Energy technology company Schneider Electric has launched its first smart factory, located in Lexington, Ky., to enable the sharing of data and analytics across its departments using a variety of Internet of Things (IoT) technologies. The firm’s IoT-based EcoStruxure architecture captures and visualizes data from multiple technologies, including augmented reality, human machine interfaces, programmable logic controllers and connected technologies, such as passive HF RFID.
The Lexington facility’s EcoStruxure Advisor solution analyzes the information and shares it across the plant’s departments. According to the company, last year’s rollout of the system has driven digitalization across its existing installations. The firm claims this digitalization reduces production downtime, improves efficiency and decreases energy consumption.
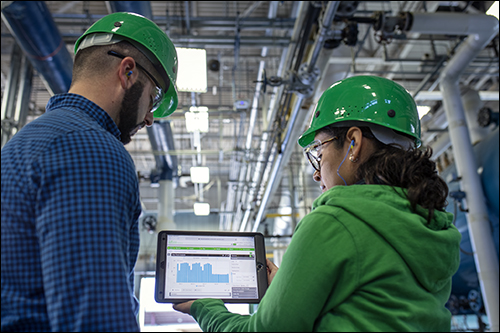
Some of the technologies, including the RFID system, have been in use for years, but Schneider Electric had completed the integration of the technologies into its EcoStruxure solution as of November 2018. The company is now sharing its system and experience with customers that are interested in creating their own smart-factory solutions.
The RFID portion of Schneider’s smart factory was initially deployed to automate the paint process for its products. Since being taken live in 2009, the RFID system, known as OsiSense, has eliminated 128 miles of daily forklift driving—which was required with the non-automated process—and has also reduced work-in-progress (WIP) inventory cost by $500,000, the firm reports. That enabled the company to gain a 33 percent return on its investment within less than a year, according to Mike Labhart, Schneider’s innovation leader for supply chain performance in North America. In fact, he says, the technology increased painting capacity and also enabled production automation such as robotic loading and unloading.
Now, the company has centralized the capture of RFID data with its other smart-factory systems in a single solution to improve data management. The facility’s central, cloud-based, digitized solution can display WIP and supply levels in the paint process, as well as other manufacturing operations. The Lexington factory is more than 60 years old, but it is a highly modern, automated operation that produces nearly 1.3 million load centers and about 800,000 safety switches annually.
With the advent of the EcoStruxure system, the company reports, the plant will serve not only as a production facility, but also as a showcase for customers and partners to learn how it is using IoT technology to make decisions that can improve profitability, asset-management performance and operational efficiency, while enabling a smarter, productive workforce. When the RFID technology was launched a decade ago, it was intended to track the movements of products on what was, at the time, its new automated monorail conveyor system. In fact, the RFID solution enabled the automated conveyor system to operate.
The company applied 13.56 MHz passive HF RFID tags, compliant with the ISO 15693 standard, to carriers on which racks holding components were attached as the parts were processed and painted. With the technology, the company was able to link each carrier with a particular product, and to read each carrier’s tag as it moved through zones in the production process. The material-handling conveyor system is complex; in fact, it moves product at high volume from 10 fabrication or load points through 10 assembly-line points, mostly related to painting. Altogether, Labhart says, the factory has approximately 900 conveyor tags attached to carriers where products are suspended as they undergo these processes.
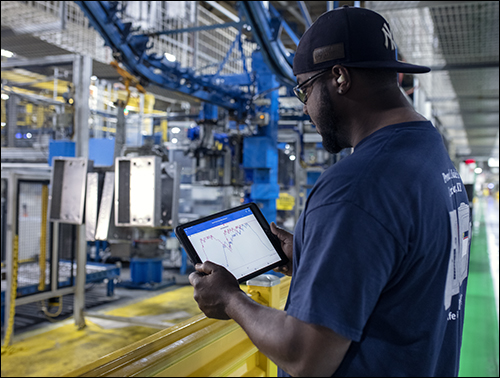
First, each new item in production is attached to a rack, which is then attached to a carrier. At that time, workers input five details into the system and that data is written to the RFID tag. Those details include whether the product is being tracked according to its origin or destination, its status (such as loaded, unloaded or painted), and its part, rack and carrier numbers.
