STMicroelectronics and Feig Electronic have teamed up to offer a Near Field Communication (NFC) system that enables wireless settings adjustment of electronics. The solution relies on ST’s ST25DV Dynamic NFC/RFID Tags embedded in electronic devices, as well as Feig’s ID LR2500 HF long-range reader and antenna.
With the solution, manufacturers can update settings batches on products as they travel along a conveyor belt, while consumers and maintenance personnel can use the same tags to access data and update firmware via an NFC-enabled smartphone. Traditionally, manufacturers have had to use manual settings adjustments on their assembly lines to customize equipment, according to Tania Guidet, the marketing manager of STMicroelectronics’ ST25 products. That could mean adjusting for a product’s customer destinations, for instance, which can be a time-consuming process for manufacturers.
The NFC-based system, according to the two companies, provides a single solution that can be deployed at multiple stages, such as customizing assembly lines, enhancing the customer experience, and providing maintenance and repair. The system also allows inventory tracking for stock management and logistics at a relatively long read range via NFC, based on engineering provided by Feig Electronic. The solution is available now.
For companies that have used UHF RFID technology for inventory tracking, there are some limitations built into the technology. For instance, it has usually been necessary to read tags at a distance, but because UHF RFID readers are not built into smartphones, consumer would not be able to interact with the tags after purchasing products.
The NFC solution enables multiple functionalities with a single tag due to its long-read range, ST and Feig report. “The purpose here is to combine track-and-trace applications (with a FEIG reader) and consumer interaction (with NFC smartphones) with a single ST25DV RF interface and antenna,” Guidet explains. The NFC Dynamic Tag provides a link between RFID transmissions and a microcontroller unit (MCU) embedded in the device, she says.
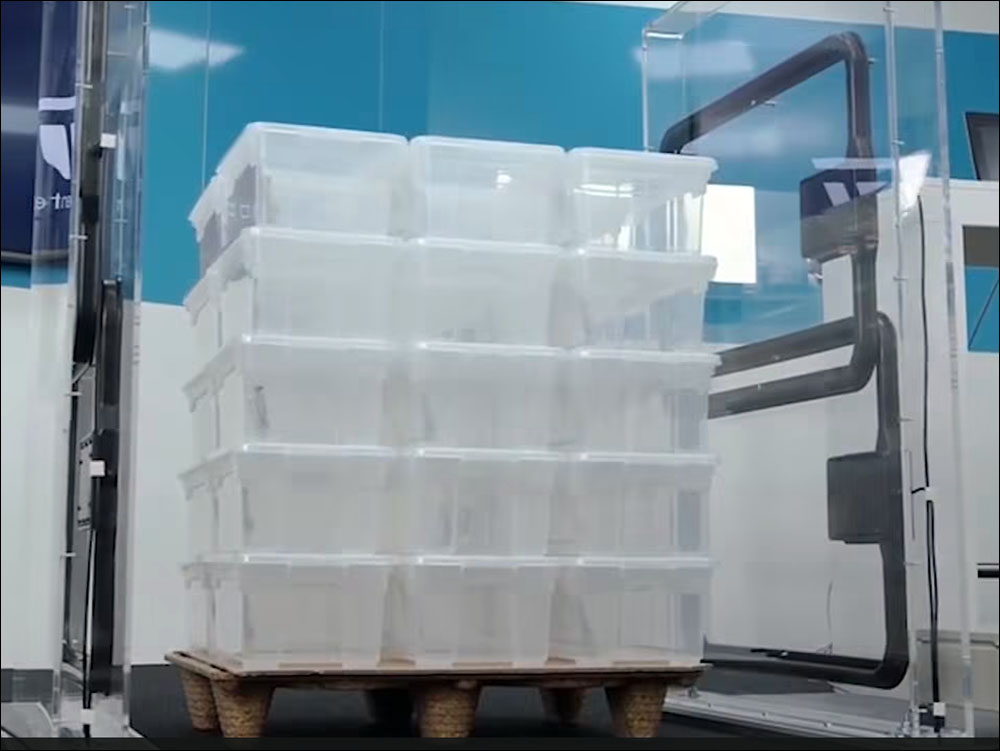
Manufacturers can program multiple products on a single pallet simultaneously.
