RFID Journal LIVE! 2023 will feature end-user companies discussing RFID’s use in various industries, as well as exhibitors offering tagging solutions for multiple applications. To learn more, visit the event’s website.
Dutch food company Gourmet has deployed a radio frequency identification (RFID) solution to ensure visibility into its vegetable products by tracking the boxes in which they are dried in storage rooms and then accessed for order fulfillment. The company is using the ATLAS forklift solution, employing passive UHF RFID technology from Aucxis. The solution was taken live in January 2023 at the company’s Grootebroek (Noord Holland) facility.
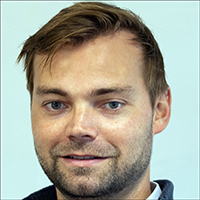
Lauran D’hanis
Gourmet was launched by the Broersen family in the Netherlands to grow allium plant-based products. The company provides the cultivation, selection, packaging and distribution of onions, shallots and garlic, which are then sold to seed companies. It also provides shallot varieties aimed at the consumer market.
After harvesting, Gourmet’s products are sorted into categories and stored in large wooden bins where they are dried. The company packages the goods according to the needs of retailers, and it distributes those packaged products to them as needed. It sorts products by putting specific vegetables into wooden storage boxes based on their quality, size and weight. The crates are then moved by forklifts to storage rooms, where the products dry before being sold. They are later accessed and packaged for shipment to customers.
Traditionally, the company managed the location and status of these goods by scanning barcodes applied to box labels, according to Lauran D’hanis, Aucxis’s account manager and business consultant. “A lot number was assigned to each storage box by means of a barcode label,” he says, “and the boxes were tracked throughout the different warehouse locations using barcode scanners.” Gourmet sought a way to better identify and manage its goods, however.
RFID-Enabled Forklifts
“The manual registration was the biggest problem,” says Jerry Posthumus, Gourmet’s operations manager. “If someone forgot to scan, there was an error in the system.” Manually scanning each barcode proved to be time-consuming, Posthumus explains, and the company needed a system that would make it possible to accomplish the same function automatically. He says Gourmet looked into RFID to gain “total control and track and trace over the stock and product handling,” and to “eliminate human error as much as possible.” The company thus approached technology firm Aucxis.
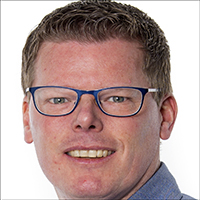
Jerry Posthumus
Because the boxes were transported to different locations within the storage facility or sortation area by forklift, Aucxis opted to deploy a mobile system centered around those vehicles. “This is a very flexible solution,” D’hanis says, adding that for Gourmet, “It was important to scan the boxes when they are picked up by a forklift and dropped off.” Standard RFID reader gates installed throughout a facility can detect when boxes have entered or left a zone, but they cannot identify details such as the aisle in which they were stacked.
Therefore, Aucxis worked with Gourmet to develop a system leveraging forklift readers, which was first tested in 2020. Based on the results, D’hanis reports, Gourmet began tagging its storage boxes in 2021. The solution consists of two RFID tags on each box. The ruggedized UHF tags are screwed into place, one on each side of the box, in such a way that they aren’t likely to be knocked loose. Each tag is encoded with a unique ID number.
Tags are also installed in each storage row within the warehouse, cut into spaces in the floor. RFID readers from Impinj are built into the forklifts to read tags as workers go about their tasks of transferring boxed items. To date, the company says it has tagged approximately 38,000 boxes. Twenty-two forklifts have an RFID reader installed to date, each with four antennas to ensure reading at 360 degrees.
Tracking Storage, Access and Packaging
Each time boxes are moved, readers capture tag ID numbers and transmit that data to a server, where Aucxis’s Hertz middleware filters and processes the data and then transmits it to gourmet’s warehouse-management software. The boxes are reusable. Typically, when a box is emptied, it can be delivered to the receiving area, where it can be filled with a specific product type, size and quality, such as large onions. That data is then linked in the software to the box tag’s unique ID.
Once the box is filled, a forklift delivers it to the assigned storage area. When the vehicle picks up the box, the reader captures its tag ID. As it then transports the box down warehouse aisles, the floor tags are read and their data is transmitted back to the management software via Wi-Fi, linking that forklift to each specific location. After the box is placed in storage, the vehicle leaves the area. The software detects that the box’s tag is no longer being read, and thus that it has been deposited. Its location is updated in the software, based on the most recent floor tag location.
When goods are required to fill a customer order, forklift drivers use the software data to locate the appropriate wooden box, drive to that location and pick it up. The vehicle reads the tag ID, and the software confirms that the proper product is being accessed. The box is then delivered to the packaging area, where the goods are removed for packaging. If the box is entirely emptied of its contents, the driver uses the software to input a prompt indicating the crate is empty and can be reused for new products.
With the RFID tag read data, Gourmet not only has an automated update of the status and location of its stock, but it also knows the history of each box’s routings, as well as when and how often products were accessed and packaged for shipping. “This reliable data and insight into the internal cycle of the products,” D’hanis says, “leads to process optimization and quality improvement,” by ensuring the right product is sent to fill each order, and that goods are used while they are fresh. In the future, the company indicates, the RFID system could be expanded to include packaged goods as well.
Key Takeaways:
- Gourmet is managing the movements of onions, shallots and garlic via an RFID reader mounted on each of its forklifts, with tags applied to their containers.
- With the technology, the company ensures its products are accounted for, and that they are used to fulfill orders properly in a timely fashion.