Urban farms are not an insignificant source of global food production. In a recent article published in Ensia magazine, Elizabeth Royte wrote, “The Food and Agriculture Organization of the United Nations reports that 800 million people worldwide grow vegetables or fruits or raise animals in cities, producing what the Worldwatch Institute reports to be an astonishing 15 to 20 percent of the world’s food.” As the local food movement has taken root in the United States, urban farms here are adding more to the bounty.
But this type of farming must scale up if it is to become a viable means of feeding a growing population—as well as sating the growing demand for local food in cities. Boston startup Freight Farms is working to give urban farmers the tools they need to do so. The company provides former refrigerated shipping containers converted into hydroponic farms that can each produce up to 50,000 heads of leafy greens annually (the containers can be run all year, so there is no growing “season”). Inside each container is an LED lighting system that mimics sunlight (and dims during night hours), optimized for uniform plant growth.
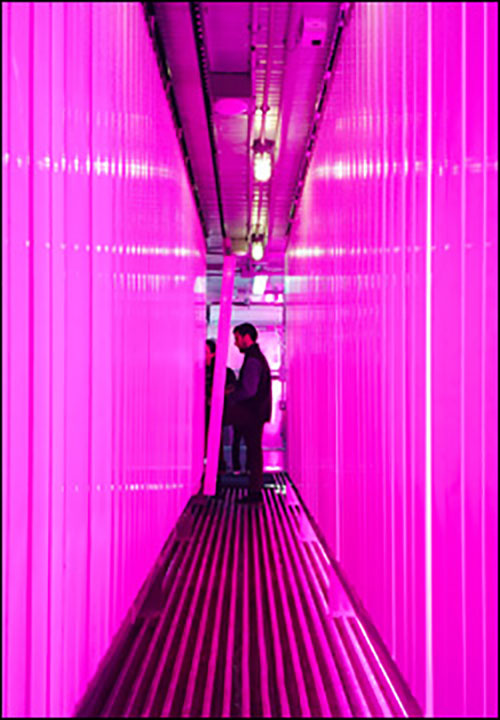
The company, which launched in 2010, built its first Leafy Green Machine (LGM) in 2012 and has since sold 35 units across North America, where individual farmers, produce distributors and restaurant owners are growing herbs and lettuce in parking lots and alleyways. It recently upgraded to cloud-based management software and added Internet connectivity via Wi-Fi or Ethernet (cellular connectivity, for users outside urban centers, is in the works) to the containers. This means Freight Farms can now offer farmers the ability to check on the status of the environment within a container remotely, using the company’s farmhand mobile app. By installing Internet-connected video cameras in and around the containers, users can also log into the app to ensure that their farm is secure.
Inside the container, a series of sensors are used to control the climate and ensure that the water quality and filtration systems are working properly. Freight Farms’ head of farm technology, Kyle Seaman, says the company uses 12 discrete, wired sensors that track the water’s electrical conductivity, pH and nutrient levels, as well as ambient humidity, temperature and carbon-dioxide levels.
Farmers can set parameters for inputs (light, temperature and so forth), and receive alerts from the farmhand app if any sensor readings exceed those parameters. By accessing the cloud-based software via a Web browser, users can change settings inside the container remotely. Soon, users will be able to adjust settings through the farmhand app as well. Currently, they can use the app to receive notifications in the event that any settings fall outside a set range.
Freight Farms offers guidelines for air and water settings, but each user might chose to tweak these and experiment with various crops, in order to determine whether he or she can improve yields. One benefit of streaming the data from environmental controls inside each container to Freight Farms’ cloud-based software, according to Seaman and co-founder Jon Friedman, is that now Freight Farms can aggregate data across all of the units it has sold, in order to search for patterns or anomalies related to specific crops or locations, and to help its customers learn from others.
Ted Katsiroubas, the CEO of Katsiroubas Brothers, a 100-year-old wholesale produce distributor that services Boston-area restaurants, says that when Freight Farms approached him a couple of years ago to find out if he would be interested in operating a container farm on his property in downtown Boston, he was intrigued. For one thing, he says, it would be far more affordable (up to six times less expensive, according to Freight Farms’ figures) than establishing a rooftop garden—plus, the technology-based approach appealed to him. “We’ve been sourcing product locally for as long as we’ve been a wholesaler,” he explains, “and the opportunity was interesting to me.”
When it began using the first-generation Freight Farms container, Katsiroubas Brothers grew herbs, which the company sold to local restaurants. It has since upgraded to the second and latest generation of containers, which is more energy-efficient and produces higher yields than the first-generation design. Currently, Katsiroubas Brothers grows baby spring mix lettuce inside the container, but it also purchases lettuce and herbs from four urban farming operations, located in Boston, that have launched businesses using Freight Farms’ containers during the past two years.
The base price of a 40-foot by 8-foot by 9.5-foot Freight Farms container—including all of the infrastructure (LED lights and hydroponics equipment) inside, as well as an air-conditioning unit—is $76,000, Friedman reports. The annual operating costs, which include energy and water costs, as well as labor and rent for the land on which the container is placed, generally run around $13,000 per year, he adds. That varies, of course, based on the local prices of energy and water, and on whether a user owns or rents the land. Other expenses include the seeds and growing medium—which, combined, total about $150 per month per container, Friedman says. A customer also pays a $9.99 monthly subscription fee to access the Freight Farms software platform and mobile app.
Freight Farms sources its hydroponics equipment from Zipgrow, which sells a vertical system that uses plastic towers to contain slots filled with a growth medium in which newly sprouted seeds are planted. Nutrient-infused water enters the top of the tower and is collected, filtered and then reused, forming a closed loop. Microgreens can be grown in horizontal trays inside the containers as well. Each container loses roughly 10 gallons of water daily, Seaman says, through consumption by the plants, as well as evaporation.
Energy consumption varies by region and according to how much heating or cooling is required. In general, Seaman says, a Freight Farms unit that operates in warm climates requires more energy than one in a very cold climate, because the heat emitted from the LED lights used to grow the food helps to warm the air inside the container, which is very well insulated. (He estimates that the average Freight Farms unit consumes 30,000 kilowatt hours per annum, or 85 KwH per day.)
Katsiroubas admits that he has not yet done the math to determine whether he has begun to see a return on his investment—that’s something that his CFO is working on right now—but he says the benefits of being able to source produce from Boston, both onsite and from other nearby urban farms, are difficult to measure. It’s not just a matter of comparing the total costs of producing the goods locally versus trucking them in from New England farms or from California, he notes. Locally grown products appeal to consumers, who are then likely to return to restaurants where those products are served, and this trickles down to benefits for Katsiroubas. Plus, he says, the ongoing drought in California is likely to directly impact the costs of importing produce from the Golden State (the costs of California produce have already risen, he says, but that is more directly tied to raising labor costs than to the drought).