ZF Friedrichshafen, a manufacturer of automotive transmissions and chassis, is employing radio frequency identification to improve the maintenance of motors that run its production machinery at its factory in Saarbruecken, Germany. After having a good experience using passive ultrahigh-frequency (UHF) tags to improve the management of parts at its Friedrichshafen plant (see RFID Helps ZF Speed Transmission Shipments), ZF began expanding the use of RFID across its company, which operates 119 production sites and reported sales of €12.6 billion ($16 billion) in 2007.
In Saarbruecken, where Friedrichshafen makes four-, five- and six-gear automatic transmissions for cars, the company has tagged 6,000 motors that run its production machinery and conveyor systems. These motors must be maintained and serviced at regular intervals—usually, every two to three months—to ensure that production equipment continues running.
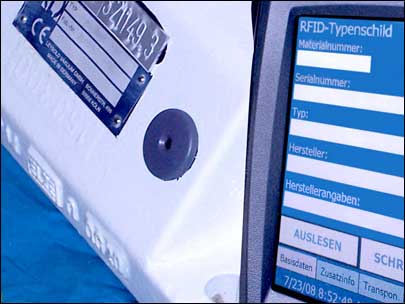
Before introducing RFID, ZF relied on metal tool identification plates that were bolted onto motors and could be read by employees. When workers needed to identify the correct motor to remove or repair, they had to visually match the number on the metal plate with that on the work order. Oil and dust, however, often made it difficult to read the numbers, says Jürgen Kusper, a project manager responsible for ZF Saarbruecken at Tricon Consulting, an RFID software and hardware provider located in Austria, and the systems integrator for this project.
Now, with RFID, workers utilize a handheld reader to interrogate the tags and confirm that the motors are, indeed, those in need of repair. They no longer need to worry that a tool’s identification number is not visible. Since production machines must always remain running, employees must switch out entire motors in order to make repairs or conduct inspections. The motor is removed from the production machine, a replacement is installed and the broken model is moved to the spare-parts warehouse and repair workshop. After the motor is repaired, a worker types in the number on the last paper repair order into the handheld reader, and the system writes the repair data to the tag.
The RFID system’s rollout began in mid 2008. During this rollout, every motor in the plant was fitted with a passive high-frequency (HF) RFID tag when it was moved to the spare-parts warehouse for routine or special maintenance. The tags contain NXP Semiconductors‘ 13.56 MHz Mifare chips that are also frequently used in transit applications. ZF chose passive HF RFID tags because it did not require long read ranges. Tags are located within a round, gray plastic housing bonded to the motor. The metal tool identification plates on which the company previously relied are mounted next to the RFID tags, in order to provide a visual backup.Workers utilize handheld interrogators from Psion Teklogix to encode each tag with basic data regarding the motor. With each repair, maintenance information or maintenance schedules are added to the motor’s RFID tag so workers can instantly know the maintenance history of a particular motor by interrogating its tag. The information is saved on the tags, which have a memory capacity of 1 kilobyte.
During the test phase, which lasted until the end of 2008, ZF examined the tags to make sure they would stand up to wear and tear from handling and cleaning in the harsh industrial environment. The company reports it has experienced no major problems.
Tricon supplied the hardware and software necessary for the project, and initially set up the application. ZF Saarbruecken continues to add motors to the RFID system by tagging them itself.
ZF Saarbruecken is presently considering an expansion of the application, Kusper says, since it helps reduce the overall costs of maintenance by decreasing the amount of time workers must search for the proper motor to repair, as well as the related maintenance histories. What’s more, if a particular motor is faulty upon purchase, its maintenance history could be used to back up warranty claims.
An expansion of the application would focus on the management of material flow and parts, Kusper adds, in which the movement of spare parts into and out of the warehouse would be tracked via radio frequency identification.