Packaging manufacturer Accord Carton is preparing to expand its RFID system that currently enables automatic identification of pallets loaded with its products as they move through a robotic storage system. With the RFID system—provided originally by Miles Technology, an RFID company that was acquired last year by Barcording Inc.—the company can identify when each pallet is loaded, sized and placed into or taken out of storage. The expansion, planned for later this year, consists of installing an RFID reader at the loading dock, in order to extend that visibility to the shipping of goods. With it, Accord Carton can prevent errors and gain a more detailed inventory of where each pallet is, and when, which it can also share with its customers.
Based in Alsip, Ill., Accord Carton makes folding cardboard cartons customized in size and shape as well as with logos and printed text on the cartons. Accord cuts and prints the cartons, and stores them flat on pallets. Customers can then fold them for use in storing goods such as food or beverages, pharmaceuticals or personal-care items. The movement and storage of loaded pallets is mostly automatic, thanks to a robotic solution from HK Systems, an automated material-handing company since acquired by Dematic. When a pallet loaded with finished cartons comes off the conveyor, it is routed to one of two locations—directly to the loading dock to be shipped out, or to the HK automatic system that places the pallet onto a rack for short-term storage until an order is ready to be shipped.
The challenge for the company, however, has been ensuring where each loaded pallet is. Prior to installing its RFID solution, the company relied entirely on a staff member to visually identify each pallet, and determine what was loaded on that pallet and for which customer, by reading the order sheet placed on the pallet. The pallet would come off the loading conveyor and pass to a holding area, where it waited prior to being sized before the robotic racking system put it away. During this pause in the loaded pallet’s movement, the worker would read the order sheet that had been placed or stretch-wrapped onto the top of the pallet, and then input the order information into the management software.
Because the automation made it a safety concern for staff to be walking around the pallets, a worker conducted this process from behind a glass window in a computer room about 10 feet from the pallet. However, it was hard to read the text and ID numbers on the sheet of paper from the room, so the worker often had to use binoculars. Sometimes, even with binoculars, the employee could not make out the necessary details and had to leave the room and walk out onto the floor to examine the paperwork at close distance.
This solution was time-consuming and delayed the racking process, as well as creating a potential for errors, says William (Bill) Codo, VP of Accord Carton. Codo says the company began looking for an RFID solution to identify each pallet instead. Since the company already used the printed order form that travels with each pallet during the loading and shipping processes (and also used by the customer to identify the products it is receiving), Accord Carton wanted to embed an RFID tag into the order form, rather than affixing an adhesive RFID tag directly to the pallet.
“We did some research online and called a couple of different companies,” Codo says. He and his colleagues found Miles Technology to be the most responsive and flexible.
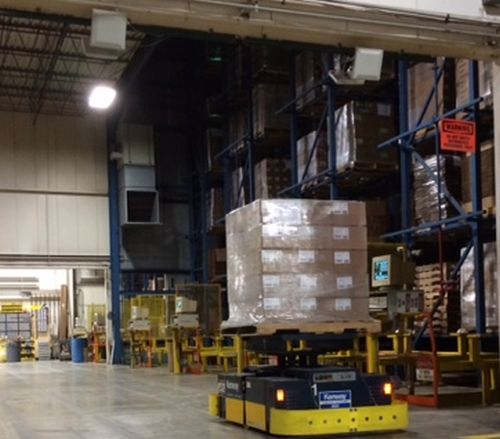
At the end of 2012, Miles Technology installed Impinj R420 readers at three zones within the facility, says Tom O’Boyle, the RFID director at Barcoding Inc. The first is located at the end of the loading conveyor, where each fully packed and (in some situations) stretch-wrapped pallet is deposited. Every pallet’s order sheet now has an Alien Technology ALN-9640 Squiggle Higgs-3 passive UHF RFID inlay incorporated into it. The tag’s ID is stored in Barcoding Inc.’s RealView software residing on Accord Carton’s server and linked to the specific order including the type of cartons and sizes, the quantity and the name of the customer. As the tag is read, its pallet is identified as packed and ready to be moved by an automatic guided vehicle (AGV) to the storage racking area or, if intended for immediate shipping, taken directly to the loading dock.
Pallets headed for the racking area have another stop, where a second RFID reader is located. Before reaching the racking system, each pallet stops at the sizing station where its height and overall dimensions are determined. This is the location where staff had been visually identifying the pallet, based on the printed text on the paperwork. With RFID, the reader captures the tag ID number, and the RealView software calculates the pallet’s size, based on the quantity and size of cartons and links that data to the ID.
At the entrance to the racking area, the company installed a third reader with four antennas connected to it, two to read pallets inbound to the racking system, and two to read tags on the outbound, thereby enabling the company to identify in which direction the pallet is moving, explains Raul Garcia, senior account executive at Barcoding Inc. As the pallet enters the racking area, this reader captures its tag ID, and based on that ID the RealView software forwards data related to that pallet’s size to the racking system, enabling the robotic system to determine which shelf would be suitable for storing that pallet. When a loaded pallet is ready to be shipped out, the robotic system retrieves it, places it on an AGV that then transports the pallet out of the area, again past the RFID reader, updating the data to indicate it has now left the racking area.
Since the RFID system was installed at the end of 2012, customers can now input a user name and password when signing into Accord Carton’s server and view which products have been manufactured by inputting an order number linked to pallet IDs, thereby learning whether those cartons are in storage or have been shipped.
Codo says his company has not done any studies to determine the monetary gains they may have accomplished with the RFID system. “I don’t like hanging numbers on this kind of thing,” he says. Ensuring that Accord Carton has the correct data and greater visibility of pallet location, he explains, is enough justification for the solution.
Once Accord Carton installs an RFID reader at its loading dock, Codo adds that he will then have a view into when exactly pallets were loaded, and that data could easily be added to the RealView software.