The places where RFID tags can be placed are almost limitless. One exception has been the challenge of integrating an RFID inlay within an object composed of metal. That’s because the high temperatures required to melt and shape metal can destroy the components making up an RFID tag.
However, researchers at the Fraunhofer-Institute for Manufacturing and Advanced Materials (IFAM), in Bremen, Germany, indicate they’ve come up with a solution enabling them to embed a standard RFID tag within a metal object as that item is being manufactured. The technique makes use of a 20-year-old process called selective laser sintering, and IFAM engineer Claus Aumund-Kopp says his team has successfully built metal parts that include an RFID tag inside. The researchers presented their work at EuroMold 2009, a trade fair focused on mold making and tooling, held this week in Frankfurt.
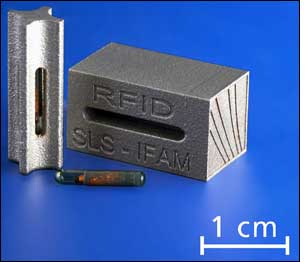
Working with metal powder and a laser, it is possible to produce parts straight from a 3-D model generated with a computer-aided design (CAD) application. The process is painstaking: Powder is laid down in layers 20 microns (0.0008 inch) in thickness—approximately a quarter the width of a human hair—and a laser melts it in the shape of the desired part. Layer by thin layer, the metallic object emerges from the powder. “The chip is inserted into the part when we have reached a certain height,” Aumund-Kopp explains.
Traditionally, RFID tags have been unusable in parts heated above 100 degrees Celsius (212 degrees Fahrenheit), though some tag manufactures have developed versions able to withstand temperatures as high as 1,093 degrees Celsius (2,000 degrees Fahrenheit) by encasing the RFID inlays in protective materials (see William Frick & Co.’s Gen 2 UHF Tags Take the Heat for Manufacturing Apps). In metal casting or laser fusion, however, temperatures can exceed 1,400 degrees Celsius (2,552 degrees Fahrenheit).
With Fraunhofer’s process, Aumund-Kopp says, only a tiny bit of the material is ever heated, because of the gradual, partial nature of the process. That allows his team to use standard RFID tags that would be destroyed in traditional metal casting. “They’re standard chips, with a standard glass cover,” Aumund-Kopp says. “The trick is, the laser doesn’t directly hit the chip, or hits it for such a minimal time that the chip isn’t destroyed in the process.”
Even more important, Aumund-Kopp adds, the Fraunhofer team discovered that the chips can be completely embedded within a metal part and still function. “We have found chips which are completely covered and are still readable,” he states. “This is really new—usually, you need a gap where the electromagnetic fields can couple.” The findings came as a pleasant surprise to the researchers, he says, and have created a puzzle for the future. “We can’t explain it ourselves. We need to do some more tests.”
In the meantime, the team is working to make the findings applicable industrially. Thickness apparently matters, Aumund-Kopp says—the chips are still readable beneath 100 microns (0.004 inch) of metal, but no deeper than that. So far, he notes, the chips that work best transmit at a frequency of 125 kilohertz. “It’s only readable over short distances, but that’s also the frequency that is most secure,” he explains. “We still have some way to go for the larger reading range.”
At EuroMold, Fraunhofer’s researchers presented metal finger rings in which they had embedded RFID chips. Such RFID-enabled rings could be worn, for instance, in order to gain admission to secure rooms. But as long as the technology remains fairly expensive, the most likely applications will be narrow.
Whereas an RFID chip molded within a plastic object could be removed and placed into something else, the chip inside a metal part could not be extracted from that object without destroying the chip. The most immediate application might be fraud prevention, Aumund-Kopp says, noting, “Think of aviation, where the quality of spare parts is vital.”
Integrated into an aircraft component, for example, an RFID tag would not only enable a manufacturer to track that item, but also allow it to later verify that a customer used the genuine article—and not a cheaper, lower-quality counterfeit—in the event of part failure. “With these chips,” Aumund-Kopp says, “you can ID the part securely.”
Another potential application, Fraunhofer reports, is to create parts containing an RFID tag with a temperature or expansion sensor, in order to record data on thermal or mechanical stresses on the components.
IFAM’s tag-embedding technique remains costly, Aumund-Kopp indicates, primarily because the selective laser melting process used by the researchers is not ideal for mass-manufacturing. However, that may change. “We’re at the very beginning,” he notes. “We’re definitely looking for partners who want to further develop its potential.”