Two aerospace companies have been testing radio frequency identification solutions enabling the creation of a wireless mesh network of battery-powered tags that can identify the locations of moving, tagged items, and be reconfigured quickly if the layout of their facilities changes. The RFID solutions, supplied by aerospace industry systems integrator ID Integration, include V-Tags and AssetWorx! software from InfinID Technologies, based in Pasadena, Calif. One company has completed its pilot and is integrating the solution into its production system, while the second is still trialing the technology. The two firms have asked to remain unnamed.
Based on the early successes with the two pilots, ID Integration says it has released the V-Tag solution for commercial deployment this month, which it will provide to aerospace and government customers. InfinID has also begun selling its V-Tag system to customers in other sectors, such as health care and military.
The system that ID Integration and InfinID are selling is designed to be simple and easy to deploy, the companies report. High-value items that move around an aerospace facility are tagged with the battery-powered V-Tags, which transmit 2.4 GHz signals via a proprietary air-interface protocol. V-Tags are also affixed to ceilings, pillars or walls, and the location of each of these fixed tags is stored in the AssetWorx! software. A gateway reader is installed somewhere in the vicinity, in order to read transmissions from the asset and fixed tags, as well as forward the collected read data to the software to identify a moving asset’s location. On a map of the facility, the AssetWorx! software displays an asset tag’s location—based on which fixed tags received that asset tag’s signal, and on the signal’s strength, as received by those fixed tags.
ID integration, based in Mukilteo, Wash., sells solutions for its customers—both commercial aerospace and the government—that manufacture aircraft and aircraft parts, or perform maintenance and repair work. As part of its solutions, the company offers laser engraving systems to create unique identifiers on aircraft parts. In recent years, however, it began exploring RFID solutions.
The company says it did not launch its active RFID solution until it could be sure that the technology would be both beneficial and affordable for its customers. “We’ve seen improvements in the technology for tags and readers,” says Gary Moe, ID Integration’s president. Such improvements, he explains, have included metal-mount tags and tags with longer battery lives. “We’re very cautious; we’re careful only to put out systems that we know are reliable. About two years ago, we made a market decision to begin offering RFID solutions.” The firm already had a 10-year relationship with InfinID, which makes bar-code, passive RFID and, most recently, active RFID solutions in the form of the V-Tag. Last year, ID Integration began offering the V-Tag and AssetWorx! system for pilots.
The first company to carry out a pilot is a parts manufacturer for commercial and government aircraft, which operates a 250,000-square-foot manufacturing plant. Within that facility, the firm is responsible for between 3,000 and 4,000 tools used to make those parts. Because it works for specific customers, the parts manufacturer typically uses tools provided by those customers, and thus needs to be able to account for them. Periodically auditors representing those customers arrive onsite to identify whether the tools are in good working order and in use. These auditors must walk through the facility to examine the tools, and the company may fail the audit in some cases if the tools couldn’t be found.
The company designated an RFID team to look into options to improve on this process via RFID technology, and to ensure that auditors can access the tools they seek. ID Integration described the V-Tag solution to the company, and then launched the pilot in late 2014. Approximately 200 fixed tags have been installed around the facility to date, while about 1,800 assets tags have been attached to jigs, fixtures and other basic tools. Both types of tags measure about the size of a box of Tic Tacs and have a transmission range of about 300 feet. The company intends to add another 5,000 asset tags in the future. The system also includes 18 gateway readers to capture data from the fixed and asset tags.
The fixed tags beacon at preset intervals, and the assets tags are designed to transmit data only when they are moving, in order to conserve battery life. With this method, says Chuck Stygar, InfinID’s president and CEO, the tag’s battery life is typically about four years.
When a tool is tagged, a user inputs data about that object into the AssetWorx! software, where it is linked to the unique ID number encoded on the tag. The asset tags come with a built-in accelerometer, and can identify when they begin moving, and then start transmitting a unique ID. With the mesh network, the fixed and asset tags receive each other’s transmissions and forward that data to the gateway. The AssetWorx! software then uses received signal strength indication (RSSI) to identify the fixed tag to which the asset tag is closest. The software can then display that asset’s location. Once the asset stops moving, it becomes dormant, and the software identifies its location based on the last reading taken at the time that movement ceased.
