Editor’s Note: This article was original published in January 2023
Taiwanese natural gas and petroleum company CPC Corp. is managing its high-value product—drums of chemicals used to process petroleum or refined gas—with a radio frequency identification (RFID) solution provided by EPC Solutions Taiwan. The system was built and deployed last year to automatically identify each filled drum as it is received, weighed, stored and shipped. The solution required a hybrid approach to ensure connectivity to a server in an area lacking Wi-Fi coverage.
EPC Solutions incorporated LoRa technology into the system to wirelessly forward RFID tag-read and scale-weight data to software hosted on the company’s server. With the technology in place, CPC reports that it can now prevent identification errors and ensure products are never lost due to unauthorized movement. In the long run, the energy company expects to reduce manual labor that was previously required to track and record data regarding each drum.
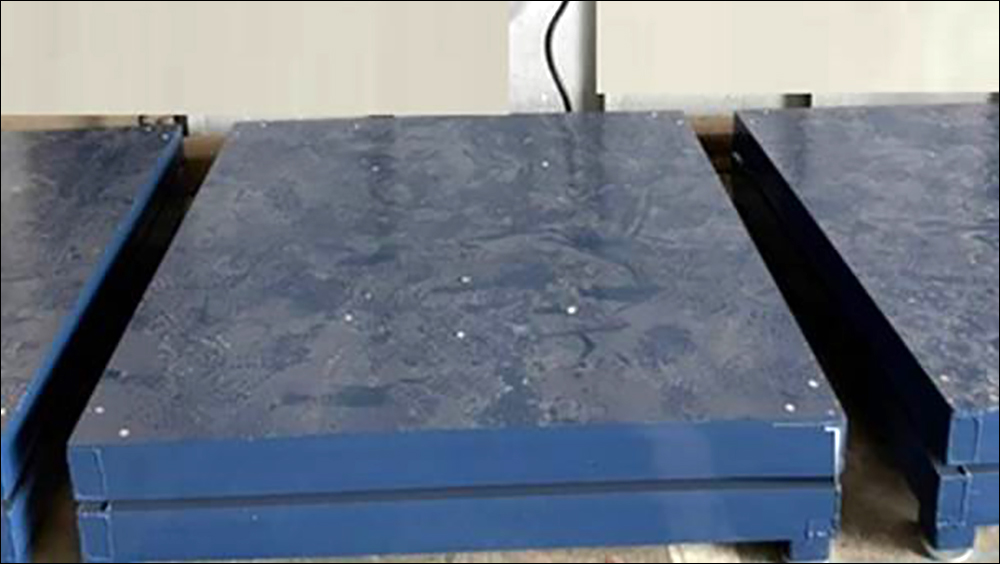
The company deployed 51 five-ton scales, like the ones pictured here.
CPC Corp. is a 70-year-old petroleum business that serves much of Taiwan’s energy industry. The firm provides petroleum-based energy throughout the country, including exploration, production, procurement, imports, refining, storage, transportation, marketing, sales, and the production of petrochemical raw materials.
CPC first approached EPC Solutions in May 2021 with a challenge related to managing the petroleum chemical catalyst used for processing, according to JK Wu, CPC’s RFID project manager. The catalyst product is leveraged by CPC and its customers to speed up chemical reactions related to transforming the petroleum into a liquid fuel. “While in the past, we manually recorded the quantity and weight of each drum,” Wu recalls, “that was inefficient and error-prone.”
EPC Solutions, launched in 2002, is a full solution provider for customized RFID solutions in Taiwan and Hong Kong. “We provide hardware, software and overall solutions for the Internet of Things industry,” says Aden Yin, EPC Solutions’ manager.
Managing High-Value Petroleum Catalyst
CPC’s drums are stored in a total of eight warehouses. The company requested a custom solution that would enable automated management of the filled drums as they are received, weighed, and then shipped to refineries or other production sites. CPC wanted to maintain a record indicating the warehouse location in which each drum was stored, as well as the weight of each pallet of drums, and the weight of the individual drums themselves.
Typically, one to four drums are loaded onto each pallet, stacked in one or two layers. The traditional method of managing the drums was a manual one. Workers had to walk up to each drum as it was received and read a serial number printed on it. They then manually keyed that number into an Excel spreadsheet stored on the company’s server. When the drum was weighed, they also keyed the weight into the spreadsheet, along with other details, such as where in the warehouse the drum could later be found.