When goods are shipped from a factory, some data may need to be customized. For instance, if a washing machine were being sent to Germany, the language in the machine’s settings could be updated to German as the goods passed through the production line. The manufacturer would change the language settings in its software, which could be connected to a reader via a USB cable. The Feig reader would then command all tags within a specific batch to be updated with the settings change. The tags built into the devices would receive that transmission at a long read range, using HF RFID compliant with the ISO 15693 and NFC Forum Type 5 standards, and the MCU would then make the necessary adjustments.
The system also works for consumers using a product, such as a printer, a coffee machine or surveillance system hardware. Such devices come with an MCU to control the modes and interfaces of their internal equipment. If the device is not operating, users can access data about the failure. This information can include the model number and error code, which they can view on a smartphone, and the app could enable them to begin troubleshooting, as well as update the firmware on the machine via their phone.
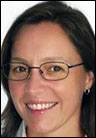
Tania Guidet
In addition, the solution can be used to access information about how a device has been utilized. This data can help service representatives diagnose and repair that device. For example, washing machine cycles can be captured by a smartphone via NFC or HF RFID, after which that information can then help workers understand how the machine has been used.
The ST25DV-I2C Dynamic Tag is not a new product. In fact, Guidet says, the series was introduced in 2016 and has been extensively used in multiple industrial areas, as well as in consumer electronics applications (see IoTize Wins NFC Forum Innovation Award to read about one such use). “The interest here is really to deploy an existing solution—NFC for smart factory and smart maintenance—at a wider scale,” she states, “by leveraging the power of Feig’s solution and increasing the read range.” This long-range functionality enables manufacturer to program multiple products, such as several pieces of equipment on a pallet, simultaneously.
In order to achieve the long range, Feig built a system with a 1-meter square (3.3-foot square) read area, with a homogeneous antenna field to communicate with the ST25DV tags, according to Andreas Löw, Feig Electronic’s marketing and corporate communication manager. “For this, we used our high-performance HF RFID readers,” he says. The system thus includes Feig’s ID LR2500 HF long-range reader, a power splitter, a four-channel multiplexer and four ID ANT800/600 HF long-range antennas.
The programming speed depends on the volume of tags within range of the reader. “The more tags that have to be programmed,” Löw explains, “the more time that is needed.” The tags’ position and the distance between them affects read rates as well. The theoretical maximum is approximately 1,000 tags, he notes, though that would be variable, based on each application’s conditions.
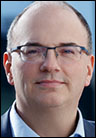
Andreas Löw
Two features of the solution shorten processing time, Löw reports: the writing process and power usage. Regarding the former, the system is optimized to write to multiple tags at the same time. And for the latter, the power splitter halves the multiplexers’ switch frequencies by connecting two antennas to a common detection area.
During early testing, Löw says, Feig managed the data using its variable test and configuration tool, known as ISOStart+. The company also offers several standard software developer kits for customized application software, which enable an individual adjustment and optimization of the data sequence. Several companies that have asked to remain unnamed are currently in the process of deploying the solution at their facilities. The two companies predict the benefits will be felt by manufacturers of both industrial and consumer products.
When it comes to enabling settings wirelessly as products are manufactured, Guidet says, “The introduction of NFC is bringing a lot of simplification and flexibility to the manufacturing process.” Potential users, she adds, include any companies that produce electronic components which need to be programmed individually, such as smart meters and LED drivers, as well as consumer products such as appliances, printers or digital electronics. Smart meters, for instance, require settings with different firmware functions, depending on the varied regulations in European countries. In other cases, devices require different configurations in terms of language, interfaces and performance parameters.
For consumer goods manufacturers, Löw reports, the benefit is in attaining a more efficient personalization process. Due to the NFC application, he adds, the time-consuming process of taking products out of their boxes, one by one, to personalize or program them is no longer necessary. Now, product personalization takes place automatically as pallets of products are moved through the RFID-enabled gate.