Meyers has invested in equipment to create branded labels with built-in technology to simplify the adoption of RFID for brands without requiring multiple processes or vendors.
Consumer packaged goods (CPG) companies adopting RFID technology face a few challenges. They can purchase basic UHF RFID tags – often a plain white sticker – that they apply to their product packaging or price labels. That means, however, that the look of the product is compromised. The other option is often a custom-made label printed with their branding, including RFID functionality. The first option is relatively low cost (about 5 cents), while the customized label might cost considerably more.
Meyers, a label and packaging printer, has offered RFID technology options since 2005. However, it has now developed an RFID label printing system that can embed RFID into a company’s labels as they are printed. The company says that that makes RFID more affordable while not requiring an additional RFID tag.
The company acquired a single, eight-station label production machine in August for printing and encoding RFID-enabled, branded labels for its customers. Its initial customers are tire makers, building RFID into their retail labels. However, the printing company is also targeting makers of consumer products and apparel brands.
Addressing a New Demand for RFID
Meyers already creates packaging, labels, and retail displays for companies such as Frito-Lay, Estee Lauder, and Saucony. RFID labels (with UHF RFID chip and antenna and a unique ID encoded) represent about 7 percent of the products they sell. Recently, however, demand for RFID has been rising.
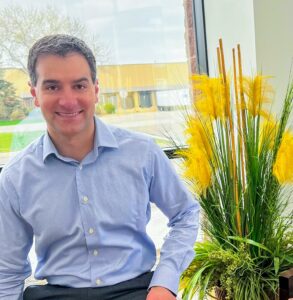
Chris Dillon, CEO, Meyers
Some of Meyers’ early RFID-based offerings included UHF tags for home video company Blockbuster, attached to DVDs to enable them to be uniquely identified as they were rented from kiosks. Over the years, Meyers has witnessed stops and starts in RFID technology adoption. However, the latest drive to deploy RFID in products is showing a new kind of momentum, says Chris Dillon, the company’s CEO.
Along with the new demand for RFID technology, the CPG label company has heard a common complaint from brands adopting RFID labels. Simply applying an RFID label to a product interferes with the aesthetics of the product packaging, while efforts to embed the technology are too costly.
Dillon says the company’s latest capacity for making all-in-one labels is part of its vision for smart packaging. He argues that using RFID, not just on labels of various product packages, will enable more streamlined delivery of goods and improve customer satisfaction.
All-in-One RFID Printing Equipment
The goal is to prevent companies from buying a separate label that must be attached to existing ones, creating a particular step and potentially disrupting the title or package appearance. “Meyers is giving brands the option to keep a beautiful label without an RFID label stuck right over the top,” Dillon says.
Meyers employs a team of technicians and engineers who have been working in the RFID space and were instrumental in transitioning the company to the flexographic printing press, says Dillon. The eight-station Mark Andy press can accomplish four- or eight-color processes, as well as spot colors and varnishes, with dye cutting in line and RFID insertion in line. The press has a built-in Tamarack RFID module for the inlay unwinding, converting, and application.
The new machines print and encode the RFID-enabled product with a single process. The labels have an RFID inlay – with a UHF chip and antenna – as the center layer. Around it is a layer of adhesive and a third exterior layer, on which a company’s logo and other information can be printed.
Typical tags are ordered in about one million volumes, but the order could also be considerably smaller. Many companies seek RFID in their labels for products destined for retailers, such as Walmart, while they intend to send essential labeled products to retailers not yet using RFID. Meyers can accommodate both requirements, Dillon says.
In fact, a single production run can include separate SKUs based on RFID-enabled, and non-RFID labels. “On our new line we could run a batch of labels with RFID tags and then we could basically continue running the press and just stop putting RFID tags in,” Dillon says. The different labels could then be organized into batches as separate lots.
Companies can request either dry tags without the adhesive or wet tags to be affixed to a product. Dry tags are cheaper, which the company has been making in greater volume.
Meyers also offers digital presses for more minor, specialty products, in which case a company with a shorter run of labels could have those labels digitally printed and then put through the die cutting and insertion of the RFID tag in the Mark Andy machine.
Meyers feels it provides a service that few competitors offer. Many label printers produce blank white tags. In contrast, others create one- or two-color RFID labels or print the labels on a flexographic press and then move that label to a second line where the RFID tag insertion is provided.
Label manufacturing takes place in Meyers’ Minneapolis facility for customers throughout North America. Dillon says the first customers tend to be based in Michigan where tires are being manufactured, and Meyers is providing the RFID labels that are applied to those tires before they are sent to the retail site. The tag then enables tire management through the supply chain and store.
Due to the lowering cost of RFID and demand from retailers, Meyers anticipates the technology to represent an increasing percentage of its sales. Dillon adds that RFID is an example of a challenge to the label industry that Meyers is well suited for. “We thrive when there’s something a little bit challenging… we’ve got a long history of getting involved with complex, complicated projects that others might shy away from.”
Key Takeaways:
- Increased demand for RFID tagging to meet retailer mandates has led Meyers to adopt a system in which a label can be printed, dye cut, with an RFID tag inserted inside, by a single machine.
- Thus far, tire companies are using the solution, while Meyers is also speaking with consumer product goods companies to use the same tag production process.