A tobacco company and a Canadian convenience store chain are beta-testing ultrahigh-frequency (UHF) radio frequency identification-based smart-shelf technology to track the stock of goods on store shelves. The Smart Shelf system, provided by NeWave Sensor Solutions, enables the convenience stores to track when cartons are removed from shelves and, therefore, need to be replenished, or when the number of cartons removed at once is suspicious. By using the technology, the tobacco company and the retailer can each view how products are selling, as well as when stock levels are low, without placing an RFID tag on every product.
The UHF RFID system from NeWave deploys built-in shelf pushers (spring-based mechanics that push products toward the front of the shelf as one in front is removed). With RFID tags on those pushers, NeWave’s Nobel readers with Wave radiating antennas capture each tag’s ID number as the tags become visible to the system, every time another product is removed and the shelf pusher moves forward.
NeWave developed its Smart Shelf technology in 2016 as a solution to help retailers and brands view which items are in stock on store-front shelves, without requiring the manual labor involved for store personnel or brand representatives to visually count each stock-keeping unit (SKU) on the shelf. The difference between this solution and other RFID smart-shelf systems, says John Pellegrino, NeWave’s technical business development manager, is that users do not need to apply RFID tags to the products.
Traditionally, RFID-based smart-shelf systems include readers in or around shelves, which read the tag on each product placed on such a shelf. When a product is removed, the reader no longer reads its tag ID, and the software then determines that the item is going to be purchased and need to be replenished. However, tagging each product is still not cost-effective in some cases, NeWave explains, since each tag must be purchased, and the labor required to apply a tag to every product is an additional expense.
The Smart Shelf technology includes a single strip of RFID tags attached to each shelf pusher. When a pusher is positioned at the back of a shelf filled with products, a shield covers those items’ tags. Only a single shelf identifier tag is readable. NeWave’s software captures the tag ID associated with that shelf, and if no other tags attached to the pusher are visible, the cloud-based software interprets that data and displays, on a dashboard, that the specific SKU is fully stocked.
As an item is removed from the shelf, the pusher slides forward, exposing an additional RFID tag—one tag would typically represent one item removed. This data, captured by the reader, is updated to the software, which can also forward alerts indicating that a shelf needs to be replenished from the back store room, or reordered from suppliers. Personnel can receive that information in the software, or via e-mail or text message, and respond accordingly.
The system is also being used for theft prevention, Pellegrino reports. Thieves often sweep through a store, grabbing multiple high-value items from a shelf at a time, and then exit the building before the surveillance system or security personnel have time to respond. The Smart Shelf can detect if multiple items are removed from a shelf simultaneously, and thus trigger an alert to security personnel. That data can then be coupled with video surveillance for that part of the store, enabling security to view on camera who may have removed the items, as well as whether the intention appears to be theft. They can then intercept the individual before he or she reaches the exit.
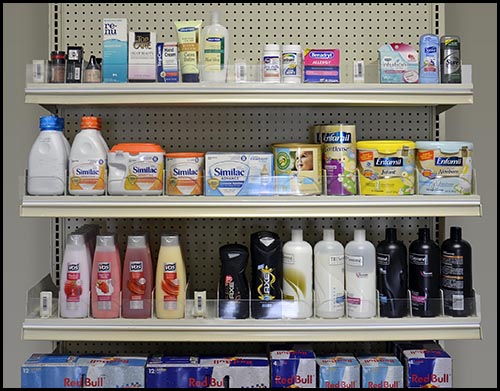
Typically, says Don Taylor, NeWave’s business-development VP, supermarket shelf sections measure 4 feet wide and accommodate five to seven shelves apiece. A single Nobel reader with 16 Wave antennas can provide RFID visibility to all shelves within four sections. “A great deal of research was done to determine the optimal RFID tag to enable our solution,” Taylor says, though he does not indicate which tags have been selected.
Since the proof-of-concept was completed in 2016 with the tobacco company and convenience stores, Taylor says, “We are now actually in the beta phase, the first step of which began in early April.” The retailer and tobacco company are currently evaluating the procedures to deploy the system across a large number of stores. Testing and data analysis will continue through the third quarter of this year.

In the meantime, another company based in Europe is expected to begin piloting the solution as well next month. NeWave demonstrated its new solution at RFID Journal LIVE! 2017, held earlier this month in Phoenix, Ariz.