In Tonawanda, N.Y., General Motors‘ factory temporarily installs a bolt with an embedded passive RFID tag on every cylinder head and engine block that GM uses to make its Gen 5 six- and eight-cylinder engines, in order to track the assembly process and verify that the procedures are being carried out. Since going live in early 2012, the Gen 5 assembly line has been fitted with 284 RFID read-write heads, and each engine block and cylinder head comes with a 13.56 MHz RFID-enabled bolt compliant with the ISO 15693 standard.
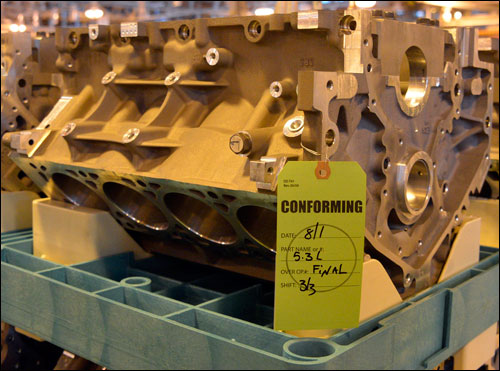
General Motors has been employing RFID technology for engine assembly for more than a decade at the Tonawanda site, according to Mark Chiappetta, the plant’s manufacturing engineering superintendent. The company has been applying a passive 13.56 MHz Siemens Simatic RF340T tag, containing 8 kilobytes of memory, to every pallet on which engines are loaded, enabling the collection of data regarding each engine’s assembly. First, an engine assembly is placed on a pallet, and the engine’s unique ID number is then input and linked to the RFID number on the tag permanently affixed to that pallet. The pallet tag is read and written to as the engine moves through dozens of assembly processes, is removed from the pallet and is shipped out of the plant for installation in a vehicle. By tracking each pallet, GM maintains a record of every process, as well as when it was completed. This information not only helps the plant ensure that the correct processes are being carried out in the proper order in real time, but also provides historical data in the event of a factory recall or faulty part, helping the firm to identify all engines assembled at a specific time or by a particular machine.
The factory also attaches a Balluff passive 13.56 MHz button-shaped tag to each machining tool. The tools are periodically swapped out in machines used for assembly, and installing the wrong tool in a machine could result in potentially serious errors. By installing an RFID reader in the machine and placing tags on the machine tools, GM can ensure that such mistakes are not made.
When the plant began preparing for assembly of the new Gen 5 engine in 2011, Chiappetta says, GM began looking into ways in which RFID could be used for the assembly of heads and blocks prior to their placement into engines. Typically, this requires dozens of processes, such as cutting, molding or washing, and it is important that the assembly machines are adjusted for the proper part before any work is performed at each point along the assembly line. If the machine processes an incorrect or incomplete part, that could result in damage to the part or to the machine itself. To ensure that this does not occur, GM and other manufacturers typically use two processes—a visual system with a camera to confirm the Part Unique Number (PUN) printed in human-readable text, and a 2D bar code on that part to indicate the kind of part it is—as well as a technology known as a bump code probe. The latter machine is installed at each operation location, providing redundancy in the event that the visual technology fails to properly identify the part.
The bump code probe consists of a mechanical probe assembly that drops from the ceiling and applies multiple probes with built-in springs to a part, in order to measure its size and dimensions, thereby confirming the part’s type, as well as the processes already completed on it. This technology, Chiappetta says, can be expensive. In addition, by using RFID, the company determined that it could collect data regarding each unique item’s movements, and track when it may have left the assembly line and was then returned, based on data written to the RFID-tagged bolt and read via a handheld or fixed interrogator.
The solution consists of a total of 200 read-write RFID heads from Balluff that are attached to the conveyor system at each assembly or operation point, for the purpose of manufacturing engine blocks, in addition to 84 read-write heads for the cylinder heads. GM determined that an off-the-shelf RFID tag would not survive the assembly process. Balluff offers an RFID tag in the form of a screw-in bolt, a customized version of which GM is using.
“We worked with Balluff to create a custom bolt,” Chiappetta states. The resulting bolt tag employs a proprietary thread type to fit the proper hole size, and includes a Balluff BIS M-series 13.56 MHz tag built into a recess in the bolt’s head, held in place by epoxy. The bolt is inserted into one of a block’s or cylinder head’s existing holes that will later be used to secure it to an engine with another bolt in engine assembly. The ID number encoded to the bolt’s tag is then interrogated via a Balluff BIS-M read-write head, and is stored—along with the engine’s unique number—in GM’s own back-end software, as well as in the bolt tag’s 2 kilobytes of memory. Balluff provided the middleware that interprets the read and write data and forwards that information to be integrated into GM’s software.
As the part passes through assembly, its tag is read at each processing point, and the data on the bolt is then transmitted to the back-end system, which can instruct the machine to proceed or shut down in the event of an error. Once the process is complete, the read-write head then writes data to the bolt tag, indicating which process has been completed.
If a block or cylinder needs to leave the assembly line due to an exception, it can also be read by staff members using a mobile reader. The plant is utilizing Psion Workabout Pro handheld computers, each with a Balluff read-write component attached to it, to enable personnel to read every part’s bolt tag. However, because the screen on that device is small and can be difficult to read, the company has also developed a cart reader that GM built itself, with a PC connected to a Balluff interrogator that can capture the ID of a bolt tag on a block or cylinder that has left the assembly line. It can then view data regarding that part on the PC screen via a USB connection to the back-end software.
Once a block or cylinder has completed the assembly process, the bolt is removed, data is cleared from its 2-kilobyte memory, and the part’s assembly history is stored in GM’s own software. The bolt can then be reused on another part.
The technology has prevented several errors to date, Chiappetta reports, which he says is the most important benefit. “Mistakes can be costly,” he adds, since some machines are valued between $100,000 and $1 million apiece. The company also wants to be certain that every part going into its vehicles was properly manufactured. However, he says, GM has saved the cost of installing visual systems linked to the bump code probes at each of the 284 points of assembly. “It’s a testament to the accuracy of RFID that we can now comfortably remove the bump probes,” he adds.
GM intends to use the RFID technology on future assembly lines as new products are released, Chiappetta says. “It’s now a standard [element] on any programs going forward,” he states.