General Electric (GE) Renewable Energy, located in Grenoble, France, is among a handful of companies from a broad range of industries that are planning to pilot or deploy RFID-enabled sensors which can be glued or attached to an asset without requiring a power source. French technology firm Asygn has been testing the technology at its own laboratory, while GE Renewable Energy has also tested the system on products in its own lab. The company plans to launch a pilot at a customer’s site in order to determine whether RFID tag reads can identify the conditions of equipment as it is used to produce hydro-energy.
For the energy application, the system consists of Asygn’s sensor IC embedded in tags with built-in UHF RFID functionality, attached to the rotating parts and shaft line in the hydro turbine generators. The tags capture temperature and strain measurements, then forward that data to RFID readers to identify when a machine requires inspection or maintenance. Asygn has been providing sensors for condition monitoring for the past decade, and it has more recently included UHF RFID sensor IC in its devices.
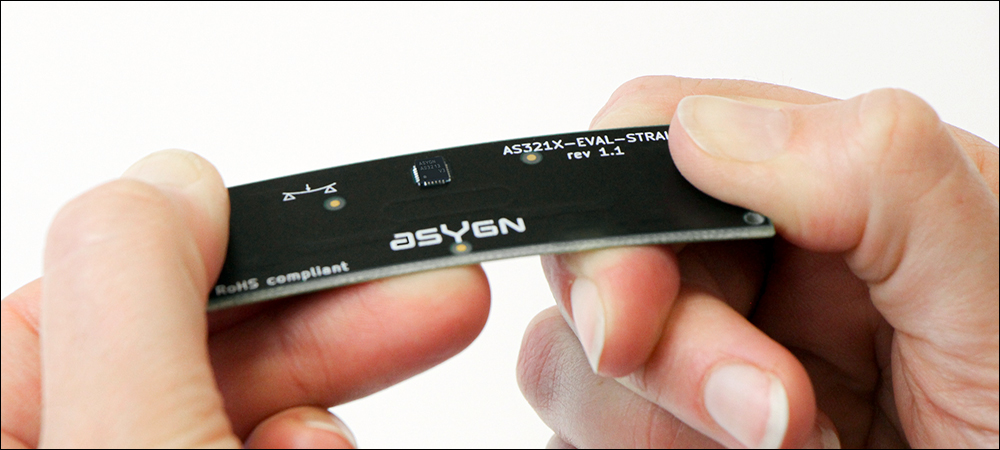
Asygn’s AS321X sensor IC
Asygn’s AS321X sensor IC utilizes the power of an RFID interrogation to capture those sensor measurements and transmit them to a reader, along with a unique identifier (see Energy Company Testing Passive RFID Sensor for Equipment). Other businesses piloting or deploying the sensor tag include not only energy companies, but also healthcare, agriculture and construction firms, according to Frederic Maricourt, Asygn’s commercial director. For hydro power, says Vincent Bouillet, GE Renewable Hydro’s head of IIoT development, the goal is to track generator parts and shaft line temperature and strain in very harsh conditions where traditional solutions are ineffective. “We are using wired sensors in static parts of turbine generators to check its conditions,” he states, “but high-moving parts like the generator poles are less instrumented today, even though it is a critical part of the equipment.”
A wired sensor, Maricourt says, could not be applied to spinning rotor parts, though the first sign of an operational problem tends to be exhibited by the rotating parts before an engine overheats. If such a problem is detected early, he notes, the maintenance issue is typically easier to resolve. In fact, by the time an engine is overheating, some damage to the hydro generator rotor may have already occurred. That can mean the generator will need to be shut down for unplanned repair or replacement, delaying energy production for days or weeks.
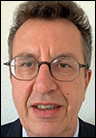
Frederic Maricourt
The sensor tag measures approximately 7 centimeters by 2.5 centimeters (0.4 inch by 2 inches) and can be applied to a hydroturbine’s salient poles “after a careful analysis by GE experts,” Bouillet says. By affixing tags directly onto interpole connections on the shaft line, users can measure temperature levels and detect strains using a handheld or fixed reader, within a distance of about 5 meters (16.4 feet). Each generator can have up to 150 sensors, providing redundancy of data, with up to five sensor tags in each rotor shaft. The sensors can accommodate temperatures ranging from -40 degrees to +125 Celsius (-40 degrees to +257 degrees Fahrenheit). Users can set up the software to create system parameters, such as prompting an alert if the reader captures a high temperature.
A variety of other applications are currently in the works around the world, Maricourt reports. For instance, a horticulture company is testing the sensor to track the conditions of flowers inside a large greenhouse, by tracking temperature and moisture levels, as well as plant lighting, in some cases. The tags represent the cluster of plants in a specific area, he explains. The system is being deployed now, Maricourt says, and is likely to include fixed reader antennas on the greenhouse ceiling. The solution is also being tested with RFID reading carts, he adds, which can be rolled through aisles. The company’s goal, he adds, is to use the technology to better understand conditions and the impact they have on the health of growing flowers.
For instance, the solution can measure soil moisture levels and thus understand when to adjust watering or lights as plants grow. According to Maricourt, several companies are seeking to deploy the system in outdoor fields, and the tags would be read via RFID reading drones. The solution is expected to save energy, water and chemicals for the grower, and to bring plants more quickly to harvest. What’s more, Asygn is developing a solution to detect the integrity of bridges and other structures, for use in predictive maintenance. The company is presently in conversations with construction firms that are interested in deploying the system on their own worksites. To serve this application, Asygn developed a feasibility study, and it says it should have the results by the end of this summer.
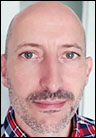
Vincent Bouillet
The sensor tags can be embedded in concrete and detect moisture and strain information in order to identify when there may be a crack. Typically, Maricourt says, the technology used for this purpose has had limitations regarding battery life. “This kind of system already exists to detect cracking,” he states, “but all the systems are provided with batteries that have a lifetime of two or three years. For critical maintenance,” Maricourt explains, “the batteryless sensing is key and is our advantage.” Since the tag requires no batteries, it can theoretically operate throughout the life of the structure. The company is also working directly with concrete manufacturers to enable the technology to be built into concrete blocks. To capture sensor data, users can drive past the structure with an RFID reader and periodically conduct inspections of the integrity.
In addition, Asygn is building and testing sensors for a solution to track the health of medical implants. Currently, Maricourt says, “when you are implementing an implant, the only way to check if there is a problem is if the patient has illness or pain.” In many cases, he adds, that is too late “Our system is a temperature and strain sensor” that could be built into a medical device. If an infection or breakage occurs, the sensor would detect overheating or a change in strain measurements. The sensor tag would be interrogated through a patient’s body, and doctors could capture the data and thus view whether any problems were arising, even if the patient exhibited no symptoms.
A spinal implant maker is now evaluating the technology, Maricourt reports, though the device is not yet ready to be implanted in human patients. The technology will still require further testing and certification, he says, and the company expects that to occur early next year. Asygn anticipates the solution will be widely adopted once it completes that process, Maricourt says, adding that there are currently 1.6 million spinal implants in the United States alone.
An unnamed company in Asia has begun testing the sensor IC for use in tracking the temperatures and movements of cows, with plans to eventually deploy approximately 50,000 sensors among livestock. Each tag is applied to an animal’s ear, where it then captures temperature and motion data. The tags are interrogated via fixed, handheld or vehicle-mounted readers for periodic checks, or with drones that fly over a field or stock yard. By capturing temperature and motion data, the company notes, the system can identify any animal that may be behaving abnormally, or that has a high temperature. In that way, the animal can be separated from the herd and be treated for its ailment.