Italian coffee machine company Gruppo Cimbali offers connected products that leverage Wi-Fi, Bluetooth and LAN connectivity to enable its coffee grinders to communicate with espresso or drip machines, and the machines to transmit data to the cloud. Now, the company has teamed with Altair to employ digital-twin technology for its products, which Gruppo Cimbali anticipates will not only benefit its product development but also enhance customers’ use of the finished product.
With the digital-twin approach, known as Altair Activate, the coffee equipment company can employ Internet of Things (IoT) data from its products to develop and test new offerings more efficiently and faster than would be possible using the traditional method of creating prototypes for testing in a laboratory. Gruppo Cimbali is currently in the process of developing a product that will be released in the fourth quarter of this year, using the digital-twin technology. Although the company is not yet releasing the details of the new product, it has indicated that it plans to provide further functionality for users, such as identifying any need for maintenance or repair.
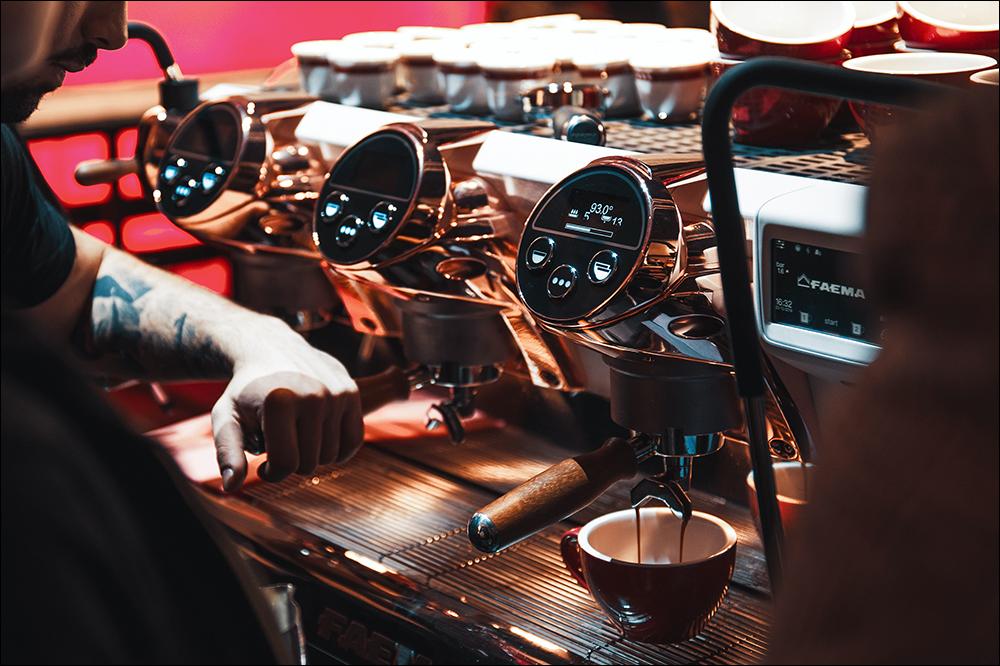
Digital-twin technology can combine process data and simulation to increase product performance and efficiency, as demonstrated here with Faema’s E71e coffee machine.
Ultimately, Gruppo Cimbali intends to provide a digital twin for every product sold to customers, so that information collected from the machine can be used to improve operation and enable new features. Initially, however, the focus will be on new product development, says Maurizio Tursini, Gruppo Cimbali’s chief products and technologies officer. The company offers professional coffee machines worldwide, he says, which are used in restaurants and businesses. It develops and manufactures the coffee machines and grinders at three facilities in Italy, as well as a fourth in the United States.
Gruppo Cimbali was founded in 1912, Tursini reports, and in 2000 it became one of the first coffee manufacturers to offer telemetry-enabled products. The machines can transmit data between each other, as well as to a cloud-based server. The company has built its products with Wi-Fi and Bluetooth wireless functionality for approximately eight years. Users can control the machines to change the perimeters and settings via a web portal. In that way, they can make changes remotely—across a chain of cafés, for instance. The machines also come with GPS-based geolocation functionality.
For machine-to-machine wireless connectivity, the grinders can utilize Bluetooth connections to transmit data to a coffee machine. As users grind their coffee, the grinder forwards data to enable the espresso or coffee machine to adjust accordingly. The company’s espresso machines can automatically track and share information about each drink crafted, along with offering insights about drink quality to improve the machines’ daily management. That information can then benefit both the users and Gruppo Cimbali.
“We try to satisfy the needs of these companies with this telemetry solution so that our clients—and we—are able to understand the use of machines,” Tursini says. That includes not only how the machines operate, but also where they are deployed and the amount of coffee being made. Gruppo Cimbali expects Altair’s digital-twin technology to take the company’s connected coffee machines to the next level, he adds.
