The time-sensitive events business requires a high degree of organization—missing or broken rental items can actually ruin an event, and the company running it has only one chance to get it right for its customers. To reduce the risks of such setbacks, a German company that organizes more than 1,000 events for corporations across Europe each year has RFID-tagged approximately 50,000 items it rents to clients for parties, company events, shows or trade fairs.
“We are constantly battling the clock and wondering if we have the right equipment at the right place,” says Christian Seidenstuecker, CEO of Joke Event, based in Bremen. “If we mess up, we don’t make any money, and we damage our image.”
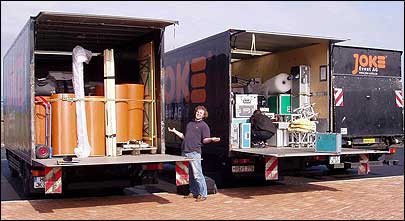
Seidenstuecker and his company were approached by the Bremer Institut für angewandte Betriebstechnik und Arbeitswissenschaft (BIBA), an institute at the University of Bremen, about using radio frequency identification to track the rental items it stores in its warehouse, such as chairs, lounge furniture, loudspeakers and cutlery. BIBA analyzed Joke’s business processes and designed an RFID system that was implemented in May 2007 at the company’s 3,800-square-meter (40,900-square-foot) warehouse. The system is integrated into Joke’s ERP software so project managers can inform clients immediately if, for instance, the right set of high-top tables is available for a particular event. In the past, a project manager would first have to contact the warehouse, and it would take 20 to 30 minutes to receive an answer for the customer.
Such increased warehouse visibility regarding Joke Event’s inventory helps to boost the company’s sales potential, but the application also has other benefits, Seidenstuecker told attendees at the RFID Journal LIVE! Europe conference, held in Prague in early November. It can also be utilized to track the use and repair status of individual items, speed up the truck-loading process, provide additional instructions for workers assembling the items at an event site, expedite billing processes by tracking the time an item was actually used by a client and allow Joke to respond quickly and flexibly if a client makes changes.
One frequent change is a last-minute request to accommodate additional guests at an event. “If more guests than expected are coming,” Seidenstuecker explained, “we can quickly select additional items and create new loading lists.”With the EPC Gen 2-based RFID system, warehouse employees receive an electronic work order on their Wi-Fi-enabled handheld computers, which tells them which items to pick from the shelves, and the best order for loading them. This helps other workers who have to set up the equipment at the site where the event is being held; the supplies are loaded in such a manner that enables them to be unloaded in the order in which they will be needed.
At the shelf, a worker employs a handheld to interrogate the item’s tag to ensure that the proper item is picked. It is then brought to a staging area within the warehouse. Smaller goods, such as cutlery, are packed in boxes, tagged in bulk and weighed to ensure the correct number has been picked. Joke has about 50,000 untagged small items. For individually tagged items, weight is irrelevant. All items required for that particular event are placed on trolleys, which are then wheeled past one of three portal readers installed at the warehouse dock doors.
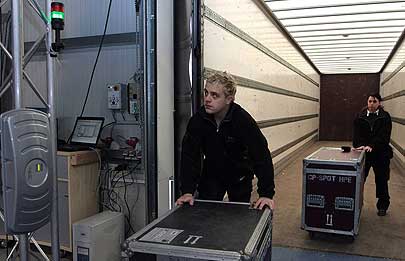
Motion sensors inform the system whether goods were rolled into or out of the warehouse. The system shows a green light if all of the appropriate goods are identified. An RFID tag supplied by Deister Electronic is attached to the top rear door of each of Joke’s eight delivery trucks, so the same dock-door interrogators can ensure that the proper equipment is being loaded on the right truck. When Joke rents additional trucks for an event, workers use double-sided tape to attach a tag to each rented vehicle.
At the event site, staff members can use handheld computers with a built-in RFID interrogator to read each item’s tag, and to retrieve additional information about, for example, how to assemble a lighting system or stage. Once the equipment is broken down following an event, employees employ the handheld devices to scan the tags on the objects headed back to the warehouse, and broken items are logged out of the system so they cannot be reserved for other events. The system is then updated regarding each item’s availability. Eventually, Joke plans to record the items’ repair status as well.
“We now know when a truck is headed to Bremen with three missing chairs,” Seidenstuecker told the audience at RFID Journal LIVE! Europe, noting that his company may also add GPS tracking for the trucks.
In addition, the system offers an employee ID feature that tracks work time via RFID. Before starting and after finishing the loading process, employees utilize individual RFID badges instead of entering a PIN code to identify themselves.According to Seidenstuecker, some of his 58 permanent staff members and 85 freelancers were hesitant about using the new technology until they realized it was being utilized to improve how the company works, rather than to eliminate jobs. Now, he said, they frequently suggest how to improve the use of the system.
One major problem the company faced when implementing the RFID system involved how to tag such a wide variety of items composed of different materials. The project partners solved this dilemma by using five different types of RFID tags, each of which were tested for their compatibility with the items tagged, such as metal boxes, wooden chairs or plastic articles. LogDynamics Lab, located in Bremen, together with the RFID Service Center Bremen, helped with the tests.
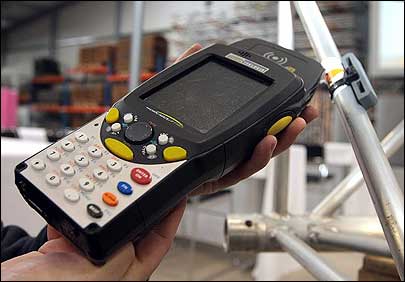
All of the handheld computers are manufactured by Psion Teklogix. Those used remotely include a UMTS card for connecting to the company’s server. The tags attached to items are made by Confidex, Innotech Resources, KSW Microtec and Sandstone Technologies Group. Tag cost ranged from 40 cents to €5 ($6.45) apiece for special tags.
“We reuse some of the tags, so we could spend more for higher-quality tags,” Seidenstuecker told attendees. Looking forward, Joke is considering the addition of active RFID tags with sensors for tracking sensitive equipment, such as LCD projectors and moveable lights. The company is also working to expand the application to all of its 100,000 items.
Seidenstuecker said his company invested a six-figure sum in the application and expects to recover that amount within two years, through cost savings and higher productivity.