Since installing radio frequency identification systems at its three distribution centers and attaching an EPC Gen 2 passive ultrahigh-frequency (UHF) RFID tag to every garment that it sells, Patrizia Pepe—an Italian fashion designer of clothing, shoes, bags and jewelry for men, women and children—has more than doubled the amount of products that each DC can handle per hour as they are received from factories or shipped to stores, according to Lorenzo Tazzi, the company’s information technology manager. Patrizia Pepe has also installed a video “totem” at four of its stores, in order to capture the tag ID numbers of garments carried by customers, and display product information.
Beginning in 2009, Patrizia Pepe—a fashion brand of Tessilform S.p.A.—began seeking a technology solution that would enable it to improve the visibility of the supply chain at its DCs located in the Italian cities of Capalle, Mezzana and Vaiano. The company sought to know when goods were accepted into the distribution centers from production sites, when the products moved throughout the DCs and when they were sent to stores. Patrizia Pepe moves approximately 2.5 million items per year, divided into two main seasons: fall-winter and spring-summer. The firm had tried scanning a bar-coded label attached to each garment every time products were received, moved or shipped, but scanning all bar codes was time-consuming, the company reports. When tracking goods via bar codes, warehouse workers were able to handle between 180 and 200 items per hour, according to Tazzi, adding that the firm wanted to improve this speed.
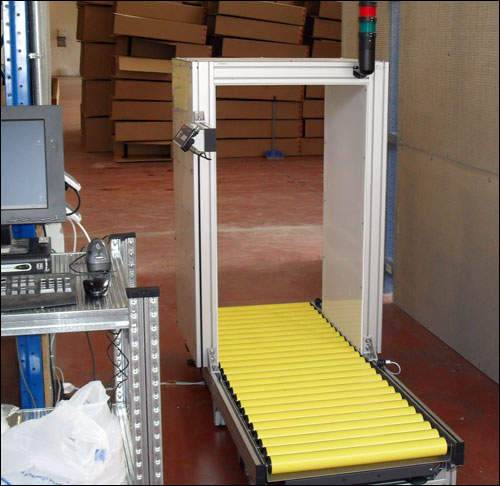
Therefore, in August 2009, Patrizia Pepe launched a pilot of RFID technology, under the guidance of researchers at the University of Florence. The five-month pilot took place at the company’s largest warehouse, in Mezzana, and included tagging 60,000 items as they were received at the DC, and then tracking them until they were shipped to stores.
Systems integrator Solos Identificazione e Protezione provided the integration of RFID data from hardware supplied by IDNova, which selected Impinj Speedway Revolution readers for the deployment. Patrizia Pepe, working with IDNova and Solos, decided to attach an RFID tag to the back of every item’s bar-coded brand label, explains Fabrizio Innocenti, IDNova’s managing director, so that the RFID tags could be encoded at the same time that the bar codes were printed. The partners used two types of RFID tags—one measuring 64 centimeters by 32 centimeters (25.2 inches by 12.6 inches) in size, the other 37 centimeters by 14 centimeters (14.6 inches by 5.5 inches)—each made with Impinj Monza 4D chips.
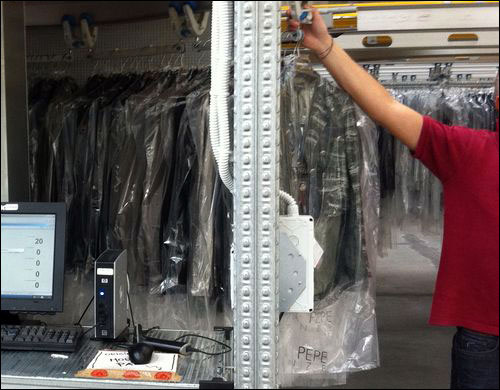
During the pilot, Patrizia Pepe sent bar-coded labels with pre-encoded RFID tags to the apparel manufacturers, which then placed a label on each item as it was packaged.
As boxes loaded with products were received at the warehouse, each carton passed through one of seven RFID tunnel portals. Each tunnel contained an Impinj Speedway Revolution R420 reader wired to four antennas designed by IDNova, and came with a built-in scale to weigh every box as it was placed on the conveyor. The tunnel readers were utilized for both shipping and receiving. When tag ID numbers were read, that data was forwarded to Patrizia Pepe’s back-end software, custom-designed by the company, to link each ID number to that particular product’s stock-keeping unit (SKU), as well as store that ID with the action that had just occurred, such as receiving or shipping.
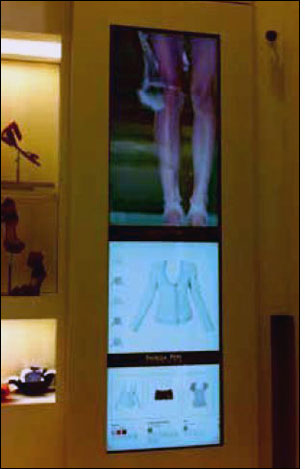
Additionally, IDNova built custom portals, each equipped with four IDNova antennas, designed to accommodate hanging rack items moving into or out of the DC, as well as the changed location within the warehouse. As hanging items were moved through the portals, the ID numbers were interrogated and transmitted to the Patrizia Pepe software, which determined the direction in which those goods were moving (for example, into or out of the warehouse), and thus, which action was occurring.
With the new, RFID-based system installed at all three distribution centers, the staff can now handle 380 to 400 items per hour, Tazzi says. When shipping goods to retailers, the DC could process only 140 products per hour, he notes, but it is now able to ship out 330. The RFID system has also increased accuracy, according to the company, thereby ensuring that the incorrect products are not shipped to retailers, and that out-of-stocks are less likely to occur due to inaccurate inventory counts.
Since the pilot’s conclusion, Patrizia Pepe has installed the solution at its three DCs, encouraging its suppliers to apply tags to their products. To date, Tazzi reports, about 2.2 million products have been tagged.
In 2011, the company also installed informational video totems near the dressing room entrance at each of four stores—located in the Italian cities of Rome, Florence and Milan, and in Moscow, Russia. In each case, when a customer carries clothing past a totem, a Speedway Revolution R420 interrogator reads the garment’s RFID tags. Two LCD touch screens then display information about that product, play videos of models wearing the clothing and offer advice regarding other items or accessories that might combine well with that garment. Similar reading stations are slated to be installed next month at a Patrizia Pepe store in Mexico City.