Many companies are leveraging radio frequency identification (RFID) or Internet of Things (IoT) technologies to ensure worker safety by tracking each individual’s proximity or location. The challenge is multifold, though, for some businesses at which hundreds or thousands of contract workers periodically surge onto a worksite for days or weeks at a time, then leave.
Global fertilizer company Nutrien faces such a challenge, with periodic scheduled breaks in production for maintenance services known as turnarounds. At one nitrogen site, for instance, the company employs a few hundred workers, but the turnaround can bring 1,500 more. All of the contractors are there only for a short time, yet they face the same health challenges as other workers during the COVID-19 pandemic. As a result, permanent employees already striving to track social contacts are now surrounded by a large number of temporary workers.
To manage these periodic surges and maintain worker safety during the pandemic, Nutrien has launched Triax‘s Proximity Trace wireless safety solution. The system includes a wearable sensor that operates on a proprietary 900 MHz RF badge worn by all workers, along with gateways deployed at strategic locations, cloud-based software and a dashboard to manage proximity event data. The solution has been taken live at 18 of Nutrien’s industrial sites so far, and it is being expanded to additional locations, as well as to corporate offices. The technology features two key functions: alerting workers in real time if they are too close to each other, as well as capturing interaction data in the event that contract tracing is required.
Nutrien produces fertilizers and related products for agriculture, industrial and feed companies, generating more than 25 million tonnes (27.6 million tons) of potash, nitrogen and phosphate products annually, according to Gary Peterson, Nutrien’s IT director for nitrogen and phosphates. The firm operates NPK sites across North America and Trinidad. At each site, Nutrien’s facilities take raw commodity, such as mined materials—phosphates, nitrogen or potash—and converts it into industrial fertilizers
During the pandemic, Nutrien faces the same challenges as other companies: namely, tracking workers’ contacts to prevent infection transmissions, as well as alerting personnel to any infection risks. Early into the outbreak, Peterson says, the company began tracking such information manually. Nutrien has not only prioritized worker health and safety, he explains, but it secondarily strives to ensure no spread events can cause temporary shutdowns.
When it comes to turnaround events, Peterson explains, the manual method of contact tracing for thousands of workers, most of whom are there only temporarily, proved to be an impossible task. “We were scratching our heads,” he says, while anticipating the turnaround. So the company began seeking solutions ahead of the first planned maintenance of the COVID-19 era. It sought a technology-based solution that would be standalone, not integrated with its own networks, which could be easily and quickly deployed. It was also looking for simplicity in the management of the system and data.
“We looked at a few technologies and landed on Triax,” Peterson recalls. Last July, the company piloted the technology in a pre-turnaround setting at two sites, located in Lina, Ohio, and Borger, Texas, in the hope of proving the solution’s efficacy. Approximately 200 workers participated at the Borger site, and the system has since been used in multiple turnarounds.
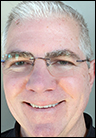
Gary Peterson
As workers report onsite, they are provided with an active 900 MHz RF badge, known as a TraceTag, according to John Goan, Triax’s director for energy and industrials. The tags are attached to workers’ clothing or hard hats, and the unique ID number encoded on each tag is linked to the individual to whom that badge is assigned. Data is stored in the Proximity Trace cloud-based software, and Nutrien’s safety and HR departments are responsible for managing that information in the Triax software.
As workers enter or leave specific parts of the site, a Triax gateway captures each badge’s ID and forwards that data to the server. The badges can continually transmit and receive transmissions to and from other badges as individuals work, and they can provide alerts with audio or visual notifications to those who come within 6 feet of one another. Users can silence the device temporarily when necessary, Goan says, adding, “It’s not intended to be an annoyance.”
Some people, for instance, may need to work in close proximity to one another and would not want the alerting distractions. On the other hand, some may require the alerting function. The visual indication is a flashing LED and the audio is configurable at up to 80 decibels in a noisy environment, down to an unobtrusive beep. When users receive an alert, they can then simply step back and the alert will cease.
The badge stores that data, and when the individual comes within range of a gateway, the collected information is forwarded to the gateway and then to the software, where it can be stored. The system is also designed for contact tracing, in order to minimize the risk of the company having to shut down operations. If someone tests positive for COVID-19, they can report that information to the company, and the HR or safety representative can then run a contact trace report for that user to identify all close contact interactions they had over a period of time.
Triax has offered its RF-based wireless technology for more than four years, and it has modified the solution to meet the unique demands of the pandemic era, with the Proximity Trace system for COVID-19 safety. However, Goan says, the solution is intended to provide benefits long after the pandemic has ended. “We repurposed our existing worker wearable,” he states, “with the intent of making sure that once COVID-19 was no longer priority-one, our customers could continue to gain value [from the technology].”
The device is approximately the size of a pager. To date, Goan reports, around 60,000 such devices have been deployed by companies in North America to ensure workplace safety during the pandemic. The cloud-based dashboard can be accessed by site managers and safety personnel, as well as by managers who want to see how sites are performing with regard to worker safety. This enables the company to identify any employees who might need to be retrained, so as to reduce the risk of contacts.
Nutrien’s pilots ended in July 2020, then rollouts began across its sites in late summer. Since the system was taken live, Peterson reports, “We’ve shown a reduced number of contacts onsite.” In fact, he says, simply wearing the badge has changed worker behaviors. “Most importantly, when there has been an issue onsite, we’ve been able to run an automated contact trace,” enabling the company to identify anyone who might be at risk of infection.
The system is not intended to track workers’ movements or locations, Peterson says, adding, “We are very conscientious of worker privacy.” The company made a point to instruct its staff that the system was intended only for the purpose of preventing or addressing any COVID-19 transmission quickly. “We made sure people were aware this is not Big Brother—it’s just a safety initiative—and because we put it in that perspective, it was well-received.” In fact, he adds, the workers appreciated the technology.
Following the system’s use at one turnaround, the firm launched it at others as well, in addition to making the technology available to permanent personnel. The solution is now live at 18 nitrogen and phosphate production sites, and three corporate offices are deploying it as well, with a potash site taking the system live this month. Nutrien has more than 8,000 employees using the technology, while 6,500 more are expected to begin utilizing the system in the near future. So far, Peterson reports, the company has been able to support as many as 1,700 employees and contractors at its nitrogen and phosphate sites.
Two more large turnarounds at nitrogen sites are scheduled to take place this year, as well as two smaller ones at phosphate sites. In the long term, Peterson says, while COVID-19 safety for turnarounds is the primary focus, the technology could be used for other purposes. “If we wanted to add other services,” he states, “we could do that—but our focus is on safety.” When it comes to social distancing, he adds, “We found, in many cases, when we ran [contact-tracing] reports, there was minimal or no exposure.”