According to Moe, the aerospace company has completed the pilot and is now implementing the solution at two of its facilities.
The second company piloting the system provides maintenance, repair and operations (MRO) services to aircraft companies, and is using V-Tags to track work-in-progress. In this case, aircraft parts are brought into the facility for servicing, and move through specific workstations to have the required maintenance or repair work done. Due to the high level of metal present in the facility, the company’s managers were concerned about the reliability of RFID tag reads, but during an initial, limited 30-day pilot carried out in November 2014, they determined that V-Tags worked well. The company is now testing the system in a larger, facility-wide deployment.
The MRO company also had concerns about the flexibility of any RFID system selected, because with each new contract for a customer, it may need to change its workflow, and thus change the locations and functions of workstations, but it must still be able to track items moving through that new setup. The V-Tag system solves that problem, since the fixed tags can simply be affixed to walls or other locations using Velcro, and then be removed when necessary and reinstalled elsewhere, with the new locations updated in the software.
To track products being serviced, tags are being attached to large, moveable carts on which products are transported. By tracking each tagged cart’s location, the company can now view where an item is at any given time, and learn which phase of servicing is currently being performed, based on the workstation’s location. Additionally, the company can be alerted to or view any potential problems, such as an extended dwell time at a particular workstation, which could indicate that a delay has occurred.
The technology cost is about half the price of a passive RFID solution, Moe says, because although the tags are more expensive than passive tags, no other hardware is required, with the exception of the gateway device. As such, the RFID reader portals required for a passive RFID system are unnecessary. ID Integration also sells passive RFID solutions, he adds, stating, “We’re not exclusive to one technology, but the V-Tag seems to fit a certain niche.”
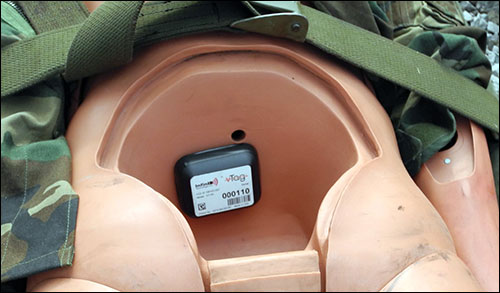
The V-Tag has been in use for several years, Stygar says, in field trials for government deployments. Initially, it was tested by the U.S. Army Medical Research and Materiel Command (USAMRMC) and the Telemedicine and Advanced Technology Research Center (TATRC) to track blood and vaccines at Fort McCoy‘s Regional Training Site (RTS) Medical location, where medical reserve troops are trained. Because the tags also come with temperature and shock sensors, they were able to transmit not only location but also temperature data, thereby ensuring that the perishable products stayed within a safe temperature threshold during mock medical responses.
InfinID, in conjunction with systems integrator VerdaSee Solutions also installed 300 V-Tags for use in manikins for a Disaster Training Exercises at the Camp Atterbury and Muscatatuck Urban Training Complex, in Indiana. The tags were placed in manikins representing dead or injured individuals, which were then dispersed around a simulated disaster area. InfinID also placed an Omni-ID Prox passive EPC Gen 2 ultrahigh-frequency (UHF) tag within the case of each V-Tag. so that personnel in the field could use a handheld reader to confirm a manikin’s identity, if necessary. Fixed tags were attached to light poles in the staging area. Each night, the Army staff could utilize VerdaSee’s Vital-asset software to locate all manikins. In one instance, after the base searched manually for a missing manikin for several days, the system was able to quickly locate it within a concrete tunnel, covered by five mattresses in a collapsed parking structure.
Both government trials concluded in 2014, when funding was exhausted.
With the newly commercially released solution, ID Integration’s customers can purchase the system, including tags, gateway and software, or purchase a software development kit (SDK) so that users can customize their own software integration.
ID Integration and InfinID will exhibit the V-Tag solution next week in booth 748 at the RFID Journal LIVE! conference and exhibition, being held in San Diego, Calif.