The U.S. General Services Administration (GSA) manages more than 11 percent of the government’s total procurement dollars and $24 billion in federal assets, including 8,600 government-owned or -leased buildings and 213,000 vehicles. It supplies the vast array of departments and agencies with office supplies and other materials required to keep the wheels of government turning. This represents a huge logistical challenge, but a real-time location system (RTLS) recently installed at the agency’s Western distribution center in French Camp, Calif., is making meeting that challenge a little easier.
The system, which employs passive ultrahigh-frequency (UHF) radio frequency identification transponders based on the EPC Gen 2 standard, tracks the movements of pallets, boxes and bags through loading dock doors and into the backs of trucks. It is expected to not only record when an item is shipped, but also issue alerts if boxes or bags are being loaded onto the wrong truck, or if an item falls off a conveyor and is at risk of being misplaced.
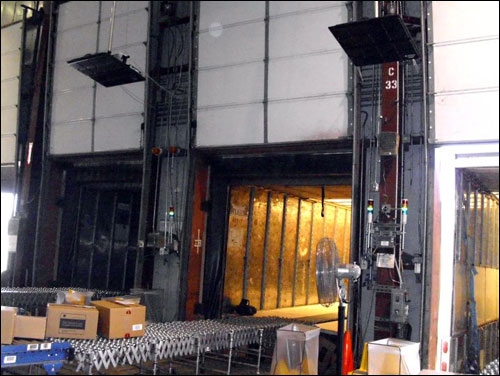
Science Applications International Corp. (SAIC) designed, installed, tested and integrated the system, which uses RF Controls RFID readers and GlobeRanger edgeware and middleware to manage the readers, as well as iMotion software that interprets data between the interrogators and the GSA’s existing HighJump warehouse-management system. XIO Strategies provided consulting and training assistance.
SAIC’s solution offers 3-D views into the location of each tagged box or item. Since the system was installed four weeks ago, the GSA is still assessing what it can do with the system, but the agency’s plan is to expand it to the entire warehouse and tagging of all items, explains Bryan Tiplady, the GSA’s branch chief for general supplies and services.
The GSA’s French Camp DC includes three buildings, totaling 1 million square feet. The facility receives, stores and ships 5,000 types of items, such as paper, office supplies and tools for government agencies and the U.S. Department of Defense (DOD). Approximately 60 percent of the supply center’s items are typically sent to a facility operated by the DOD’s Defense Logistics Agency (DLA) before being shipped to military locations both in the United States and overseas.
When goods are shipped from the French Camp site, they are packed in cartons, which are then loaded onto pallets. Forklifts transport them onto the backs of trucks parked at dozens of loading docks. Some smaller items are more difficult to track because they are loaded not in stackable boxes on pallets, but rather in an odd assortment of box sizes and, for certain smaller items, in padded envelopes.
Instead of being placed on pallets, items in padded envelopes are sent down a conveyor to a dock door, where staff members place the envelopes into clear, 50-gallon plastic bags before loading them onto a truck. Odd-size boxes are loaded directly onto trucks. The GSA wanted to track the odd-size boxes and plastic bags, as well as increase the accuracy of what is loaded onto each delivery truck, and it wanted to do so without significantly changing its existing processes. In addition, the DOD requires all pallets, single boxes or padded envelopes to be tagged.
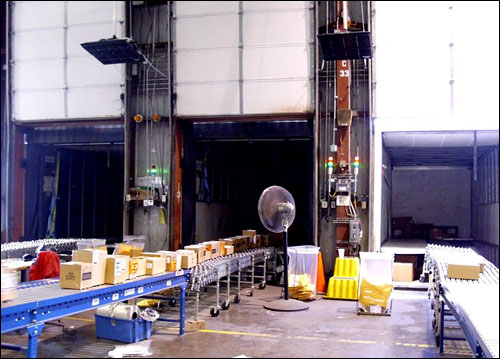
“Part of our challenge was to integrate RFID into our system knowing that it would be necessary only for 60 percent of our volume,” Tiplady says. The GSA decided to install the SAIC system in Building 330, a 600,000-square-foot warehouse that is the largest of the three buildings, at which most of the DOD-destined goods are stored and shipped.
The system consists of RFID readers at the nine loading doors used for shipments destined for the DOD, says Douglas Litten, SAIC’s RFID program manager. These consist of six large loading doors for pallets of boxed items, and three smaller loading doors for small parcels, including bagged items. RFID readers were also installed overhead, Litten says, between the doors through which three conveyors carry the small, odd-shaped items in padded envelopes from the warehouse to the dock doors.
