It might sound like science fiction, but Joshua Smith, a principal engineer at Intel Research Seattle, and his team of scientists from Intel and the University of Washington are working to develop passive RFID-enabled sensors that operate on power pulled out of thin air. Stated more precisely, the tags would harvest ambient RF power—that is, already existing RF emissions transmitted by any number of sources, including television, radio and cell phone base stations.
In an experiment, the team mounted a prototype sensor tag on an outside balcony at the Seattle lab. The prototype included a power harvester consisting of a printed circuit board approximately 2 inches by 4 inches in size, wired to a set-top television antenna—the type a consumer would use to receive over-the-air television broadcasts. The researchers aimed the antenna at a Seattle TV transmission tower located slightly more than 4 kilometers (2.5 miles) away, and broadcasting 960kW of effective radiating power at 674 to 680 MHz.
According to Smith, the prototype Wireless Ambient Radio Power (WARP) device was able to harvest the ambient RF signals emitted by the tower and store up sufficient energy to power a commercially available thermometer/hygrometer with an LCD display. The prototype, he says, could be altered to harvest ambient RF power from other sources, such as FM radio, AM radio, or cell phone base station signals.
But WARP is only one part of the Wireless Identification and Sensing Platform (WISP), a project Smith and his group have undertaken to develop passive RFID tags capable of exploiting RF energy to support sensing applications. Other iterations of the tags are designed either to harvest ambient power from an RFID interrogator and store it in a capacitor to allow for data logging over a period of time when the tags are not being read, or to harvest enough power from a reader’s signal to collect sensory information that is immediately transmitted back to the interrogator.
WISP tags have been built with sensors that measure light, temperature and strain (the amount of deformation an object experiences compared with its original size and shape). “The vision is to embed a lot of strain sensors throughout an airplane wing,” Smith says. “They could be read either by a handheld RFID reader, or by one mounted somewhere in the airplane.” WISP tags have also been used to test cryptographic computations for securing tag data, he adds.
Each WISP contains a microcontroller that not only communicates with an off-the-shelf EPC Gen 1 or 2 RFID interrogator but also controls the sensors linked to the tag. According to Smith, most RFID chips do not contain microcontrollers, which typically have at least 20,000 transistors. RFID chips have a finite-state machine, which usually has fewer transistors and carries out a fixed set of functions (implementing the EPC protocol, for instance). “The big difference,” Smith says, “is that finite-state machines are not programmable—they don’t run software.”The tags also contain an antenna and impedance-matching components, an RF power harvester, a demodulator to extract information from reader-to-tag transmissions, a backscatter modulator for transmitting tag-to-reader data, and a voltage regulator.
Whether the WISP platform will be transitioned into a commercial product—and if so, when—is difficult to predict, Smith says. However, he notes, the technology has already been in development for four years and is becoming mature.
Smith cites two examples of possible applications. In the cold chain, WISP tags with temperature sensors could be placed on shipments of food, blood plasma, temperature-sensitive chemicals or other perishables. While the goods are in cold storage, fixed-position Gen 2 RFID readers would periodically interrogate the tags. Each time they were read, the tags could transmit their identity and any required temperature data. But with each interrogation from the reader, a super-capacitor on the WISP tags would also collect some of the RF energy from the interrogator’s signal. Once in transit and out of range of an RFID reader, however, the tags would take periodic temperature readings, powered by the energy saved in the super-capacitors. These readings would be logged to the tags’ memory banks and transmitted to the interrogators once the shipment reached its destination. The data logs would immediately show any potentially harmful low or high spikes in temperature during transit.
In another scenario, WISP tags could be integrated into a hard-to-reach area and read intermittently, to monitor for specific conditions. For example, WISP tags with an integrated water sensor could be installed under roof tiles and read periodically in order to check for water seepage, which would allow users to quickly isolate and repair leaks before they caused significant damage.
A WARP tag requires a large antenna to harvest ambient RF signals, and therefore its placement options would be limited. The size of the other WISP tag prototypes, on the other hand, is similar to that of conventional passive RFID tags.To help generate ideas for other applications, Intel Research Seattle has issued the WISP Challenge, a call for research proposals for specific WISP applications. Smith and his team plan to send WISP development sets to the teams offering the most promising proposals.
Advances in making silicon chips operate more efficiency, as well as decreases in chip manufacturing costs, could make a WISP tag—currently composed of discreet components—economically viable. Smith believes the price of each manufactured WISP tag would be much closer to that of an active tag (in the $50 range) than to the cost of a passive tag, which can be purchased for less than 25 cents apiece. But the complexity of the specific type of sensor attached to a WISP tag would greatly influence its price. In the future, as sensors become integrated into the tag’s chip instead of being added as an additional manufacturing step, tag cost would begin to drop.
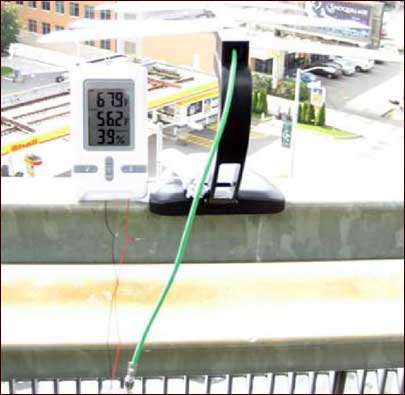
The fact that WISP tags can be read with standard Electronic Product Code (EPC) Gen 2 readers, however, is a “huge advantage” for the system, Smith says, because it makes the system significantly more affordable than it would be if WISP-specific interrogators were required.
Sensory data can be collected in the user memory of the tag’s chip, then sent to the reader using the EPC Gen 2 protocol for transmitting user data. An EPC, or other unique identifier, can be sent to the interrogator using the Gen 2 protocol so that on the reader end, the tag can be identified and associated with the sensory data.
WISP tags can currently be read from up to 10 feet away, Smith says. Advances in chip efficiency and an integrated WISP chip, however, should improve that range.