While most retailers are putting RFID to the test for pallet-, case- and sometimes item-level product tracking, Cost Plus World Market (CPWM), a large specialty retailer of food, furniture and other home goods, is using the technology in a different way. CPWM is employing an RFID-based real-time location system (RTLS) to monitor its fleet of trailers at its main distribution center in Northern California.
Cost Plus World Market operates nearly 300 stores in 34 states, with a reported 2007 revenue of over $1 billion. The retailer has begun tracking the 75 trailers in its fleet using the Yard Hound yard management system made by PINC Solutions, based in Berkeley, Calif. The system utilizes passive EPC Gen 2 RFID tags encased in rugged housing and permanently mounted onto the trailers.
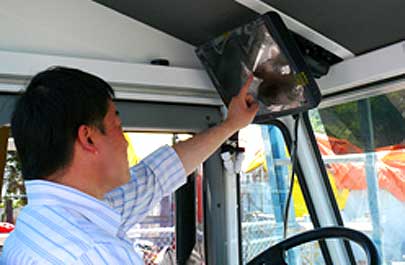
An RFID interrogator built into the yard’s entrance gate reads the tag of an arriving trailer. Once that trailer has entered the yard, its tag is read by an RFID interrogator built into PINC’s Tracker appliance, which is mounted inside a yard truck, also known as a shunt truck, used to reposition trailers within the yard. As the truck moves through the yard, it passes within range of the trailer’s tag and its Tracker collects the tag ID, associating it with the location coordinates determined by its built-in GPS receiver.
Because the truck is in motion, the Tracker appliance also contains inertial sensors to measure the yard truck’s movement in relation to stationary trailers. The sensors measure such things as the yard truck’s acceleration and rotation. This data, along with the signal strength of the tag reads, is plugged into algorithms developed by PINC, to pinpoint each trailer’s location.
The Tracker stores the trailer’s location data, along with a time stamp, and sends that information to PINC’s Web-based software platform as soon as the appliance is in range of one of the yard’s Wi-Fi (802.11) access points. PINC’s server collects the information from the various yard trucks as they arrive, merges that data with a map of the facility, and presents a real-time picture of activities in the yard.
CPWM yard personnel access this map by logging onto the Yard Hound software, linked to the company’s yard management system, which includes each trailer’s shipping manifests. This way, each worker sees not only the trailer’s ID number, but also information about the products being carried within. CPWM can set the Yard Hound software to trigger alarms if, for instance, a specific trailer is not moved to an unloading dock within a given timeframe once it enters the yard’s trailer storage area. This feature is designed to ensure that seasonal product is unloaded and distributed according to schedule, or that perishable goods stored in a refrigerated trailer are processed before they spoil.Using the PINC system, the retailer says, has improved its DC yard efficiency and reduced costs by automating many yard-management processes that were previously performed manually. While the company declines to discuss the deployment with RFID Journal, nor to release information about the precise time or labor savings the Yard Hound system has provided, PINC Solutions’ CEO, Aleks Göllü, says CPWM is seeing concrete benefits by taking advantage of the highest functionality Yard Hound offers.
According to Göllü, companies can choose to deploy a reader only at a yard’s main entrance, to automate the process of noting which trailers have entered the yard, and when. The second level of functionality includes adding the Tracker appliance to yard trucks in order to monitor the location of tagged trailers on a map of the yard. The third level, which CPWM has deployed, enables yard managers to exchange text and graphic messages with truck drivers over Wi-Fi, by means of a PINC software module running on a mobile touch-screen computer inside the yard truck.
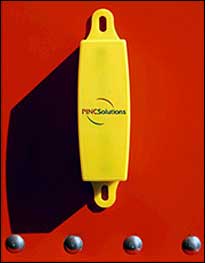
With this function, known as Yard Hound Director, CPWM yard managers can show drivers where they want each trailer placed by noting the desired location on the map. They can also use the map to request that a trailer be retrieved and brought to a specific dock bay. Drivers can tap the touch screen to confirm requests, and managers can ensure that the proper drivers move the correct trailers to their assigned locations by constantly updating the map view. If they see a yard truck heading in the wrong direction to pick up or drop off a trailer, they can send the driver an alert. Since all of these processes were previously done over radio and with a paper map, Göllü says, mistakes weren’t caught until much later.
Göllü says another PINC customer has been able to eliminate one of the yard trucks it had leased, based on the visibility afforded by the PINC system. The company found that one yard truck, used more efficiently, met its needs. “When you consider the labor, gas, maintenance and leasing costs of that extra yard truck, that’s savings of somewhere around $90,000 annually,” he explains. “And if your company has green [carbon-reduction] initiatives, [downsizing a yard truck fleet] helps with that, too.”
This same customer, Göllü adds, has also been able to reduce the number of manual yard checks—verification that all of the trailers are stored or docked where they are supposed to be—from six per day to just one. Such checks are conducted to audit the Web-based software, he says, adding that personnel spend 90 minutes on each manual check.
Göllü says another customer expects to reduce by 80 percent the late fees it typically pays for trailers that are kept inside its yards beyond their rental agreement. This customer, he notes, also hopes to reduce the number of empty trailers that sit inside the yard.