This process was time-consuming and prone to errors, Wu says. Once a year, inventory was manually counted in the warehouse, and the company found discrepancies in the counts, such as missing drums that had not been identified as having been shipped out. To solve the problem, the company initially opted to deploy the RFID technology at a single warehouse, which covers an area measuring 80 meters by 30 meters (262 feet by 98 feet). CPC wanted to know not only when each drum arrived and how much it weighed, but also where it was stored and when it was shipped, so that it could prevent errors and ensure accountability.
Installation began at the Tao Yuan-based facility in November 2021, Yin says, and was completed in April 2022. The system was taken fully live in August. EPC Solutions provided UHF RFID technology to identify every drum and the pallet on which it was stored. The company selected its passive LH-7030 Flexible on-metal UHF RFID tag, which is affixed to each drum and pallet via an adhesive. A total of 500 tags were initially used.
To read the tags, EPC Solutions installed two of its own HLR-CW400 RFID readers onsite, each with four antennas. The company also deployed two cameras and 51 five-ton scales. EPC Solutions’ software manages the collected data on CPC’s server. Additionally, the company deployed a single LoRa gateway and 51 LoRa dongles that transmit long-range data at a range of up to 600 meters (1,970 feet), from the RFID readers and weigh scales to the company’s server.
How the System Works
The solution required tag identification at two locations: where the goods are received and weighed, and where they are weighed and shipped. Due to the highly metallic and crowded environment, EPC Solutions Taiwan needed to customize the system to prevent stray reads of pallets or drums within the reader’s vicinity. To accomplish this goal, the company built a metal mesh shielding area around both readers.
The catalyst chemical arrives from vendors in metal drums. At that time, CPC’s operators apply a single RFID tag to each drum and link that tag’s unique ID number to the order in the software. They also apply an RFID tag to the pallet on which the drums are loaded. All tags are then linked together in the software. In the future, CPC expects to require vendors to apply tags to the drums before they are shipped to its warehouses.
Once the drums are received, palletized and tagged, warehouse forklift operators transport each pallet through the shielded tag-reading portal, where the RFID tags are read. The data is then forwarded to the software. That includes the unique ID of the pallet, married to the ID number of each drum tag. One scale is dedicated at this location for weighing pallets, and the weight of the fully loaded pallet is linked to the tag IDs and stored in the software.
Typically, the drums are next removed from the pallet and transported to one of 50 scales intended to individually weigh the drums. Each scale comes with a LoRa dongle transmitter. As a drum is placed onto the scale, its weight is linked to the tag ID and forwarded via the LoRa gateway. Each scale used to weigh the drums is dedicated to a specific section in the warehouse, so the data indicates where every drum is being stored.
When an order is placed for specific drums, a forklift operator proceeds to the warehouse to locate and pick those drums and load them onto a shipping pallet. They then drive the forklift through a second shielded RFID reader intended for shipping purposes. The weight and the RFID tag IDs are read, and the software compares that data against the order to ensure the proper drums are being loaded.
If an error is being made, or if a drum is being moved in an unauthorized manner or at the wrong time, the system detects that action and prompts an alarm to be sounded. The cameras installed at the RFID gate areas take pictures of the event as it is taking place, for back-up details in the event of an alarm.
Deploying LoRa for Long-Range Connectivity
The use of LoRa technology with the RFID system was a first for EPC Solutions, the company reports. Because there was no access to Ethernet networks onsite, the system would require wireless coverage, but the Wi-Fi signal was not reliable. The company’s engineers tested and deployed the LoRa system, using dongles and a single gateway to ensure the technology would remain cost-effective.
Going forward, CPC intends to install four ultra-wideband (UWB) anchors on the roof of the warehouse, as well as UWB tags on each of its forklifts. In that way, the energy company will be able to track the location of every operator and better manage dispatch assignments to ensure an efficient, safe process for warehouse workers. That feature is slated to go live later this year.
In the meantime, CPC reports that it has accomplished its primary goal, which was to ensure efficient, error-free processing and shipment. With the RFID and LoRa technology in place, Wu says, “The system helps us not only take correct data, but also send the data to a remote server through LoRa communication without deploying an Ethernet network.”
Key Takeaways:
- CPC Corp. employs an RFID system to identify pallets and drums as they enter and leave its storage facility, while LoRa provides an alternative to Wi-Fi or cellular networks by sending weight data to the server.
- EPC Solutions Taiwan built a shielded RFID reading system to ensure accurate and reliable tag reads as drums enter and leave the active and crowded site.