Orthopedic implant company Medacta USA is piloting an RFID-enabled solution to track its loaner kits when they are provided to hospitals. Each kit comes in the form of a case filled with Medacta USA implant products. The system, supplied by inventory-management technology firm Terso Solutions, allows Medacta USA to receive daily updates regarding which products are inside each case, as well as each time the case is opened. In this way, users can view which implants remain in a particular kit, and where that case is located. That information is intended to help the company prevent errors, investigate losses and, if Medacta USA adopts the system permanently, automate the billing process.
Since Medacta USA began testing the technology, says Shawn McIntyre, the company’s director of operations, it has been able to more accurately and efficiently replenish kits with replacement items—even when cases are still in the field—since Medacta USA now knows which items were removed from the kit and not returned. It also knows when and where those actions occurred.
Headquartered in Chicago, Medacta USA is the U.S. division of Medacta International, a manufacturer of orthopedic implants, as well as neuro-surgical systems and instrumentation. The company ships its kits—each filled with implants for a specific type of surgery, such as a hip replacement—to hospitals prior to patient procedures. A Medacta USA sales representative is present during such surgeries, to provide surgeons and hospital personnel with technical assistance.
Traditionally, as products are removed from the kit, the sales representative manually records those actions, after which Medacta USA bills the hospital accordingly. However, implant products can end up missing, and are sometimes lost by a carrier in transit, delivered to the wrong facility or misplaced at the hospital. What’s more, the act of replenishing a kit can be inefficient, since the company may not know which items need to be restocked until that kit arrives back at its warehouse. Medacta USA began working with Terso this year, McIntyre says, to test how well RFID technology could make these processes more visible.
Terso Solutions’ RFID Mobile Case Automated Inventory Management Solution consists of Terso’s Mobile Case, comprising a Pelican hard-sided carrying case with a built-in Impinj RS500 RFID reader, a 4G cellular radio and a microprocessor to store read data and forward that information to Terso’s Jetstream cloud-based software. Terso developed the technology in 2014 and 2015 so that businesses that send kits of high-value medical devices to hospitals could gain visibility into those kits’ locations and contents (see Terso Makes a Case for Mobile Tracking of Medical Devices).
Medacta USA began testing the technology on two of its implant kits approximately two months ago, and intends to continue testing throughout the remainder of this year. If the technology continues to work well, McIntyre says, his company may opt to incorporate the RFID technology into all of the loaner kits it provides to health-care organizations for use during surgery. To date, he notes, the solution seems to be helping his firm determine what is in each case and where it is located at any given time, and thereby identify which products may need to be replenished—and, in the event that an item ends up missing, when and where it may have been removed from the case.
“One thing [our customers] didn’t have was full exposure of the status of each kit,” says John Kuehl, Terso’s hardware product manager. Companies like Medacta USA often need to replenish a kit quickly, he explains, either at the implant firm’s distribution center (when returned by a customer), or in the field (while at a hospital or in the hands of a sales rep).
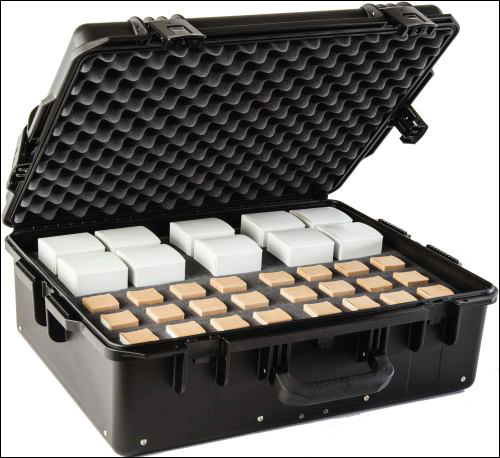
An Avery Dennison AD-321 RFID tag is attached to each implant product’s packaging, so that as it is placed inside the kit, the case’s reader can capture every tag’s unique ID number, which is linked to that product’s description and serial number in the Jetstream software. Each time the case is opened and then closed, the reader is prompted to interrogate the tags, and to then transmit the ID numbers to the Jetstream software via a cellular connection. In addition, once each evening, the case’s reader automatically interrogates the tags again and forwards that data to the software, thereby updating the inventory status—even if the case may not have been opened that day.
Medacta USA is currently testing two Terso cases filled with implants for hip surgeries. Each case has traveled to a customer and back 10 to 15 times, McIntyre says, and has functioned well. The only problem that has occurred, he reports, is periodic loss of transmission when the case is at a location—in a hospital basement, for instance—in which cellular coverage is unreliable.
“It’s been interesting to see” the data resulting from the tag reads, McIntyre says. For instance, one sales rep had a habit of removing all products from a case and placing them into another container when it arrived at the hospital. That action can now be viewed immediately, since all tag reads would cease.
Another advantage of the RFID Mobile Case, according to Joe Pleshek, Terso Solutions’ CEO, is that that the unit contains built-in memory for storing inventory transactions, even when it is not connected to the cellular network. “Once connection is re-established,” he states, “the queue is pushed to our Jetstream cloud solution, so that no transactions are missed.”
McIntyre says he hopes to begin expanding the system’s use to other carrying cases his company utilizes. Doing so, however, would require that the RFID technology be adapted to a variety of case sizes. “I’m always looking at how technology can drive efficiency and accuracy,” he says.
With the RFID-enabled cases, McIntyre says, he can more accurately send replenishment items for a kit at a hospital, since the Terso’s Jetstream cloud-based software automatically transmits updated inventory data to Medacta USA on a daily basis—whereas, with the manual method, the company may not know what was removed until the kit returns to the DC. In the future, McIntyre hopes to use the technology to speed up the billing process. He envisions providing sales reps with an Android- and iOS-based app that would allow them to bill for an item while they were out in the field, at the same time that the case would provide details regarding what had been removed for a surgery.
Medacta USA was the first company to begin piloting the RFID Mobile Case, Kuehl says, but several others have launched pilots during the past few months. The system can be used not only to gain efficiency in real time, Pleshek notes, but also to support business analytics. By viewing how often items are used, as well as when and where this occurs, companies can better manage their inventory of products that are placed into the cases.
Terso continues to improve on the technology as well, Kuehl says. For instance, while early versions of the case required that the battery periodically be removed for recharging, the current versions now accommodate being plugged directly into an outlet. According to Pleshek, a battery can operate for six to eight weeks with one or two case openings each day, before it needs to be recharged.