the most professional we have ever dealt with.”
InvoTech’s GIMS Laundry System is already being used by hundreds of properties to manage the cleaning and maintenance of employee uniforms, Welles says. In this case, the firm modified the solution to meet the specifications of clean-room services, by programming the software to track not only when an item was washed, but also in which machine, the detergents used and the temperatures at which the washer and dryer were set.
First, MSR-FSR applies RFID tags to each new item that arrives for cleaning. InvoTech provides Fujitsu’s rubber-encapsulated ultrahigh-frequency (UHF) inlays—the same tags used in InvoTech’s laundry system—which are sewn onto every item via a fabric label. At the time that the new tags are attached, a staff member uses an Impinj reader is used to interrogate each tag ID, and, via a drop-down menu, selects which type of item it is. The tags can sustain approximately 200 wash cycles or three years, Welles estimates.
When soiled items arrive at either of the two facilities, they are placed in carts and wheeled past an Impinj reader that captures each tag’s unique ID number and forwards that information to the GIMS software. The software links the tag’s ID with the item to which it is attached, as well that garment’s washing and repair history.
Employees then sort the garments according to type (that is, coveralls, smocks, aprons or gloves), and fill new carts with products specific to where they will be directed for washing or repair. Items requiring repair are moved to another section within the facility. Those tagged items destined for washing are then pushed in the cart to the washer areas, where a second Impinj bulk reader awaits to read the ID number of each garment in the cart. The staff then inputs which washer will be used, as well as the washing recipe (the amount and type of detergent, along with the temperature setting). Once washed, the items are then placed directly in the dryer. According to Welles, attempting to read the tags before they enter the dryer could be difficult, because the high amount of water may absorb RF signals.
Once dry, the garments are removed from the dryer, placed into a cart and taken once more to the reader, where the tags are read. A staff member then inputs from which dryer they came, as well as the temperature used.
Next, the items are folded and prepared to be returned to the customer, and the tags are read a final time as the cart is pushed past another Impinj reader located at the loading dock. The GIMS software stores data with every read, linked to each item. When the garments are shipped, a bill can be sent that reflects exactly which services were provided. An Impinj desktop reader is also used in a repair area, and in a prewash stain-removal section, to indicate those services were performed.
The readers can interrogate and process hundreds of UHF tags per second, Welles says, at distances of up to 6 feet away.
With the RFID system, which was installed in Albuquerque in January and Hillsboro in March, “our efficiencies in tracking thousands of product each day in greatly enhanced,” Cox says. In the future, he adds, the company intends to install the system at its facility in Ireland as well.
Typically, Welles notes, the GIMS Laundry System pays for itself within approximately 10 to 15 months.