A. Kempf Getränkegrosshandel, a wholesale distributor of beer, wine, bottled water, soft drinks and other beverages, has implemented a radio frequency identification system at its warehouse in Balingen, Germany. The technology is being used to identify pallets loaded with customer-ordered goods as they are delivered to conveyors controlled by an automated warehouse system. The RFID solution was built into the company’s automation technology in November 2013, according to Dominik Kampf, head of contracting customer service and support at SSI Schäfer, the firm that provided A. Kempf’s automation system and installed the RFID technology. The solution was taken live last December.
A. Kempf operates two distribution centers, one in Balingen and another in Offenburg. At the Balingen site, the company ships beverage products to 125 of its 600 customers daily. Each afternoon, the trucks are loaded for the next day’s delivery, and afternoons and evening are thus a busy time at the warehouse. During peak season, 174,000 or more crates and boxes of beverages leave the Balingen warehouse each day. Between 3 PM and 8 PM, the company’s peak shipping time, employees load up to 60 trucks at five shipping docks.
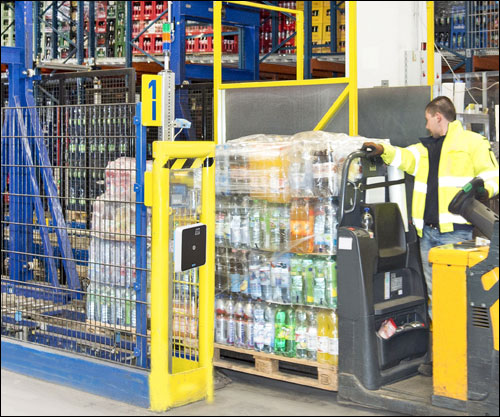
By June 2012, the company had automated many of its processes at the warehouse, in order to keep up with order volume. The automation includes conveyors that move the pallets stacked with beverages through two “buffer” zones before they are taken to the dock doors and are loaded onto trucks.
With the automation system in place, warehouse workers pick the products required to fill a particular order and load them onto pallets, which are covered with stretch wrap. Forklift drivers then deliver the pallets to a receiving station that conveys them to the order buffer, where software determines routes for the delivery of each customer’s order. Once the route schedule is completed, a conveyor system transfers the pallets to what is called the tour (route) buffer, where they then await loading onto the appropriate truck.
The automation makes it possible to sort and move a large number of loaded pallets, the company reports, and to prepare them for loading onto the appropriate vehicles. However, several manual processes were necessary prior to the RFID system’s installation. Each time a warehouse operator brought a loaded pallet to a receiving station, he needed to scan a bar-code ID number on every pallet to update the software regarding which product was being moved. The system could then decide where the pallet needed to be directed in order for it to reach the proper vehicle at the correct dock door.
“Our goal was to decrease the feed-in time” in which the pallets were passed off from drivers to the automated conveyor system, Kampf explains.
Therefore, approximately one year after the automation system went live, A. Kempf ordered an RFID solution from SSI Schäfer. This enabled the company to update its bar-code-enabled loading stations to employ RFID technology.
To automate the hand-off process to the automated system, A. Kempf installed three Sick RFU 630 ultrahigh-frequency (UHF) RFID reader units, one at each of three receiving stations for the order buffers. Each of A. Kempf’s employees uses an ID card containing a UHF RFID chip. Kampf declines to indicate the make and model of RFID cards implemented. Each forklift comes with a holder for the driver’s card.
Upon beginning his shift, a worker proceeds to a vehicle, registers by keying his ID number into that vehicle’s onboard computer, and then places his ID card in the holder on the side of the forklift. The individual receives his assignments on his forklift computer terminal, and indicates such on the terminal screen when he picks up the pallet on his assignment list. The software then transmits that data to the receiving station’s material-flow computer, which thus knows that a specific pallet is en route to that station to be loaded onto a conveyor. When the driver delivers the pallet to that station, the reader installed there identifies his ID number—which had previously been linked to that pallet, along with details indicating which customer it is intended for—and accepts that pallet. In that way, the system knows exactly which pallet has been received at that station.
In addition, the system stores that information for A. Kempf’s own management software. In this way, it creates a record of when that order was filled.
By using RFID technology, Kampf reports, the company has reduced the amount of time required for the handoff to the conveyor system, from about 15 seconds down to two seconds. Taking into account all pallets transferred during a given day, the savings equates to eight hours of labor daily.
“With the RFID solution, we have further optimized the transfer processes and adjusted to the high throughput capacity of our new system,” Kampf states. “The achieved results prove that we have made the right decision.”