Initially, as the system is being ramped up, the GSA is tagging only about 15 percent of its total inventory—those items destined for RFID-enabled DOD locations. With the new system, when an order is placed, warehouse workers use an electronic pick list and load boxes destined for the ordering customer. The order and location data is then received by GSA’s HighJump software, which interprets the information and forwards it to the iMotion system, according to Michael Bigbee, GlobeRanger’s senior VP of sales.
Each packing station has two printers—one for labels with embedded RFID inlays, and another for labels without them. Based on who the customer is, the SAIC software determines whether the items will be shipped to an RFID-enabled DOD location, and then sends commands to the appropriate printer. If a box or bag is destined for an RFID-enabled DOD location, the label’s passive UHF EPC Gen 2 RFID tag is encoded with a unique ID number, and the front of the label is printed with several bar-coded numbers and printed details regarding that customer. If an RFID tag is not required, a plain tag is generated with only printed data and bar-coded numbers. In either case, a GSA worker removes the tag from the printer and applies it to the box or bag.
When cartons are loaded on a pallet, GSA employees ensure that they have loaded the correct items by scanning the labels (whether RFID-enabled or not) with a bar-code reader. For RFID-enabled shipments, they then print an RFID label for the pallet, and the iMotion software links the RFID number on the pallet with that of the items on that pallet. A forklift operator then drives the pallets to the appropriate dock door, where RFID readers capture the tags’ locations. SAIC software determines whether the correct boxes are being loaded in the appropriate truck, and a red light flashes if there is an exception, such as an incorrect box being loaded. In addition, data from the iMotion software is transmitted to the GSA’s HighJump system, in order to record shipment information for the tagged pallets, cases, boxes and padded envelopes.
SAIC installed RFID interrogators to cover a 4-foot-by-4-foot zone in which items inside padded envelopes are stored as they await being placed in a larger plastic bag. When the goods enter that zone via a conveyor, the SAIC software updates the information to indicate the time at which those items arrived in the zone and were loaded onto trucks. Thanks to RFID readers, the system can also determine if something goes wrong—for example, if an item falls off the conveyor and onto the floor. In that case, GlobeRanger’s iMotion software lists an exception, alerting warehouse managers that an item is not loaded on the truck, and informing them of its location. In this way, Bigbee says, the system provides RTLS data while using inexpensive passive RFID tags, as opposed to $20 to $50 active tags more traditionally utilized in an RTLS.
Workers also employ a Motorola MC9090-G RFID handheld computer to read tags in the event that an item is misplaced. For instance, if the staff finds a loose item in the warehouse, they can simply read its tag to determine what it is and where it was destined.
RFID readers suspended from the ceiling, at a height of 15 feet above the nine dock doors, are used to determine the location of each tag residing within about 20 feet of the dock doors, with an accuracy of approximately six to 12 inches. “This accuracy is most valuable in the small parcel area, where we use small zones,” Tiplady explains. “Later, when we leverage this technology to receiving and inventory-management functions, this accuracy will allow us to drive more value back into the operations. In the larger freight doors, it is valuable to know when an item is out on the floor, being staged and loaded.”
Installation and use of the system, Tiplady says, “was the non-event I was hoping it would be. Our business processes did not change dramatically.” To assist the staff in using the technology, XIO Strategies provided a one-week RFID course.
According to Tiplady, the GSA will continue to review how it will use the system to gain greater visibility within its warehouses, though it hopes initially to benefit through a reduction in loading problems, thanks to the alert function for warehouse staff members. Whether the system will save the facility time in its loading process has yet to be decided. “We have established our baseline metrics and will measure the gained efficiencies over the next months,” he states. “I don’t think we’ve even scratched the surface for what we can do.”
Tiplady hopes to utilize the system to record the arrival of items, already tagged with RFID labels by the suppliers of those goods, and track where they are stored throughout the warehouse. This, he says, would require the installation of additional readers.
The installation is significant for the DOD as well, Bigbee notes, since the GSA provides a large percentage of all supplies received by the military. By tagging its own products, the agency is helping the DLA in its efforts to track more shipments with RFID. The GSA and DLA together represent about 80 percent of the DOD’s supplies. By completing this installation at French Camp, Bigbee says, “the GSA is helping fulfill the vision the DOD has had for a while.”