In 2012, Johnson Controls was looking to improve its visibility into the millions of returnable containers used by the company’s Automotive Experience division. The firm was challenged by costly loss or slow movement of the containers that carry components from its multiple plants to its distribution centers, and that transport finished products to customers. To rectify this problem, the company launched a cloud-based RFID solution provided by Smart Label Solutions (SLS), enabling it to track hundreds of thousands of reusable containers, as well as molds and other manufacturing tools, at two plants operated by its automotive division.
The RFID solution employs software supplied by Ohio-based Surgere, SLS’ reader portals with NeWave Sensor Solutions‘ Wave antennas, Zebra Technologies handheld readers and a combination of Avery Dennison and Metalcraft RFID tags.
Brian Kelly, Johnson Controls’ director of supply chain management, described his company’s implementation and future plans at RFID Journal LIVE! 2016, held earlier this month in Orlando, Fla.
Some of Johnson Control’s approximately four to five million containers and racks enable the company to transport the components—such as trim, headrests and seat backs—to its factories, where workers assemble them according to customer requests. The finished products are often loaded onto containers and racks, and then moved through DCs as well. Once received by a customer, the racks and containers are expected to be returned empty, for reuse at the manufacturing plants.
The containers and racks, which come in varying sizes and are composed of metal or plastic, range in value from $3 to $1,500 apiece. While there are 508 unique types of containers, most, Kelly says, are black and look like many of the other models. Tracking what is on hand at each facility at any given time had required visual inspections and multiple phone calls—and if some seemed to be missing, Johnson Controls had to order new containers as replacements. Sometimes, the company purchased cardboard containers to replace the missing plastic or metal versions if goods had to be shipped by a certain date and no containers were available.
With an RFID system in place, Johnson Controls hoped not only to reduce the incidence of loss but also to identify which parties were not returning containers. So in 2012, Johnson Controls’ Technology & Advanced Development (T&AD) group evaluated RFID technology and its capabilities, and then launched a project with the company’s supply chain management team to determine how the technology could be used most effectively.
Johnson Controls selected the solution from SLS and conducted a seven-month proof-of-concept (POC) that ended in January 2015. For the POC, the company set up an SLS smartPORTAL at the dock doors of two of its plants, tagging four types of containers that pass between the two facilities. The firm decided that the POC deployment proved that RFID could be used to effectively address its needs, and thus began installing RFID SLS smartPORTALs across its plants and DCs.
At each side of the approximately 8-foot-wide dock doors, Johnson Controls bolted a smartPORTAL to the floor, according to Jeff Hudson, SLS’ CEO. A total of 1,200 smartPORTALs were installed at 600 dock doors within 37 facilities, in order to read the tags of containers arriving at and exiting each location. With the Wave antennas built into the towers, Hudson explains, the system knows in which direction every tag is traveling.
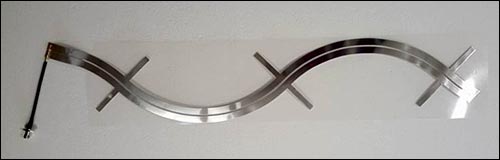
Each smartPORTAL—which contains an Impinj R420 reader and two NeWave Wave antennas—stands 8 feet tall and can read tags as high as 10 feet above the floor. Wave antennas are designed differently than standard reader patch antennas, according to Don Taylor, NeWave’s business-development VP. Instead of radiating an RF beam in a single direction, like a traditional patch antenna, the Wave is designed to generate a uniform RF field around it. Taylor likens the Wave to a fluorescent light that illuminates a surrounding cylindrical space.
NeWave overcomes any RF fading or signal loss by installing a pair of Wave antennas inside each smartPORTAL, with one antenna inverted and cross-polarized with the other. This configuration, the company explains, also reduces the risk of RF signals spilling outside of the portal read area, which could happen with standard readers with patch antennas turned to high power in order to ensure that tags are read in challenging environments.
Johnson Controls has set up eight tagging facilities at the plants where the components originate, and 40 Zebra MC-9190-Z handheld readers are currently in use across those sites. To date, the company has tagged 876,000 containers. The tags are printed and encoded on Avery Dennison Monarch RFID printers, with the unique ID number encoded to each container’s tag linked to that container’s serial number.
