Managing and inspecting heavy equipment in Chinese oil fields has posed a challenge for oilfield operators, which often contain hundreds of thousands of assets on a single site. That task grew more challenging in 2013 when China’s State Administration of Work Safety (SAWS) issued new standards mandating that companies maintain records of their assets’ maintenance history, with the goal of reducing the number of accidents.
In response, one of China’s leading oil exploration and production companies has adopted a radio frequency identification solution. The firm has already affixed Xerafy tags to 30,000 portable transformers, and has issued ATID handheld RFID readers to field workers. The company also plans to begin tagging other items, such as heavy machinery, pipes and valves.
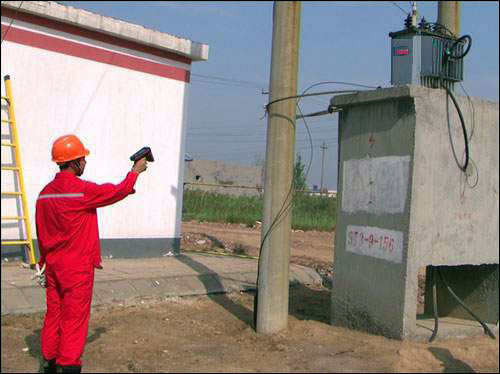
In seeking a technological solution, the oil company wanted not only to comply with SAWS’ requirements, but also to increase its own efficiency. The firm used bar-coded labels to track its items, which inspectors scanned. They then manually filled out paper inspection reports that had to be taken back to an office for inputting. Such a system allowed for mistakes, or for the loss of data between the field and the office database. In addition, scanning some equipment, such as high-pressure boilers, can be dangerous for employees.
Not only could RFID technology make the process of collecting inspection data more efficient and error-free, but the improved access to records could ensure that equipment is inspected and maintained more frequently. This, in turn, could lead to better operating equipment, the company (which has asked to remain unnamed) reported to VictorySoft Co. Ltd., a Chinese oil industry systems integrator that provided the RFID solution.
By deploying RFID, the oil company could also locate assets that might be difficult to find in the large oil field via manual searches and bar-code scans.
The company faced several challenges when seeking an RFID solution. For one thing, in some cases the tags would need to be affixed to transformers located eight or more feet above the ground. Therefore, the system needed to provide a long read range. What’s more, the highly metallic environment had the potential to interfere with RF signals transmitted by the tags and readers, while exposure to weather, temperatures ranging from -30 degrees to +60 degrees Celsius (-22 degrees to +140 degrees Fahrenheit) and damaging chemicals all made highly ruggedized tags a necessity. The oilfield operator had tried several passive RFID tags and readers on its own, but had found the performance not to be as reliable as it needed.
When the company approached VictorySoft, the IT technology firm tested EPC ultrahigh-frequency (UHF) RFID tags from five different companies, according to Xu Haiting, VictorySoft’s general manager of technical development. The tags that performed the best, Xu says, were Xerafy Cargo Trak tags, which could be affixed to assets by means of adhesive, rivets or welding. The oil company tested the tags on its site, providing inspectors and other field workers with ATID AT870 handheld RFID readers with which to interrogate the tags while searching for specific equipment. The oil company tagged a few items before determining that the technology worked, and then began applying the tags to more than 30,000 transformers used to provide dependable electricity distribution to the oil field. The oil firm chose to tag transformers first, due to their need for regular inspections and calibration in order to ensure their proper operation.
While searching for an item, a worker walks around the oil field, during which the handheld receives the unique ID transmitted by each tag from as far away as 12 meters (39 feet). The handheld then employs a Wi-Fi connection to forward each ID to VictorySoft software hosted on the oil company’s back-end server, and to access information regarding the tagged item, including a description and its inspection and maintenance history. If performing an inspection or calibration, the worker can then input the time and the type of work being carried out, and that information is stored along with the unique ID number encoded to the tag, thereby creating a permanent record that company management can view and, if necessary, share with government inspectors.
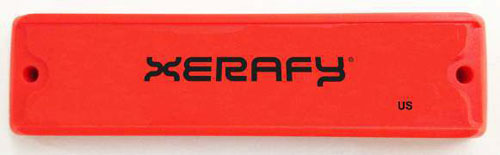
“The system software keeps records for installation date, calibration settings, date of service, maintenance history and other important information,” Xu says. “The software makes it easier for site managers to know the location and operating status of transformers, to ensure they are inspected and calibrated on time.”
Since its installation in 2013, the system has made it possible for inspectors to conduct their work more quickly, without the need to search as long for transformers, or to use paper and pen. “Workers can perform their job more effectively,” Xu states, “and save time by not having to write down the maintenance history.”
According to Xu, the oil company plans to expand the RFID system’s use to hundreds of categories of assets on its oil field. However, he says, specific information regarding how many tags will be used—or when—is not yet available.