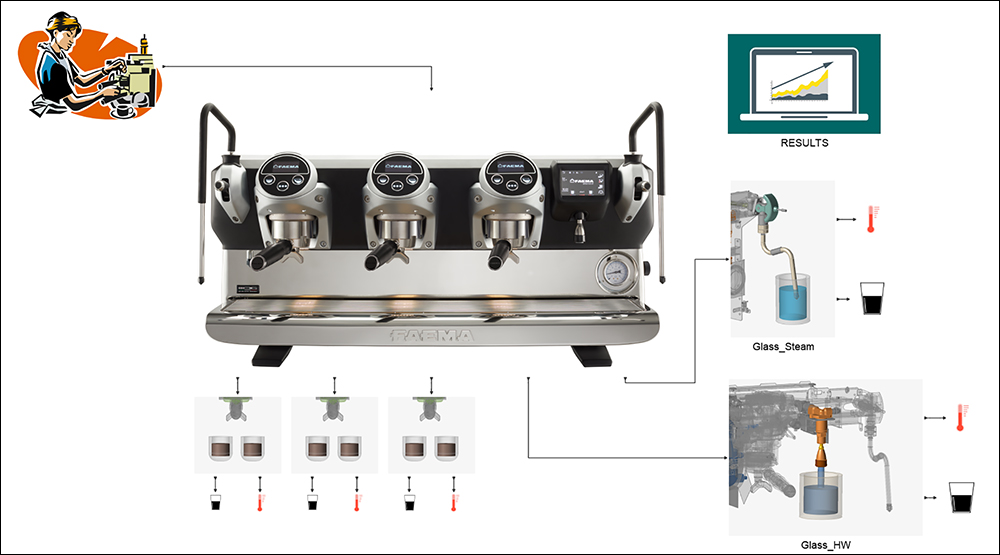
The simulation results from Altair Activate feed a digital twin.
Altair’s platform blends physics- and data-driven twins to support optimization throughout the lifecycle of each Gruppo Cimbali coffee machine, according to Christian Kehrer, Altair’s business-development manager for system modeling. For development and production, he says, this results in a reduced need for physical tests and shortened time-to-market.
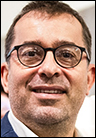
Maurizio Tursini
When adopting the technology, Tursini recalls, the company required a dual solution that would benefit both the production process and the customer experience. “One of the questions that I posed to myself and our team,” he states, “was how to improve performance [of the finished product] to provide better service to our clients and to optimize our own internal processes.” The firm met with Altair regarding its digital-twin solution, the use of which Tursini hoped would reduce time to market, while optimizing product production and configuration.
In most cases, Tursini says, manufacturers create a design for a new product, then build a prototype, conduct tests and validate original assumptions, after which they make changes to the design, create another prototype and test again. With such a method, he explains, “Time to market becomes a little awkward. With this tool, you can simulate how many configurations you want, without building and rebuilding prototypes for testing.”
Altair says its digital-twin technology can reduce the number of tests and prototypes required for any given manufacturing process. In the case of Gruppo Cimbali, this is enabled by capturing real-world data from existing machines in the market. Because the company’s products are already IoT-enabled, Tursini says, “They know what is happening on the customer side of their products. We can feed the real-world data into a simulation model and increase development for possible iterations,” based on the algorithms and mathematics behind the data.
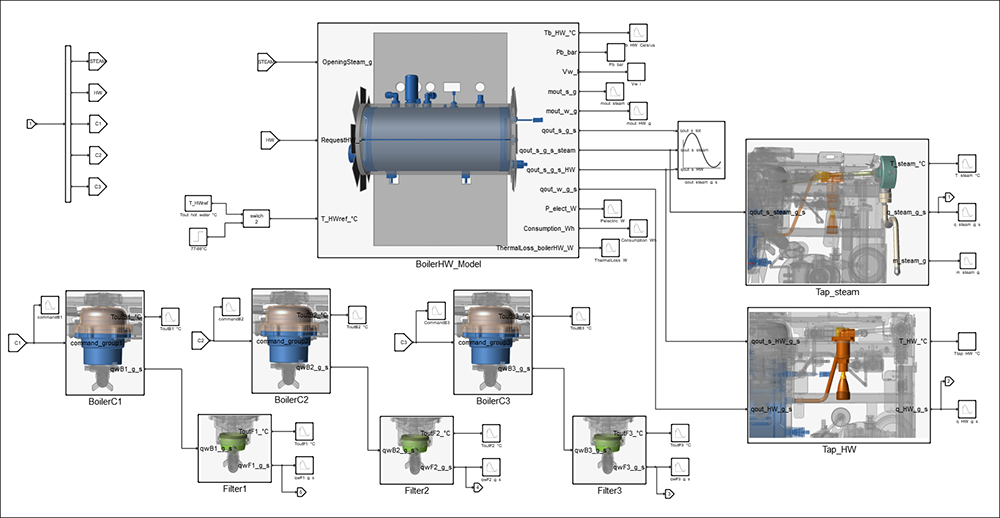
System modeling with Altair Activate allows subsystem optimization. The thermodynamic behavior of all parts of a LaCimbali coffee machine is represented in a modular scheme, allowing for a realistic representation and parameter studies.
The developers are now using the technology to create a virtual version of a new product and subject it to testing digitally, before a prototype is built. “We will use these tools to identify some possible failures that could happen,” Tursini says. In the long term, the digital twin “becomes our way of developing all products,” he explains. “A convergence between real numbers and virtual numbers can happen.”
In the longer term, Tursini reports, the company plans to extend the digital twin to enable the collecting of data about each individual product as it is used, and to create a digital version with which the information can help Gruppo Cimbali make predictions about machine performance. “To me, it opens the door to create new services for the market,” he states, though in the near future, “We hope to have virtual machines in the cloud,” representing each purchased product. “Our hope is to extend our collaboration into other fields. I hope we can digitalize, as much as possible, our internal processes. This is crucial to be top of the market.”
The term “digital twins,” Kehrer notes, is still a buzzword with a variety of meanings, depending on those making or using the tools. “Some talk about fairly simple methods of simulation” for digital twins, he says, with just one or a few pieces of data being fed into the twins initially. Gruppo Cimbali, however, is among the first companies with experience connecting its products, and it already collects and analyzes a wide range of data, which means the digital twins can be used to greater benefit in the development process. “This is so close to our idea about optimizing product performance. That’s why this is a lighthouse project.”