As a container passes through a dock door, a smartPORTAL captures its tag ID, along with the time and the container’s direction and location at the time of the read.
An SLS Photo Eye sensor is mounted at the top of the smartPORTAL. The sensor, which SLS custom-built for this application, is powered by the reader, and is pointed at reflective tape on the dock door. Once the dock door is raised, the electric eye triggers the reader to activate the smartPORTAL’s RFID reader. This process eliminates signal bounce off the closed metal dock doors, Kelly explains, and has also reduced reader power consumption and unnecessary network traffic.
Staff members use handheld Zebra readers to perform weekly cycle counts at each facility. The handhelds run an application provided by SLS, known as COS Mobile, that allows users to plan shipments using container inventory data derived from a particular cycle count. A worker can also use the reader in Geiger counter mode to search for a specific container.
With the new system, Johnson Controls has designated lanes for receiving and shipping, through which containers can quickly pass and be captured electronically via the RFID portals. Surgere developed a software application that generates more than 20 different reports for the system, such as aging, inventory by dates and last-seen locations.
In addition, SLS provides what it calls smartEIT Listening Service—a software product developed to control and monitor RFID readers in the smartPORTALs. The service was customized to deliver tag and health events to the back-end software selected by Johnson Controls.
The technology has helped the company to identify regions and businesses that are misusing container assets. Its supply chain management teams are now able to recover those assets and put them back into the network. Kelly says he has been able to rebalance his container fleet and reduce the number of replacement containers that need to be ordered due to missing items. Johnson Controls can now cycle-count all of its containers and racks within minutes, as opposed to the several days it previously took before the RFID system was installed.
Johnson Controls recouped its investment in less than a year, Kelly says. The installation of the entire RFID-based solution was accomplished within just six months, he notes, and was more manageable for the company since the software is cloud-based and requires minimal IT involvement by Johnson Control’s own IT department. The system is maintained by SLS. “I don’t have anyone on my IT staff to ensure readers are working,” Kelly states. Instead, Johnson Controls turned the system’s management over to SLS and Surgere. “The core of this solution is our service providers,” he says, who provide him with data that his company can then determine how to use.
“If I have a distribution center sitting on containers for two days,” Kelly says, citing an example, “I can see that.” He can then contact the DC to find out the reason for the shipping delay. The software also knows that containers, after a certain number of days, should be returned from a customer, and can address the problem if they fail to come back by that date. “We’re changing the paradigm,” he states. “What we’re saying is, ‘This is an asset of Johnson Controls, and we want it back. We know where it is, and if you have it, we’re going to come looking for it.'”
“We’ve had a lot of large projects, but very few have been run as competently as this one,” says Bill Wappler, Surgere’s president. Kelly, he says, “is singularly responsible for what will be an explosion of RFID in the automotive industry.”
“RFID is pretty tricky for the automotive environment,” Wappler adds, due to the high level of metal and fast-moving goods in high volume. “We had to find a way to use the software, the reader hardware and the tags in a unified orchestra.” Once the system was proven and fully installed, he says, it was found to have a read accuracy rate of more than 99 percent.
Johnson Controls is now considering ways in which to expand its use of RFID technology. The company has begun testing the RFID-tagging of trim covers (the upper parts of seat covers, which are made of cloth or leather), and is using an Impinj reader at its assembly plant to verify what kind of trim cover is being installed on each seat. The trim pieces can also be identified after being received at a DC or at the seat assembly plant, in a closed box, via a handheld or portal reader. Moreover, Johnson Controls has begun attaching RFID tags to equipment in order to ensure that the correct mold or tool is being used properly for every project, and that it matches the seat order. Eventually, as more components are tagged, an individual at the inspection station will be able to use a handheld to confirm which trim items or other tagged components are built into a particular seat, and thereby make sure that no errors were made before it is shipped.
In addition, Johnson Controls is considering the use of RFID to identify the airbag components that it installs in some of the car seats it manufactures. If an RFID tag were attached to each airbag, and if the tag’s ID was linked to that item, a reader could later be used—in the event of an airbag recall—to identify any components that are not visible once they are built into a particular seat, so that no one would need to take the seat apart in order to identify those items.