A Dutch company called WPS Horti Systems is providing growers a high-tech, RFID-based means of improving plant health and production, from seed to sale. Nearly five years ago, WPS worked with European auto-ID technology systems integrator Zetes to develop the Plant Order System, using RFID hardware from Tagsys. The company has been selling the system ever since, and a dozen of its customers have deployed it.
WPS’ Plant Order System is designed for use at greenhouses where plants are grown from seedlings to mature plants, as well as at large plant warehouses where the mature plants are stored and readied for shipment. At the greenhouses, growers place each potted plant into a larger plastic container with a Tagsys 10-TL passive 13.56 MHz transponder permanently attached to its base, encoded with a number to uniquely identify the plant inside.
Tagsys interrogators, mounted under the conveyor systems moving the plants from one growing area to the next, read the tag of each passing pot. At various stages of growth, the conveyors bring each plant to a mounted digital camera to be photographed. The Zetes software correlates each image with the container’s RFID tag number, then sends this data to a program that analyzes characteristics of the plant’s image—such as size, shape or color—and determines whether the plant is adequately healthy. Once the plant is grown and ready to ship, says Olivier Burah, Tagsys’ vice president for Europe, the Middle East and Asia (EMEA), it is removed from the container, which can then be reused for another potted plant.
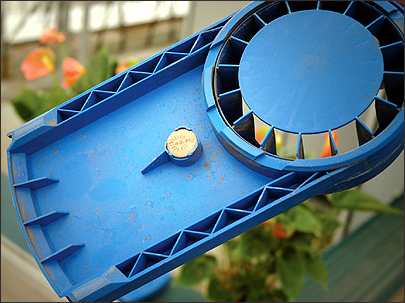
Aside from monitoring each plant’s health, the Plant Order System also enables growers to perform automated inventory counts and updates on each type of plant. On a daily basis, workers at the greenhouse tend to any ailing plants, applying fertilizer or taking whatever other measures they deem appropriate. Prior to implementing the Plant Order System, growers had to manually inspect all seedlings and plants in the greenhouse to find those requiring special care.
The mature plants are shipped to warehouses for storage and order preparation. There, each plant is transferred to the pot in which it will be sold. This pot is then placed on a small tray designed to keep it stable as it moves on a conveyor system into a storage area, and later to a shipping area. If the warehouse has deployed the Plant Order System, a Tagsys 10-TL tag is permanently attached to the base of each tray. As in the grow houses, readers are fixed beneath the conveyor system. In the warehouse, however, the data collected as the tagged trays move through the facility is used to route each plant to an appropriate storage area, or to the shipping area, based on directions the Zetes software receives from the warehouse’s ordering system.
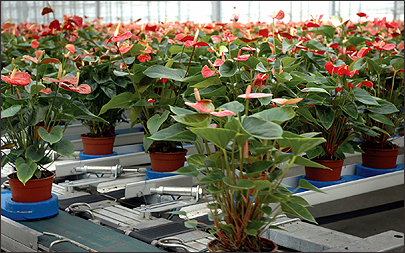
Some WPS customers have deployed the Plant Order System in facilities as large as 700,000 square meters, Tagsys claims, requiring the installation of up to 50 readers. Plant production, according to Tagsys, is a huge industry in Holland, with more than 1,500 growers of potted plants employing 1,000 hectares of greenhouse space. The plants are then sold to retailers at an average of €5 ($6.9) apiece, says Burah.
In addition to automating the inventorying and monitoring of plants, Burah adds, the platform provides WPS customers added visibility into their operations, enabling them to further increase productivity and reduce losses.