When meat-processing workers enter the plant floor where meat is cut and packaged, they bring with them a batch of cutting tools that require close scrutiny. The knives and cutting devices must be frequently replaced and sharpened daily. A knife that remains in the work area after an employee leaves his or her shift, and is then reused, could contaminate the meat and require the destruction of an entire day’s worth of products.
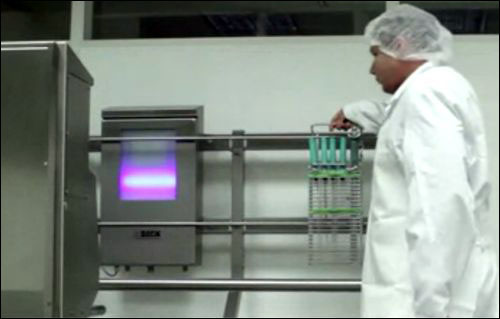
To address this problem, German cutlery manufacturer Friedr. Dick has developed a solution, known as Knifeinspector, that includes passive RFID tags built into the handles of its knives, as well as in staff ID badges. Readers can be installed at entrances and exits, cleaning and sharpening stations, or other requested locations, in order to track those tagged tools at a processing facility. The solution employs RFID interrogators supplied by Kathrein and Nordic ID, while the software was developed by Freidr. Dick in cooperation with Enso Detego. With Knifeinspector deployed, meat processors can track and trace which individuals brought which tools onto the plant floor, whether they brought all of them back at the end of the shift, and whether the knives were sharpened prior to reuse.
“We had been approached by a lot of customers seeking a simple solution to allocating a knife to a person,” and then to ensure the knife was returned, sharpened and cleaned, says Steffen Uebele, Friedr. Dick’s director of sales and marketing. Not only is a dull or worn-out knife dangerous to workers, but if one is left behind within the processing area, and has thus not been cleaned, that action can cause costly and dangerous contamination. In addition, many meat-processing plants suffer from shrinkage. Staff members simply may not return all of the knives they use, or may return another worker’s knives, rather than their own. Over the course of a year, this can add up to a major cost for a large plant containing many knives. For meat companies, Uebele explains, “It’s a huge problem to guarantee that 100 percent of tools that enter the production site leave that site,” and are then properly cleaned and sharpened for reuse.
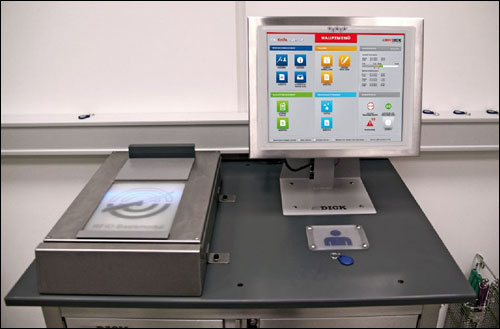
Friedr. Dick’s customers wanted each worker to be held responsible for his or her tools, thereby ensuring that every employee would be sure to bring all tools back off the floor and turn them in for cleaning and sharpening, rather than leaving them behind, allowing another staff member to use them or bringing them home.
The cutlery company began working with Enso Detego to develop an RFID system, says Alexander Gauby, Enso Detego’s general manager responsible for innovation and product development. Enso Detego created a software solution and helped select the appropriate RFID hardware to collect data for that software. The resulting solution, according to Matjaz Novak, Enso Detego’s marketing director, has three parts: the RFID-enabled knives, as well as sharpening steels and other tools; the reader hardware; and the software used to manage the collected data. Hardware, software and installation of the RFID solution will be provided by Friedr. Dick’s RFIDick division, while Friedr. Dick and its distributors will sell the RFID-enabled tools.
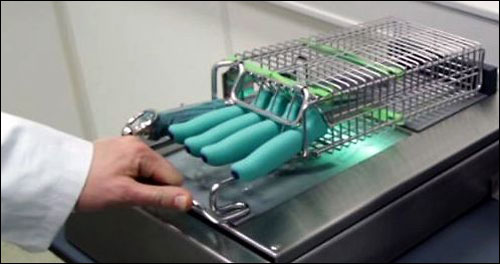
A large meat plant in Germany is currently in the process of installing the solution. Friedr. Dick may extend the system’s use to products from other tool manufacturers looking to integrate their products with the Knifeinspector solutions. Friedr. Dick installs readers at the plant floor’s entrance and exit, and can also deploy them at additional customized tracking points as well, such as at grinding areas. The software resides on the customer’s server.
First, workers proceed to the tool-issuing station, equipped with an RFID reader, and acquire the necessary toolkit, such as a wire-mesh basket filled with RFID-tagged knives. Each worker then places the kit, as well as his or her RFID-enabled ID badge, on the reader. All RFID-enabled knives within a particular kit are then linked to that person’s ID. To enter the plant floor, the worker walks through an access station and places his toolkit next to the built-in reader. The system registers all items contained within and confirms their status. In the event of any deviations, such as a knife that should not be entering the processing floor, an error message will be displayed a computer screen.
Upon leaving, the employee again places the toolkit next to the access-station reader. If the software determines that a knife is missing, it can issue an alert, either as an audible warning at the location at which the reading took place, or as an e-mail or text message that can be sent to management. The tools are then expected to be moved to a washing station, as well as a grinding station for sharpening. Some customers may opt to install RFID readers at these locations, in order to create a record of that process.
The solution is scalable, Uebele says. Users can start with using RFID simply for registering tools as they are allocated to personnel, and can further track who takes tools onto and off the work site, by installing readers at processing-floor exits. What’s more, users can also employ handheld readers so that the quality-management department can periodically search for knives and check their status, or record the disposal of tools that have reached their full lifespan.
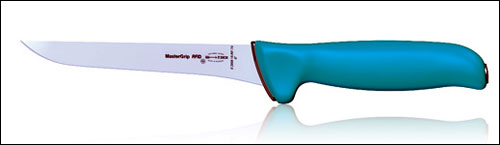
Friedr. Dick is integrating RFID tags in a wide range of the company’s meat-processing products—including boning knives, sharpening steels, sharpening devices, chain-mail gloves and knife baskets.
The company is also releasing a smaller, less expensive version of its solution, known as Knifeinspector Easy, which includes a small Read Me RFID reader from Microelectronics Technology Inc. (MTI) that plugs into a laptop’s USB port, along with software for tool management and the allocation of tools to workers.