There are 75 readers throughout the facility that capture tags reads as each item is processed. The tag passes within three inches of each reader, at which time data is read and routing is accomplished accordingly. When an item enters the paint section, the paint recipe for that product is written to the tag as well. Users can view in real time where each carrier tag was last read, thereby gaining data regarding WIP or potential reductions in materials and supplies. However, the data was previously captured at the edge, and not stored, so it couldn’t be analyzed later.
“The knowledge of what existed in the workflows was only known at certain points in the process,” Labhart says. There was no history available, and an individual needed to be in front of a computer in order to view WIP data. That was the case with other IoT-based systems as well. “Our facility is vertically integrated and fairly automated,” he explains. There are multiple proprietary systems in place at the plant, which has evolved throughout the years into what he refers to as pockets of data that might indicate which supplies and materials are available but cannot be automatically shared with other departments.
“We may have SQL [software] on one end and paper files on another end of the plant,” Labhart says, “while others used a legacy software system that didn’t integrate with other operations.” So for those on the plant floor or overseeing production, gathering data could prove to be a complex project. Visualization beyond the edge level has been a challenge, he notes, adding, “We had no history of that data. The data existed on the edge, in the moment, but then it was gone.” There was no ability to analyze the WIP data, or to correlate a given WIP count with another in order to evaluate performance, and also no ability to share the information.
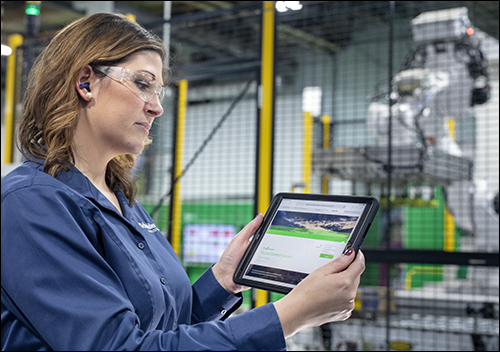
Since November 2018, however, the data captured and managed by the RFID system has been centralized. Thus, the information is now stored for analytics purposes, can be shared with other departments and can trigger alerts, such as notifying personnel that a supply level could be running low. With this next step, the material counts are now being captured and stored in the cloud, and supervisors receive push notifications if material levels reach an alert point or require action.
In 2009, the RFID system was integrated with the “power-and-freestyle conveyor system” by Thermo-Tron-X Inc., based in Sturgeon Bay, Wisc. This was the first installation of the product at the time, and Schneider worked with its own competency center to develop it. “We did a lot of product testing,” Labhart says, which included using a variety of tags and readers to capture each component’s unique tag ID, as well as written data, while the conveyors moved the tagged carriers at a speed of 60 feet a minute. The selected RFID tags and reader hardware were provided by the Schneider Electric Sensor Competency Center.
Schneider Electric tested the RFID solution on a simulated version of its conveyor system at its Competency Center in Dayton, Ohio. Since that time, the firm has continued to use the same technology, thought it has added racks, tags and readers. It has also begun deploying the technology on the last stages of its assembly lines, where goods are loaded onto pallets; each pallet comes with its own RFID tag.
The system’s benefits have improved since the EcoStruxure Advisor tools were taken live, Labhart reports. “We’ve seen a nearly 6 percent reduction in load center downtime,” he says, due to the company’s ability to react to notifications and events, such as low supply levels, before they can become critical. With the centralized data, he adds, “We better understand consumption of material in the different systems.”
The company is now working a complex modeling of the conveyor system. RFID data from the material movement, coupled with the descriptive analysis of Ecostruxure Advisor solutions, such as Aveva Insight, are enabling the company to predict and validate system performance before modifications are made.
The RFID system has been working effectively for the company for 10 years, Labhart says, and that hasn’t changed since it was first launched. “We have had no trouble with the RFID system. It is rock-solid,” he states, adding, “We had a large learning curve with the complexity of this kind of system when we started.” In fact, the firm deployed the system without shutting off production. “The coordination of logistics in the air, keeping production running, not interrupting the system—it’s been an eye-opening experience.”